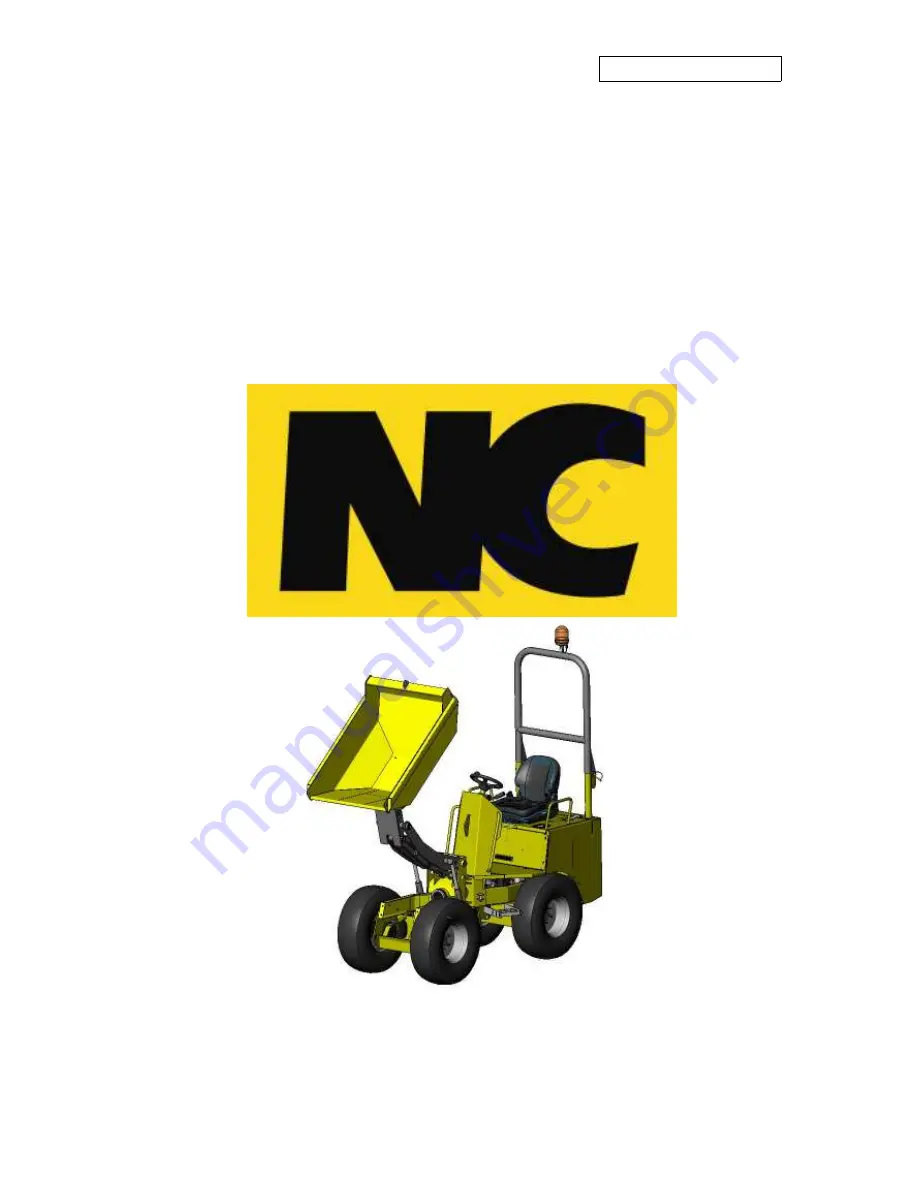
HT1.0 Site Dumper
HT1.0 Site Dumper
HT1.0 Site Dumper
HT1.0 Site Dumper
MAINTENANCE
MAINTENANCE
MAINTENANCE
MAINTENANCE
INSTRUCTION
INSTRUCTION
INSTRUCTION
INSTRUCTION
MANUAL
MANUAL
MANUAL
MANUAL
NC ENGINEERING (HAMILTONSBAWN) LTD
2 Killyrudden Road, Hamiltonsbawn, Co Armagh, BT61 9SF
Tel: 028 38871970 Fax: 028 38870362
email:
www.nc-engineering.com
REVISION B
ORGINAL
INSTRUCTIONS
Summary of Contents for HT1.0
Page 9: ...9 Technical Specifications...
Page 47: ...47...
Page 53: ...53...
Page 81: ...81 Fault Finding CHART E2 Noisy wheel motor...
Page 82: ...82 Fault Finding CHART E3 Wheel motor does not revolve...
Page 83: ...83 Fault Finding CHART E4 Wheel motor does not revolve at its normal speed under load...
Page 84: ...84 Fault Finding CHART E5 Wheel motor revolves irregularly CHART E6 Wheel motor leaks...