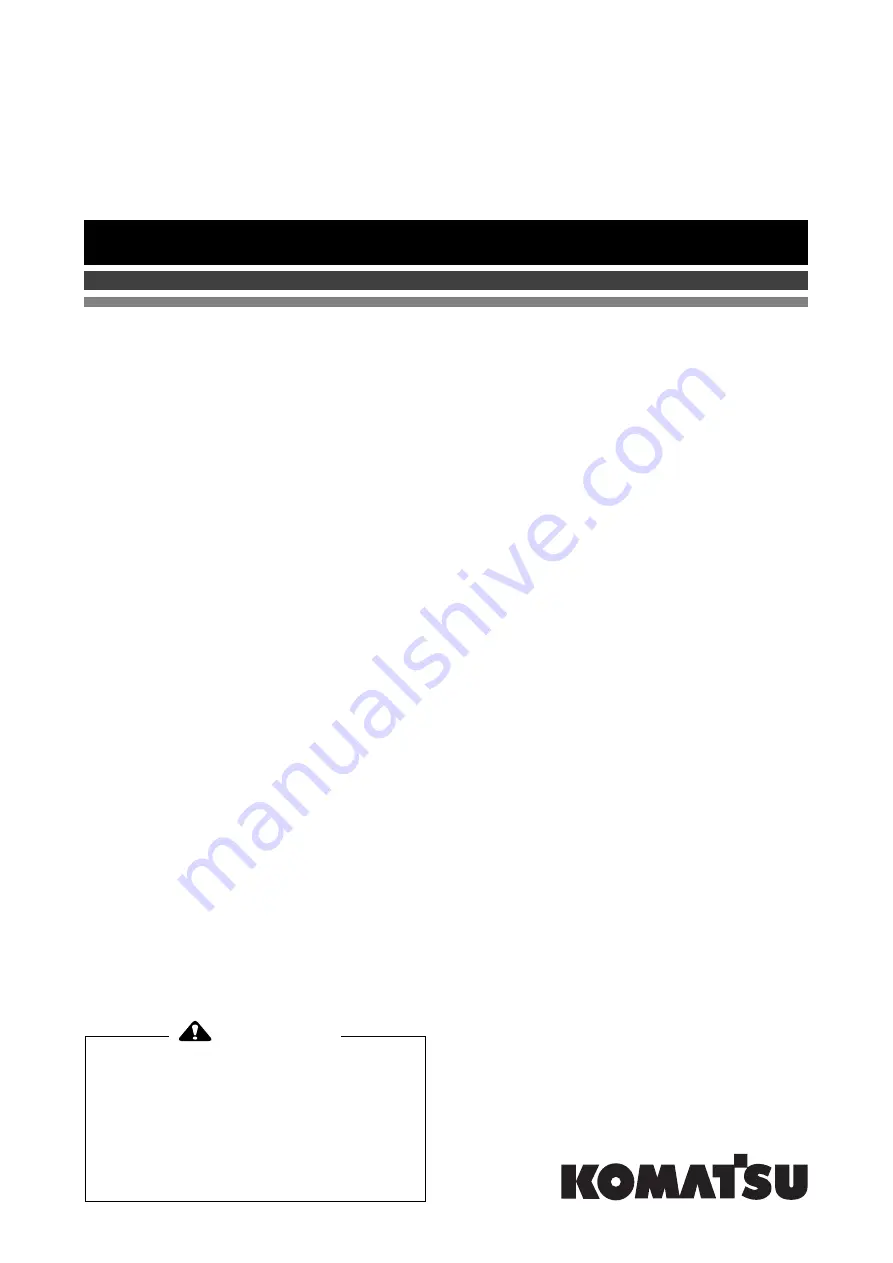
D155AX
-5
SERIAL NUMBER
D155AX - 76243
and up
BULLDOZER
Unsafe use of this machine may cause serious injury or
death. Operators and maintenance personnel must read
this manual before operating or maintaining this
machine. This manual should be kept inside the cab for
reference and periodically reviewed by all personnel who
will come into contact with the machine.
Operation &
Maintenance Manual
EEAM023402
WARNING
Summary of Contents for 76243
Page 2: ......
Page 3: ...FOREWORD 11 ...
Page 5: ...FOREWORD FOREWORD 1 3 q Machine equipped without cab Back pocket of operator s seat ...
Page 16: ...NECESSARY INFORMATION FOREWORD 1 14 ...
Page 17: ...FOREWORD NECESSARY INFORMATION 1 15 ...
Page 24: ...CONTENTS 1 22 ...
Page 28: ...SAFETY LABELS SAFETY 2 4 SAFETY LABELS 2 POSITIONS OF SAFETY PICTOGRAMS 2 ...
Page 289: ...SPECIFICATIONS 15 ...
Page 297: ...INDEX 17 ...
Page 298: ...INDEX 7 2 ...
Page 301: ...COLOPHON 18 ...