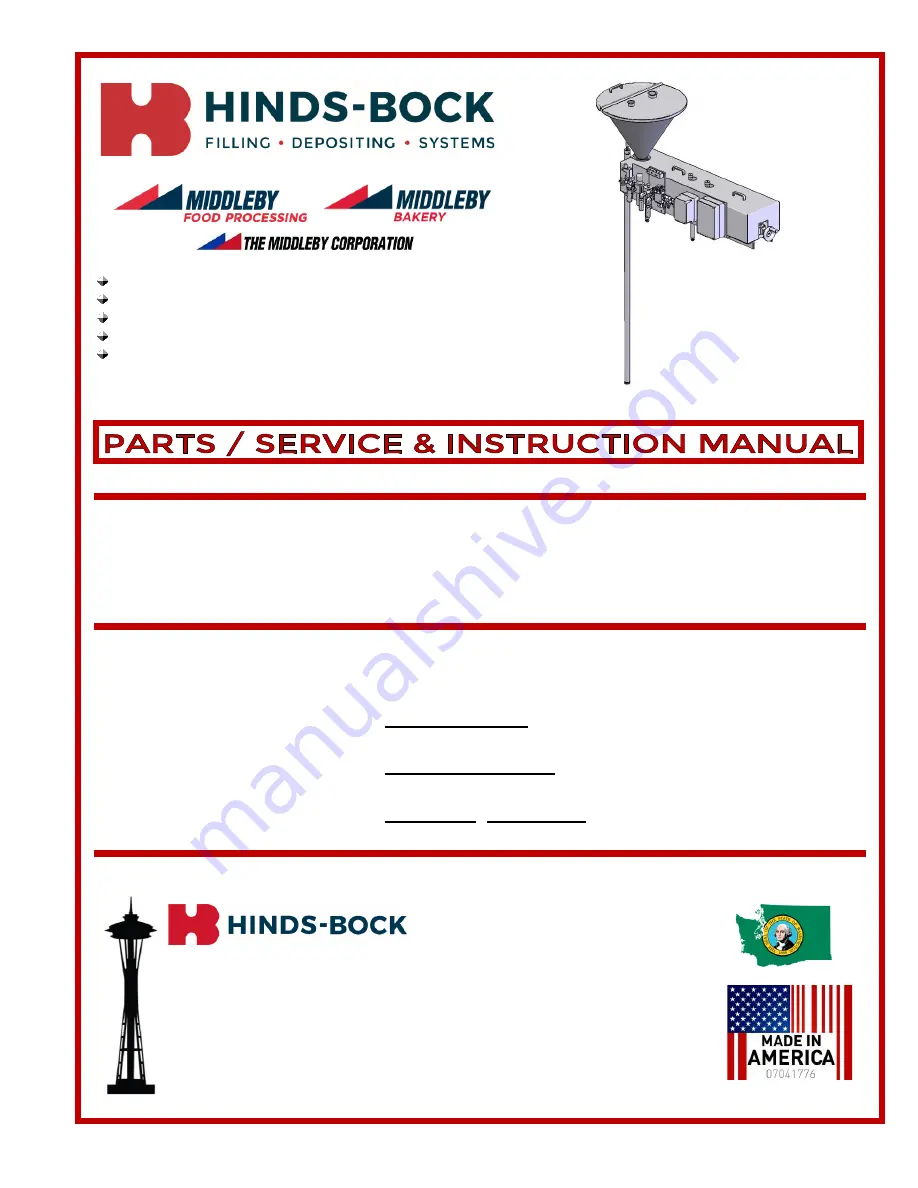
PACIFIC FRUIT PROCESSORS, INC.
SOUTH GATE, CA | USA
SINGLE PISTON FILLER/DEPOSITOR
MODEL No.: SP-64B
SERIAL No.: 0005537
MFG. DATE: MAY 2007
2122 - 222
nd
Street S.E. | Bothell, WA 98021-4430 | U.S.A.
TEL
425.885.1183
TEL:
877.292.5715 (MAIN
–
TOLL FREE)
TEL:
888.557.7881 (PARTS DEPARTMENT
–
TOLL FREE)
FAX:
425.885.1492 (MAIN)
FAX:
425.897.4110 (PARTS DEPARTMENT)
WEB:
www.HINDS-BOCK.com
E-MAIL: SALES INFORMATION:
PARTS:
Air Piston & Servo Filling / Depositing Systems
Air Piston & Hydraulic Transfer Pumps
Spotters & Stripers
Icers & Glazers
Custom Integrated Designs