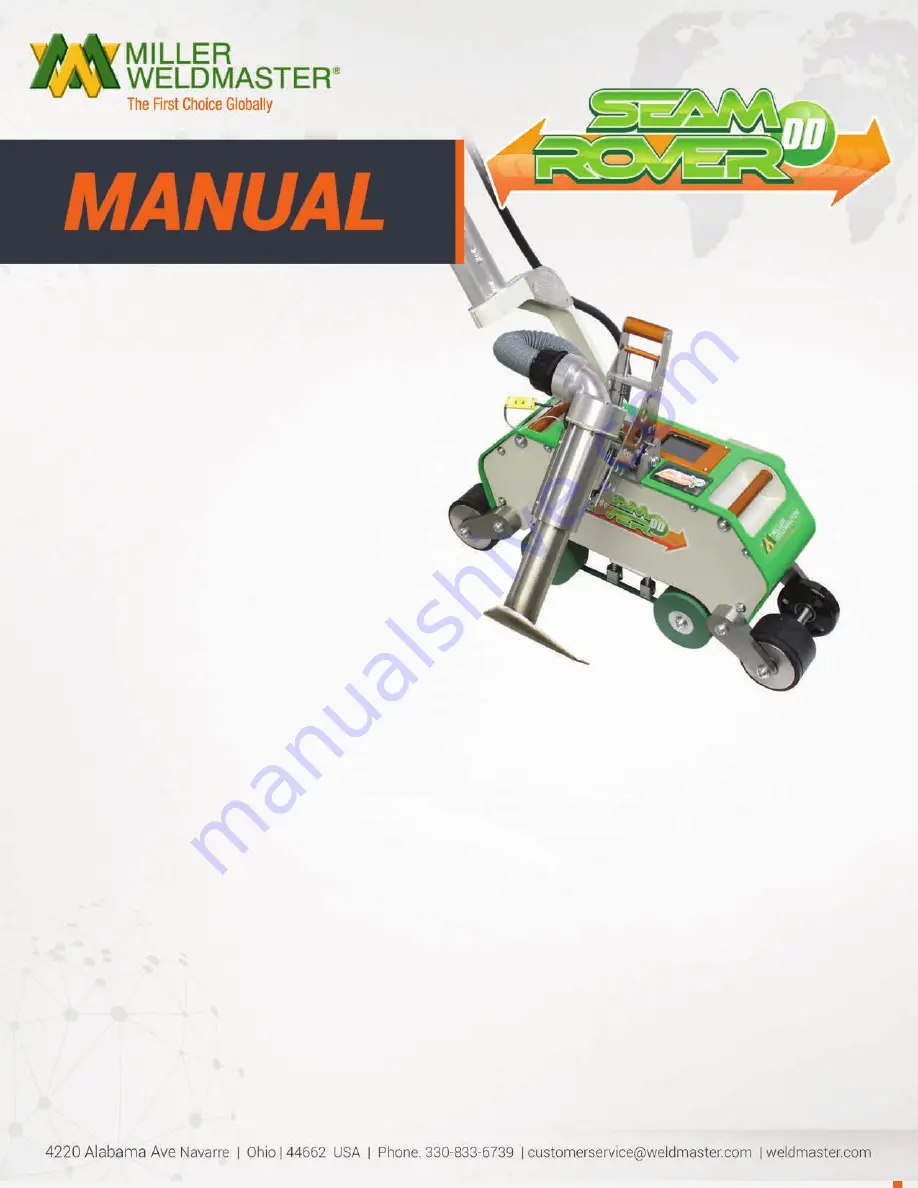
Instruction Manual
Page 1
This instruction manual is intended to be a guide when operating the Seamrover DD. To ensure optimal
performance from your welder, please follow the recommendations and specifications precisely.
You can also subscribe to Miller Weldmaster Insiders to stay updated on tech tips, machine maintenance
updates, and more at www.weldmaster.com/insiders.