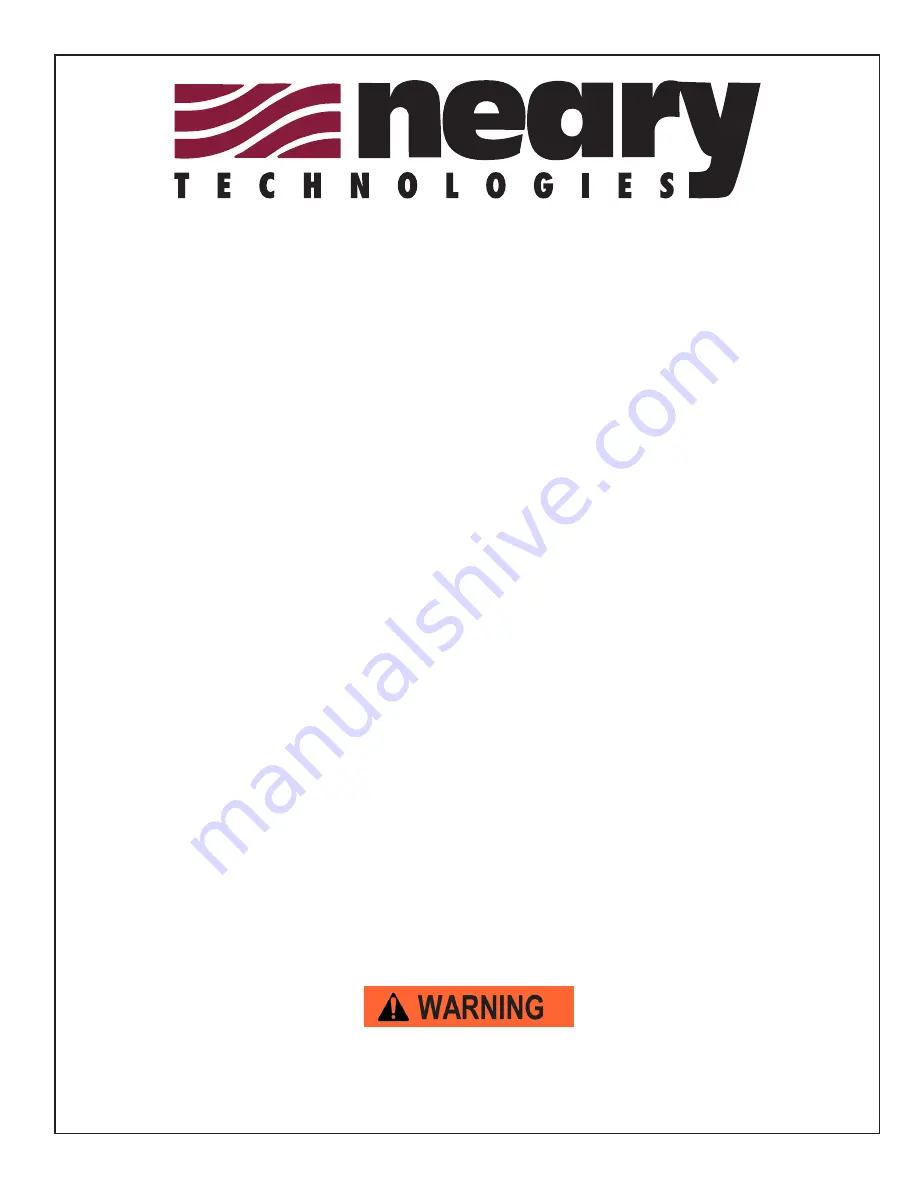
- ORIGINAL INSTRUCTIONS -
555
AUTO - INDEX
SPIN / RELIEF
REEL MOWER GRINDER
Patent No. 5,321,912
6,010,394 & 6,290,581
6,685,544 & 6,699,103
SERVICE
MANUAL
55013 (3-17)
You must thoroughly read and understand all manuals before operating the equipment,
paying particular attention to the Warning & Safety instructions.
Summary of Contents for 555 SRI
Page 42: ...42 ORIGINAL INSTRUCTIONS 55761 EXPLODED VIEW DOOR ASSEMBLY ...
Page 44: ...44 ORIGINAL INSTRUCTIONS 6329575 EXPLODED VIEW REAR GUARD DOOR ASSY ...
Page 46: ...46 ORIGINAL INSTRUCTIONS 6329575 EXPLODED VIEW REAR GUARD DOOR ASSY ...
Page 48: ...48 ORIGINAL INSTRUCTIONS 55583 EXPLODED VIEW GRINDING HEAD ASSEMBLY ...
Page 50: ...50 55451 EXPLODED VIEW PIVOT ARM GRINDING SHAFT ASSY 1 of 2 ...
Page 52: ...52 55451 EXPLODED VIEW PIVOT ARM GRINDING SHAFT ASSY 2 of 2 ...
Page 54: ...54 ORIGINAL INSTRUCTIONS 55563 EXPLODED VIEW TRAVERSE DRIVE ASSEMBLY ...
Page 56: ...56 ORIGINAL INSTRUCTIONS 55452 EXPLODED VIEW MOWER SUPPORT ASSEMBLY ...
Page 58: ...58 ORIGINAL INSTRUCTIONS EXPLODED VIEW VERTICAL MOWER SUPPORT ASSEMBLY ...
Page 60: ...60 ORIGINAL INSTRUCTIONS 55708 EXPLODED VIEW CARTON ASSEMBLY ...
Page 62: ...62 ORIGINAL INSTRUCTIONS EXPLODED VIEW ALIGNMENT GAGE ASSEMBLY ...
Page 66: ...66 ORIGINAL INSTRUCTIONS 55628 EXPLODED VIEW SPIN DRIVE ASSEMBLY 2 5 1 3 6 4 7 9 ...
Page 68: ...68 ORIGINAL INSTRUCTIONS EXPLODED VIEW CONTROLS ASSEMBLY ...
Page 70: ...70 ORIGINAL INSTRUCTIONS EXPLODED VIEW ELECTRIC PANEL SUB ASSEMBLY ...
Page 72: ...72 ORIGINAL INSTRUCTIONS 55041 WIRING DIAGRAM ...