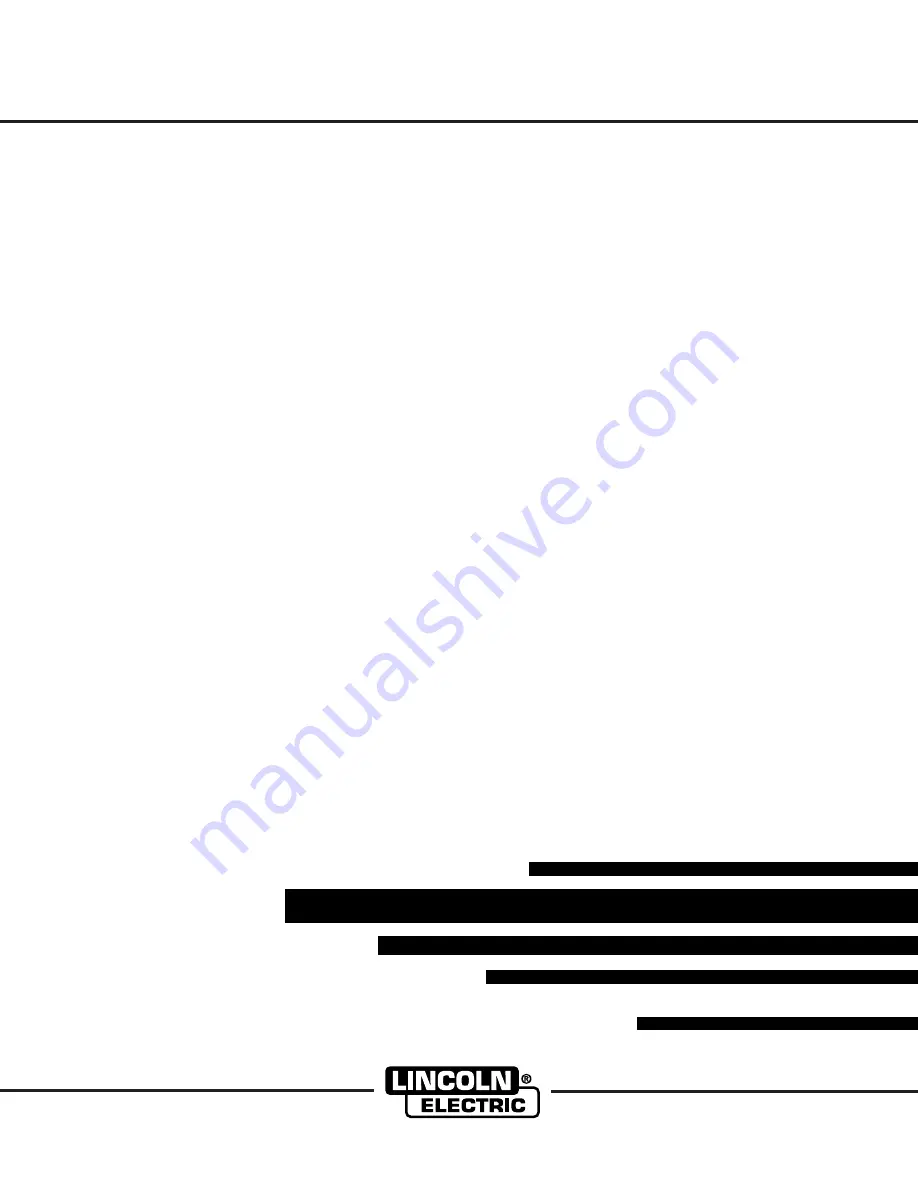
SAM400 & 650 PERKINS DIESEL ENGINE DRIVEN
MULTI-PROCESS DC ARC WELDING POWER SOURCES
OPERATOR’S MANUAL
Sales and Service through Subsidiaries and Distributors Worldwide
22801 St. Clair Ave. Cleveland, Ohio 44117-1199 U.S.A. Tel. (216) 481-8100
World's Leader in Welding and Cutting Products
Premier Manufacturer of Industrial Motors
IM568
April, 1997
For use with SAM400 machines having Code Numbers: 10140 & 10141
For use with SAM650 machines having Code Number: 10333
Supersedes IM247-D
Safety Depends on You
Lincoln arc welding and cutting
equipment is designed and built with
safety in mind. However, your overall
safety can be increased by proper
installation ... and thoughtful opera-
tion on your part.
DO NOT
INSTALL, OPERATE OR REPAIR
THIS EQUIPMENT WITHOUT
READING THIS MANUAL AND
THE SAFETY PRECAUTIONS
CONTAINED THROUGHOUT.
And, most importantly, think before
you act and be careful.