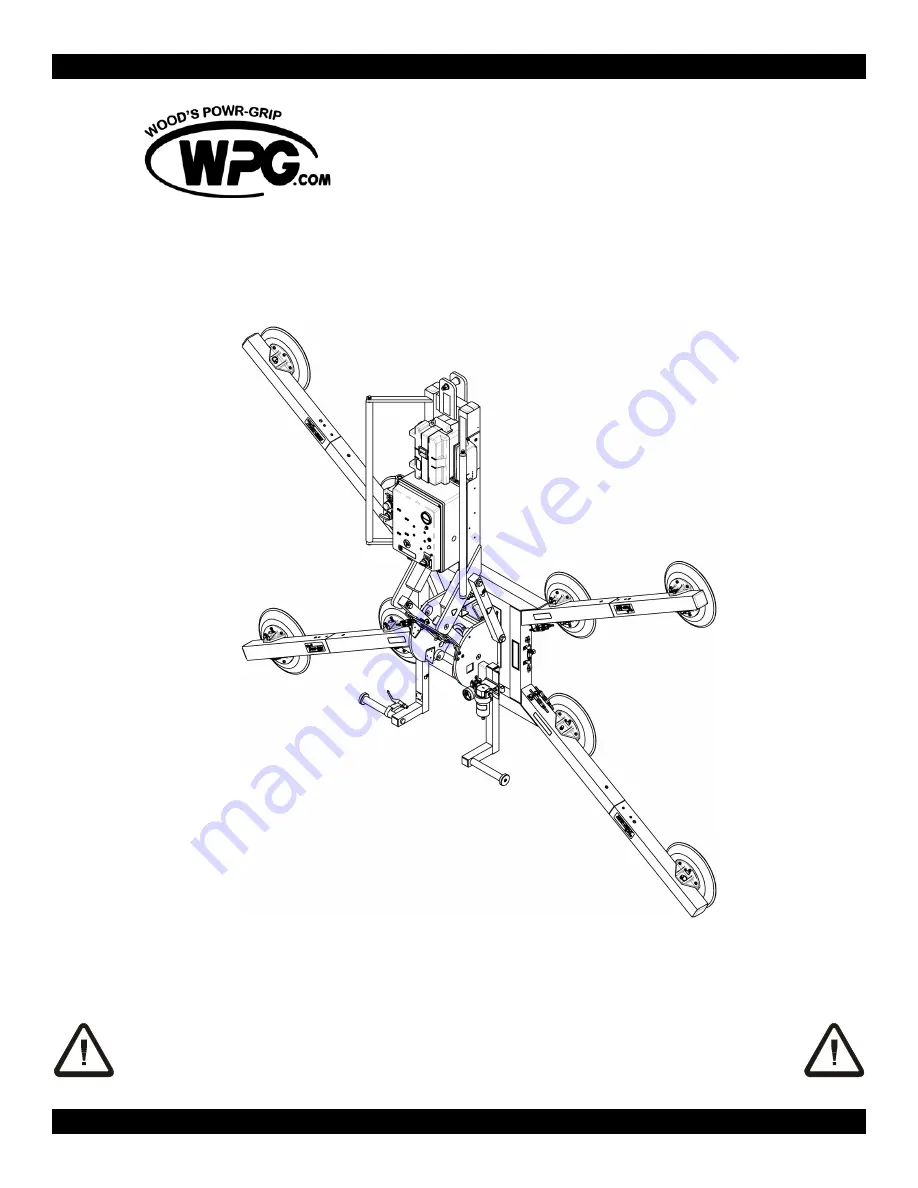
KEEP FOR FUTURE REFERENCE
INSTRUCTIONS
International Version
MODEL NUMBERS: MRTARC8HV11DC,
MRTARC811LDC
SERIAL NUMBER: ___________
(please see serial label and record number here)
QUADRA-TILT ROTATOR
DC-VOLTAGE, HIGH-FLOW, WITH PENDANT
READ ALL INSTRUCTIONS AND WARNINGS
BEFORE OPERATING THIS LIFTER
DESIGNED FOR THE MATERIALS HANDLING PROFESSIONAL
P.O. Box 368 – 908 West Main
Laurel, MT USA 59044
phone 800-548-7341
phone 406-628-8231
fax 406-628-8354
Summary of Contents for MRTARC811LDC
Page 2: ......
Page 42: ...Rev 5 2 9 16 40 MRTARC8 DC 35076RC ...
Page 43: ...Rev 5 2 9 16 41 MRTARC8 DC 35076RC ...
Page 44: ...Rev 5 2 9 16 42 MRTARC8 DC 35076RC ...