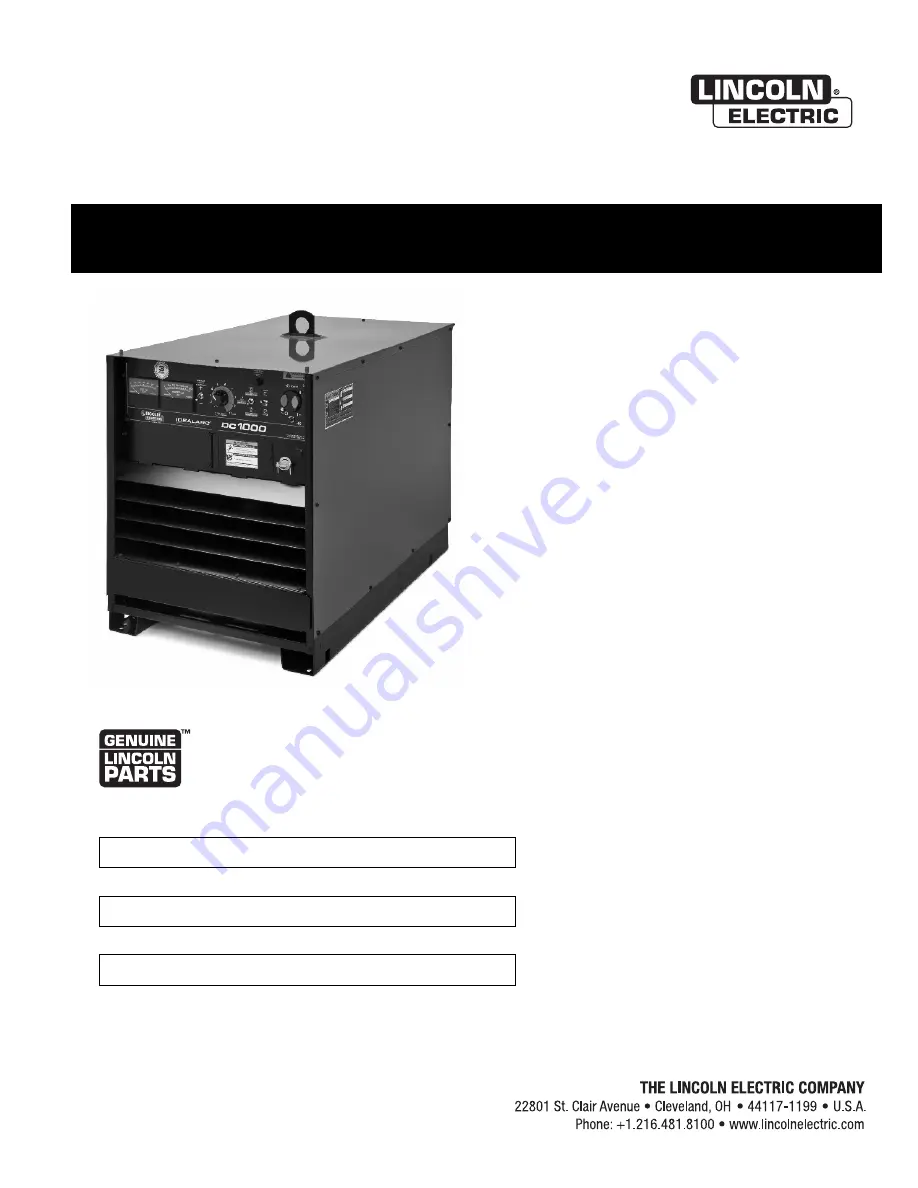
Operator’s Manual
IDEALARC
®
DC-1000
Register your machine:
www.lincolnelectric.com/register
Authorized Service and Distributor Locator:
www.lincolnelectric.com/locator
IM10212
| Issue D ate Sept-15
© Lincoln Global, Inc. All Rights Reserved.
For use with machines having Code Numbers:
12480
Need Help? Call 1.888.935.3877
to talk to a Service Representative
Hours of Operation:
8:00 AM to 6:00 PM (ET) Mon. thru Fri.
After hours?
Use “Ask the Experts” at lincolnelectric.com
A Lincoln Service Representative will contact you
no later than the following business day.
For Service outside the USA:
Email: [email protected]
Save for future reference
Date Purchased
Code: (ex: 10859)
Serial: (ex: U1060512345)