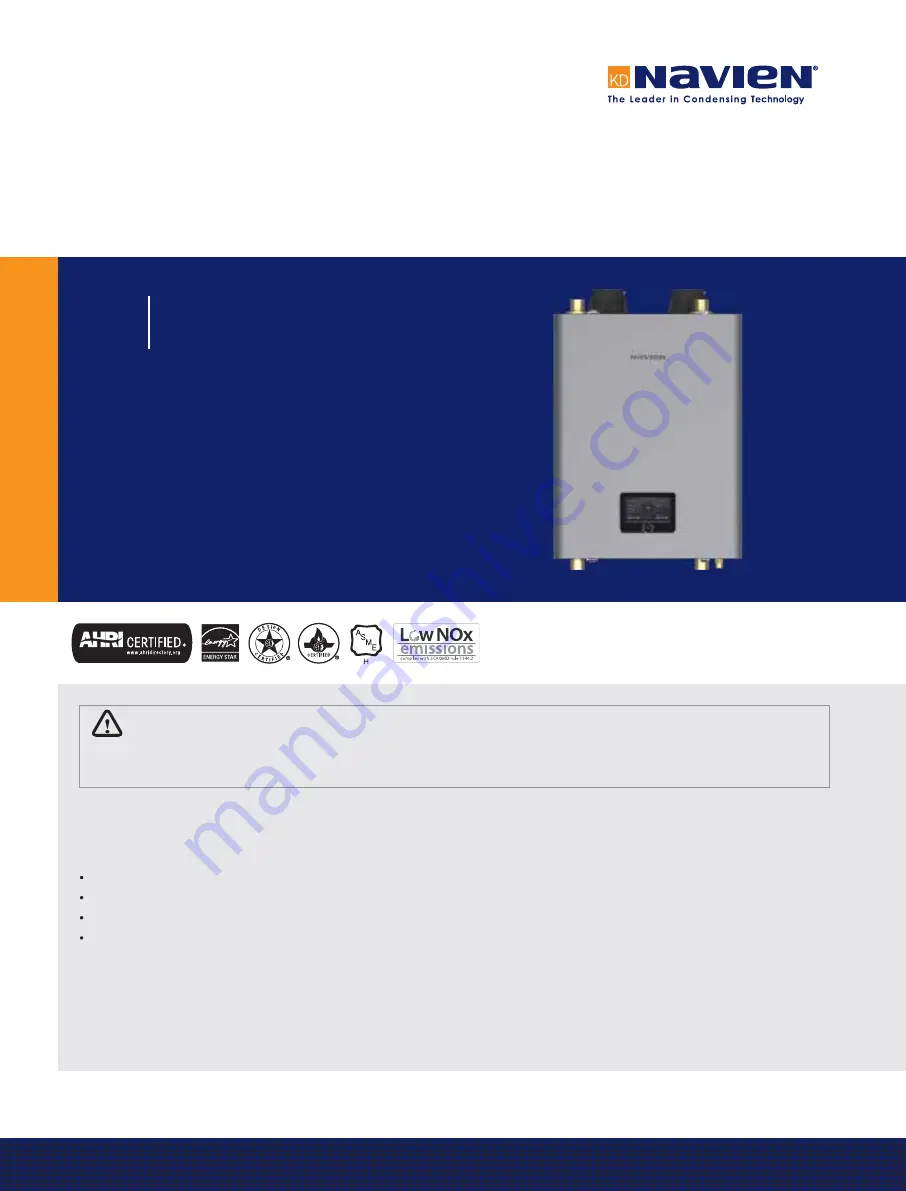
WARNING
If the information in these instructions is not followed exactly, a fire or explosion may result, causing
property damage, personal injury, or death.
Do not store or use gasoline or other flammable vapors and liquids in the vicinity of this or any other
appliance.
WHAT TO DO IF YOU SMELL GAS
Do not try to light any appliance.
Do not touch any electrical switch; do not use any phone in your building.
Immediately call your gas supplier from a neighbor’s phone. Follow the gas supplier’s instructions.
If you cannot reach your gas supplier, call the fire department.
Installation and service must be performed by a qualified installer, service agency or the gas
supplier.
The installation must conform with local codes or, in the absence of local codes, the National Fuel
Gas Code, ANSI Z223.1/NFPA 54 and/or CSA B149.1, Natural Gas and Propane Installation Code.
Keep this manual near this boiler for future
reference whenever maintenance or service
is required.
Installation & Operation Manual
NFB Condensing Boilers
Model
NFB-301C
NFB-399C
Summary of Contents for NHB Series
Page 120: ...120 Appendixes 12 6 Component Assembly Diagrams and Part Lists 12 6 1 Case Assembly NFB 301C...
Page 122: ...122 Appendixes 12 6 2 Case Assembly NFB 399C...
Page 124: ...124 Appendixes 12 6 3 Heat Exchanger and Waterway Assembly NFB 301C...
Page 126: ...126 Appendixes 12 6 4 Heat Exchanger and Waterway Assembly NFB 399C...
Page 128: ...128 Appendixes 12 6 5 Combustion Parts Assembly NFB 301C...
Page 131: ...131 Appendixes 12 6 6 Combustion Parts Assembly NFB 399C...
Page 134: ...Memo...