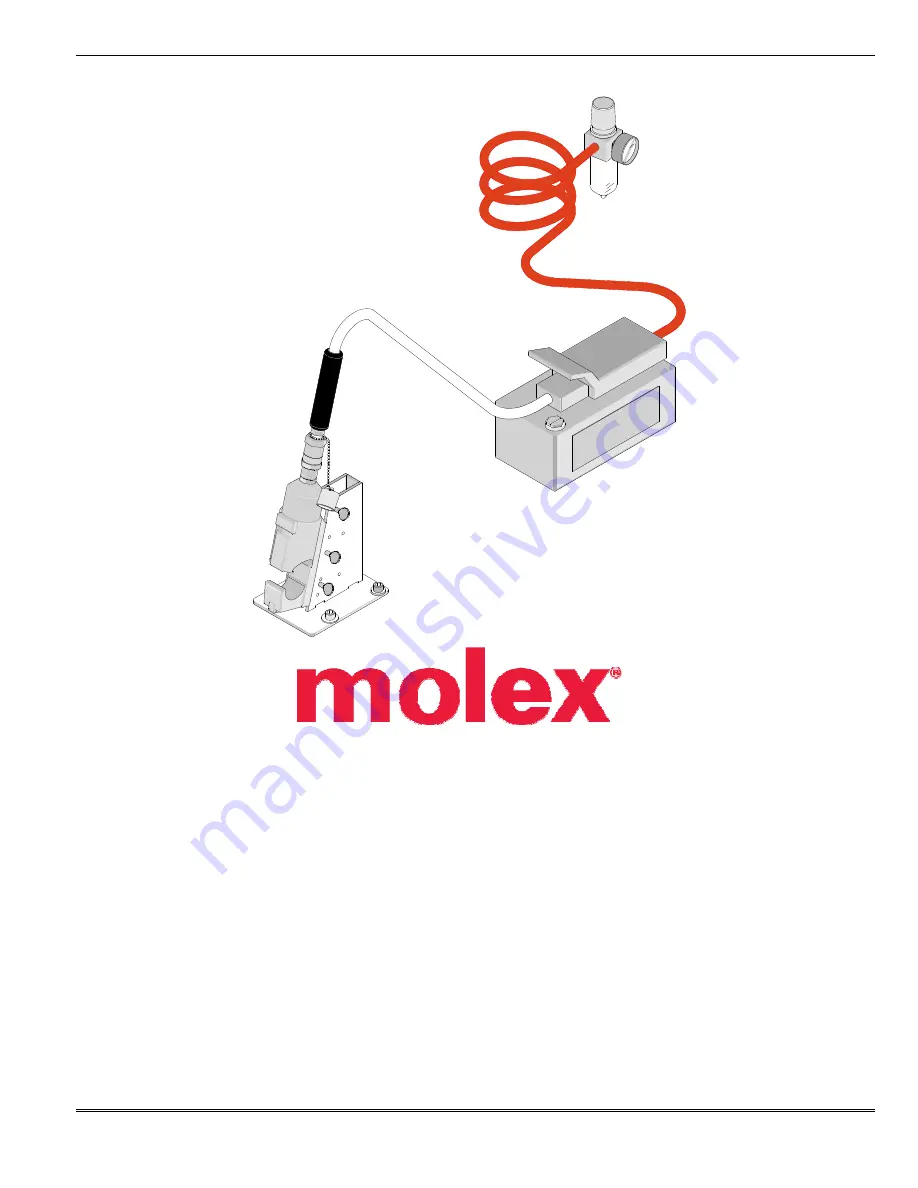
MagKrimp™ Hydraulic Head Crimper
Doc No. TM-190780422
Release Date: 03-21-14
UNCONTROLLED COPY
Page 1 of 22
Revision: A
Revision Date: 03-21-14
MagKrimp™ Hydraulic Head Crimper
(With Optional Bench Mounting)
Operation Manual
Order No. 19078-0422
For MagKrimp
Products Taps, Butt, and Parallel Splices and Terminals
(Up to 230,000 Circular Mill Area)
Description
Operation
Maintenance