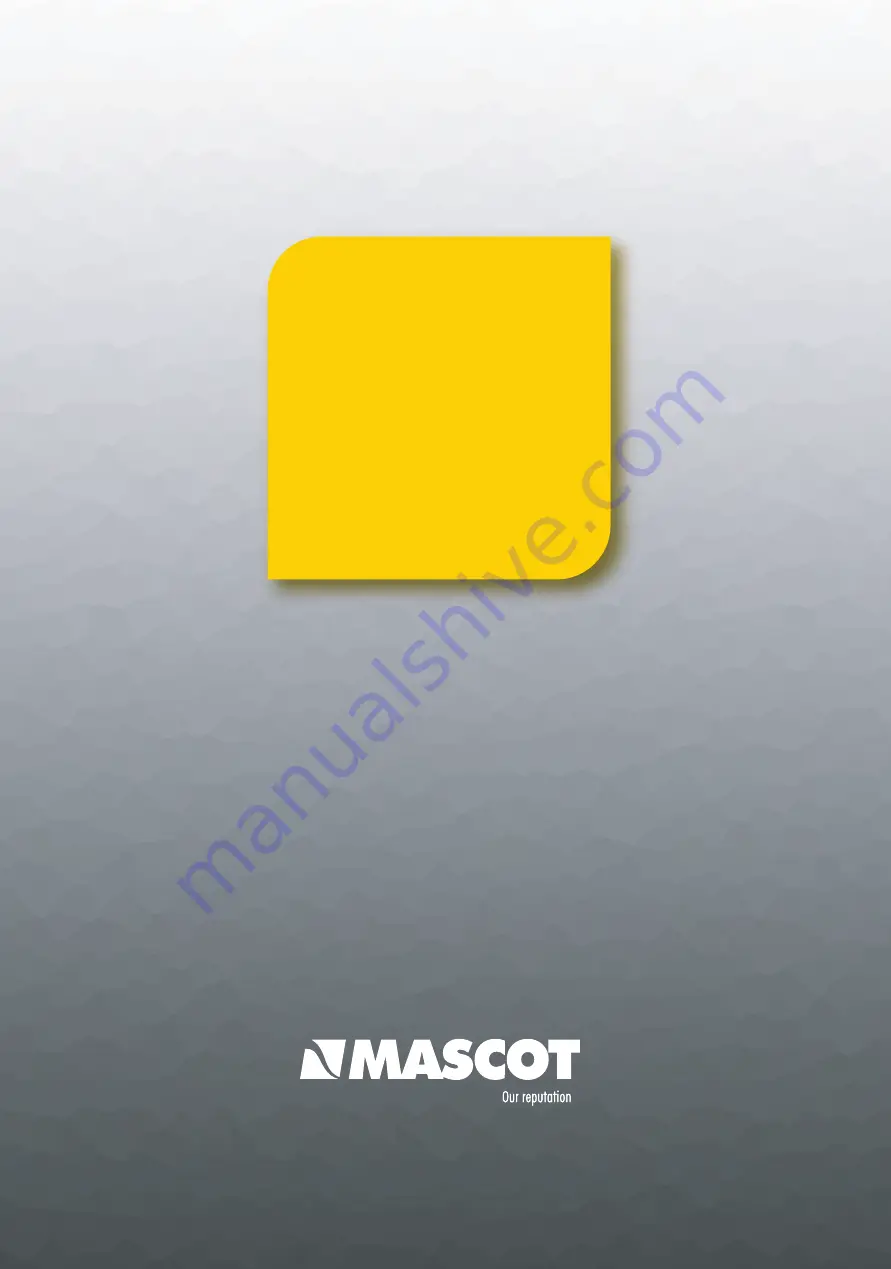
CAUTION :
1.
Use pressure relief valves for high pressure
piping.
2.
Use explosion proof valves/accessories for
dangerous media piping.
3.
Use fire safe valves for piping where chances of
fire by external means.
4.
Use seismic proof valves where chances of
earthquake are frequent.
5.
Check whether location of the valve mounting is
of the same service/application as specified on
the marking plate.
Installation, Operation,
Maintenance Instructions
DiskFlo
Control Valves