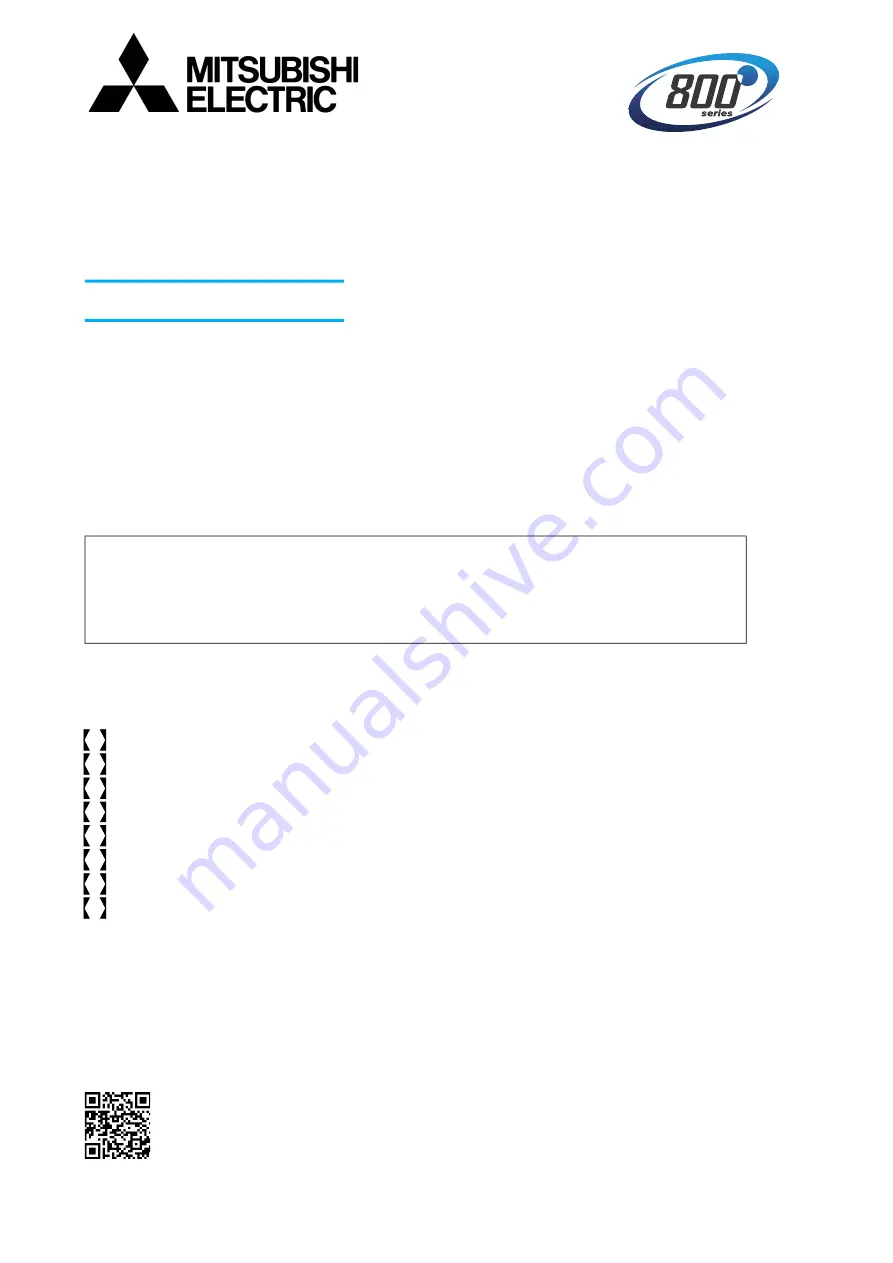
INVERTER
FR-A800 Plus
INSTALLATION GUIDELINE
FR-A820-00046(0.4K) to 04750(90K)(-E)-R2R
FR-A840-00023(0.4K) to 06830(280K)(-E)-R2R
FR-A842-07700(315K) to 12120(500K)(-E)-R2R
Roll to Roll Function
A
800
CONTENTS
INSTALLATION AND INSTRUCTIONS ................................................................................ 1
WIRING................................................................................................................................ 5
FAILSAFE OF THE SYSTEM WHICH USES THE INVERTER...............................................24
PRECAUTIONS FOR USE OF THE INVERTER....................................................................25
BASIC OPERATION ...........................................................................................................27
TROUBLESHOOTING........................................................................................................45
SPECIFICATIONS ..............................................................................................................48
APPENDIX ........................................................................................................................55
Thank you for choosing this Mitsubishi Electric Inverter.
This Installation guideline and the enclosed CD-ROM give handling information and precautions for use of this
product.
Do not use this product until you have a full knowledge of the equipment, the safety information and the
instructions.
Please forward this Installation guideline and the CD-ROM to the end user.
Version check
Art. No. 473174
12082019
Version B