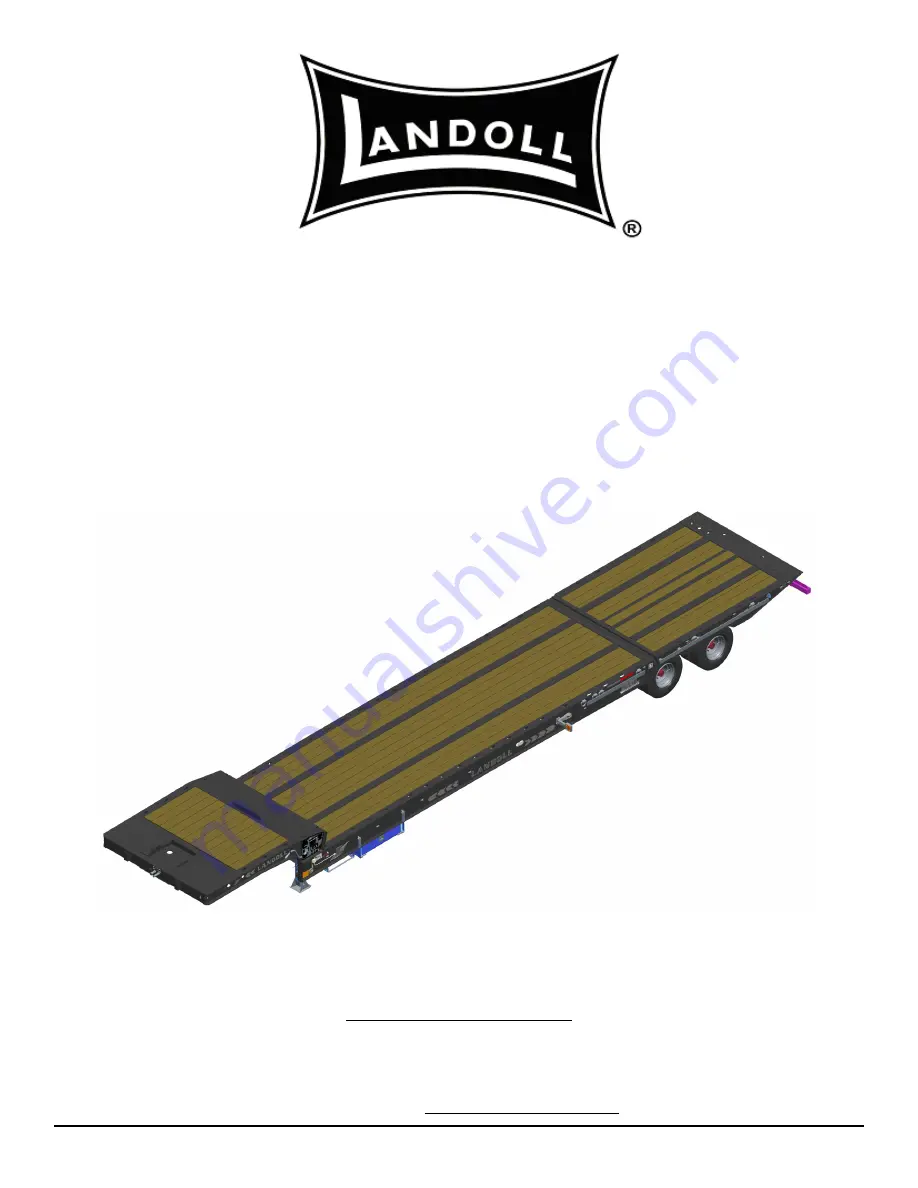
F-823-0216
02/2016
LANDOLL CORPORATION
1900 North Street
Marysville, Kansas 66508
(785) 562-5381
800-428-5655 ~ WWW.LANDOLL.COM
Model 900D Series
Hydraulic Tail Semitrailer
Operator’s Manual
Ea
st
ern
W
re
cke
r Sa
le
s
In
c
F-823-0216
02/2016
LANDOLL CORPORATION
1900 North Street
Marysville, Kansas 66508
(785) 562-5381
800-428-5655 ~ WWW.LANDOLL.COM
Model 900D Series
Hydraulic Tail Semitrailer
Operator’s Manual
Ea
st
ern
W
re
cke
r Sa
le
s
In
c