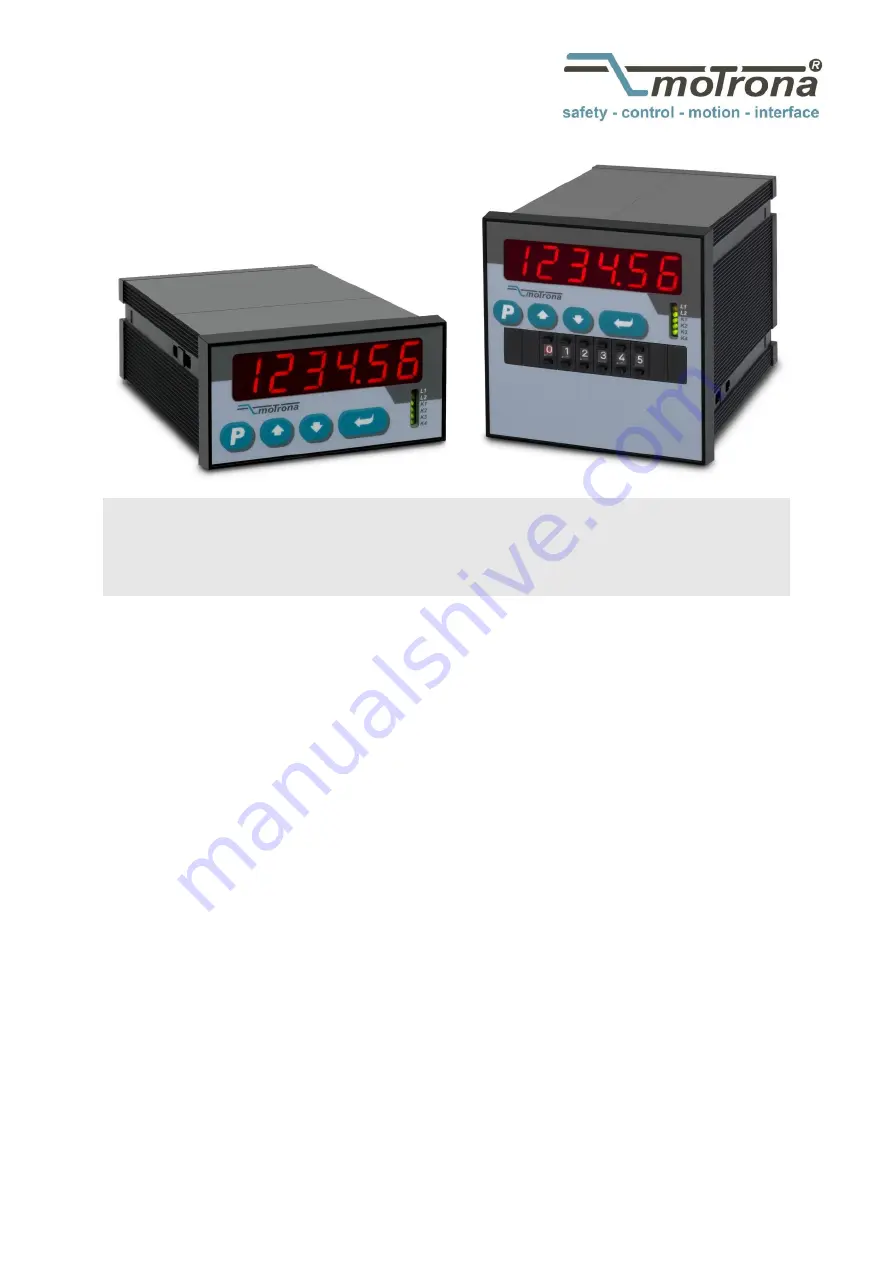
Operating Manual
motrona GmbH, Zeppelinstraße 16, DE - 78244 Gottmadingen, Tel. +49 (0) 7731 9332-0, Fax +49 (0) 7731 9332-30, [email protected], www.motrona.com
FS340 / FS641
High Performance Low Cost Controller for Control Tasks
with Flying Shears and Saws
Product Features:
•
Easy parameter setting and immediately ready to work
with minimum commissioning time
•
High accuracy due to high feedback frequency range of 300 kHz with
TTL encoders and 200 kHz with HTL encoders
•
Extremely smooth motion by optimized S-shape profiles
•
High dynamic response by means of short cycle time, therefore accurate cutting
results also during change of line speed
•
Most compact unit including operator panel for direct access and
RS232 interface for remote access
•
Analog output - configurable for voltage or current operation
•
PROFIBUS DP interface available (option)
•
24 VAC / 17 … 40 VDC power supply
Available Devices:
•
FS340: Controller with setting of the cutting length by keypad, 14 bits analog
output and 4 power transistor outputs for alerts
•
FS641: Controller with features like FS340, but additional front thumbwheel
switches for cutting length and 4 relay outputs for alerts