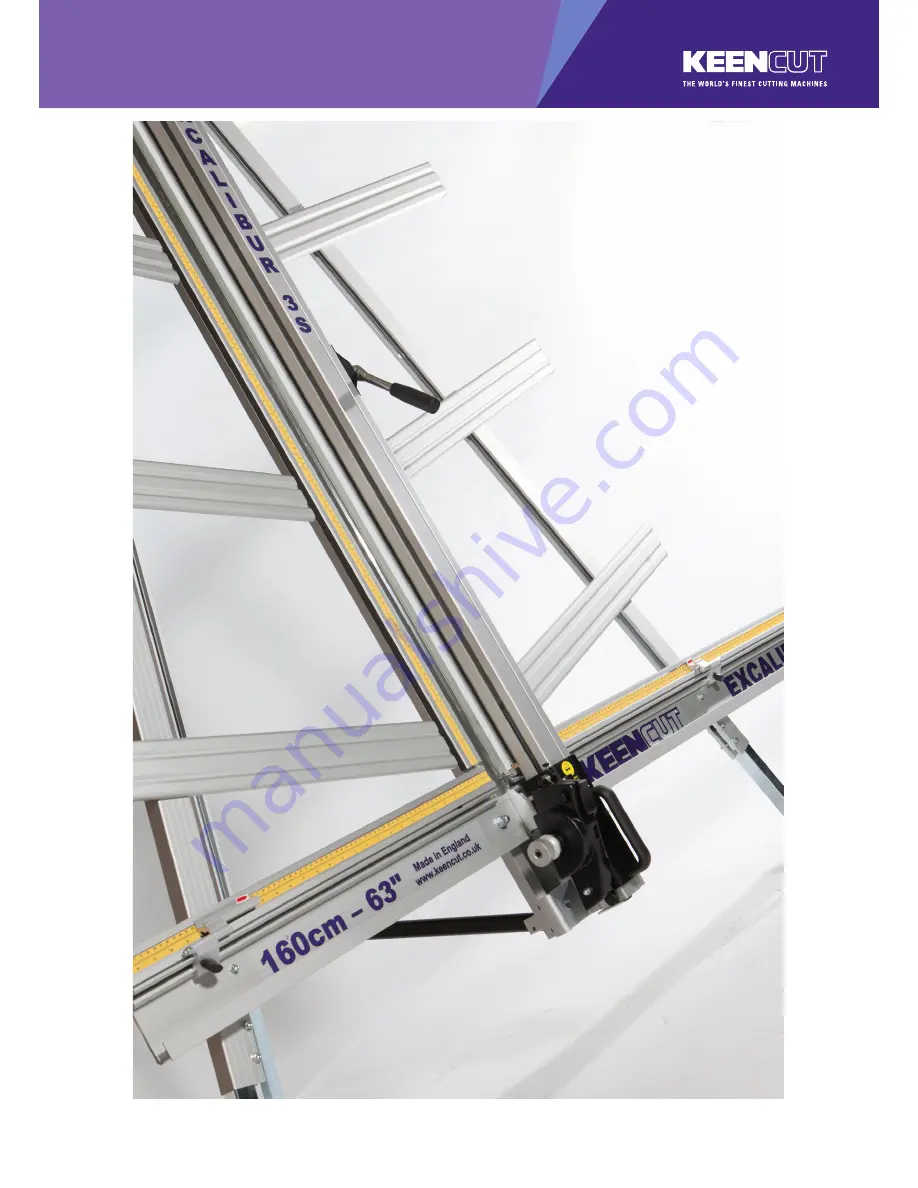
EXCALIBUR 3S
Manual
Single language versions and parts diagrams can be down loaded from www.keencut.co.uk
Thank you for choosing the Keencut Excalibur 3S. Every
effort has been made to bring you a precision engineered
product with the promise of many years of valuable
service. In order to obtain maximum benefit from your
machine please read these instructions carefully. For advice
and assistance or replacement parts please contact your
distributor or Keencut.
PLEASE NOTE THIS IS A TEMPORARY MANUAL