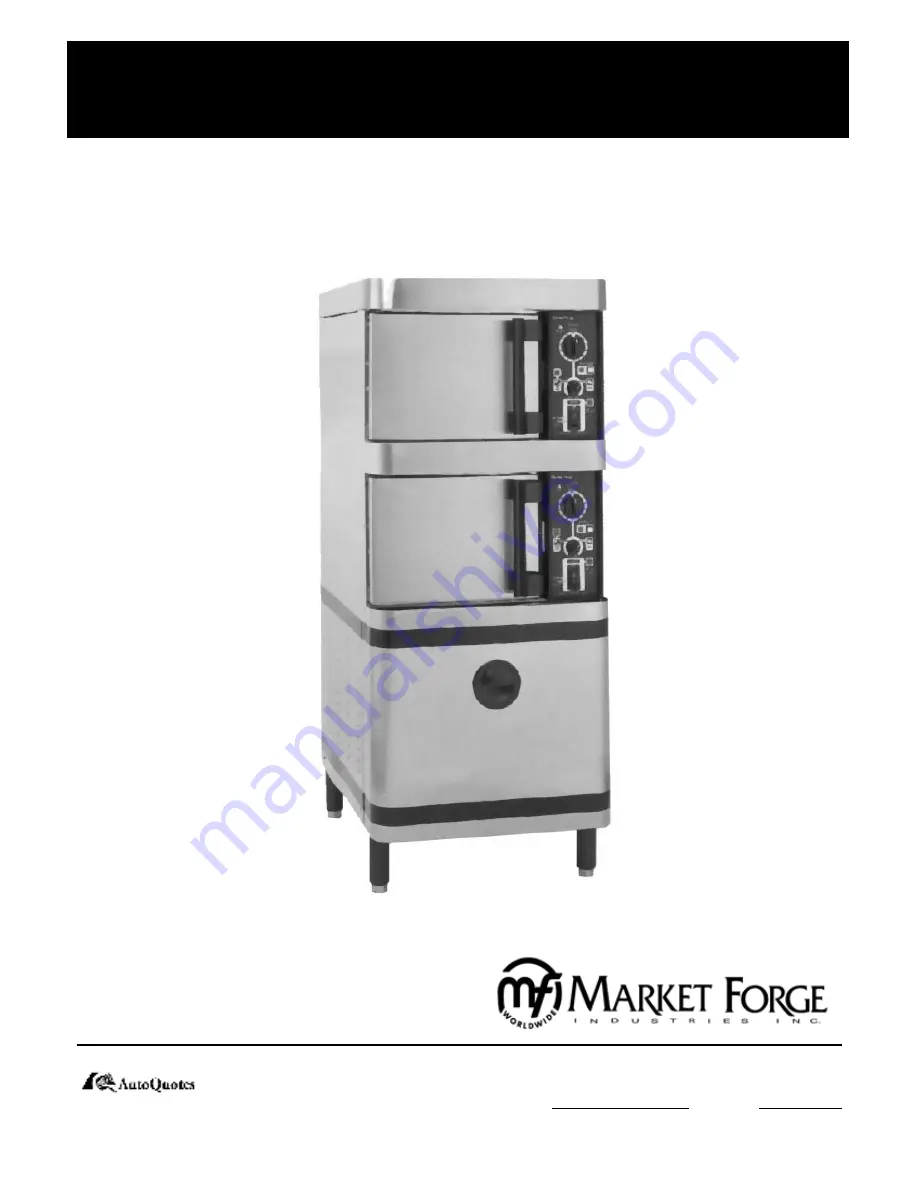
STEAM-TECH
PLUS
ELECTRIC STEAM COOKER
STP-6E
OWNER’S MANUAL
Printed in U.S.A.
35 Garvey Street
l
Everett
l
MA
l
02149
Tel: (617) 387-4100
l
Toll Free: (888) 698-3188
Fax: (617) 387-4456
l
Outside MA Fax: (800) 227-2659
E-Mail:
l
Website:
www.mfii.com
Form Number: S-2464 01/07
An Employee Owned Company
Summary of Contents for STEAM-TECH PLUS STP-6E
Page 20: ...6 5 6 MAINTENANCE FIGURE 6 3 ...
Page 21: ...6 6 6 MAINTENANCE FIGURE 6 4 PRINCIPLES OF OPERATION SCHEMATIC ...
Page 22: ...6 7 6 MAINTENANCE FIGURE 6 5 SINGLE COMPARTMENT SYSTEM WIRING DIAGRAM ...
Page 23: ...6 8 6 MAINTENANCE FIGURE 6 6 SINGLE COMPARTMENT SYSTEM WIRING DIAGRAM ...
Page 27: ...6 12 6 MAINTENANCE FIGURE 6 9 COOKING COMPARTMENT DOOR ASSEMBLY ...
Page 31: ...6 16 6 MAINTENANCE FIGURE 6 12 TEMPERING TANK ASSEMBLY ...
Page 32: ...6 17 6 MAINTENANCE FIGURE 6 13 CHASSIS ASSEMBLY ...
Page 34: ...6 19 6 MAINTENANCE FIGURE 6 14 TUBING ROUTING ...