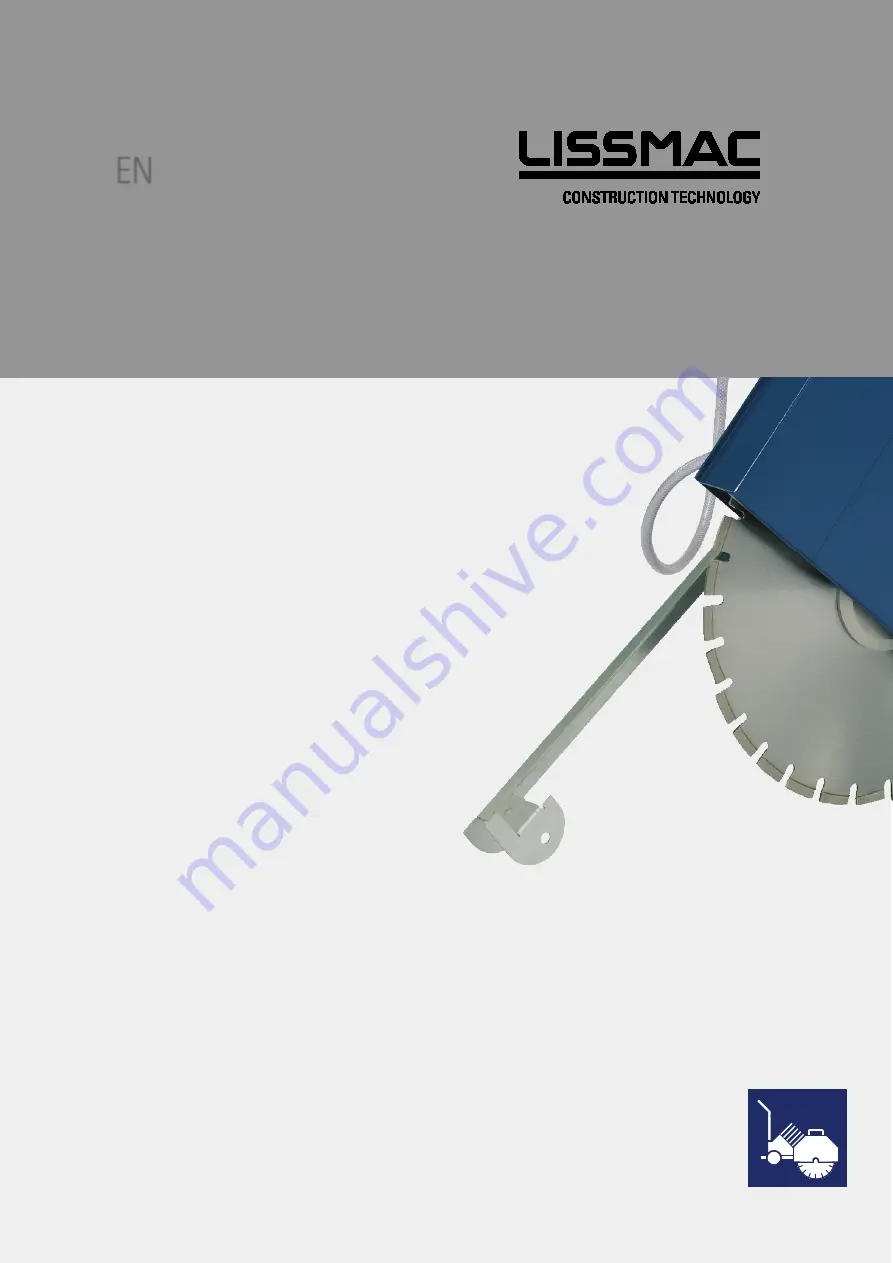
1/80
OPERATING MANUAL
FLOOR SAW
COMPACTCUT 905 P/T
LISSMAC Maschinenbau GmbH
Lanzstrasse 4
D-88410 Bad Wurzach
Tel49 (0) 7564 / 307-0
T49 (0) 7564 / 307-500
[email protected]
www.lissmac.com
EN
Summary of Contents for COMPACTCUT 905 P/T
Page 2: ...2 80 ...
Page 8: ...8 80 Notes ...
Page 78: ...78 80 11 CIRCUIT DIAGRAM Oil filter Air filter Emergency Stop ...
Page 80: ...80 80 ...