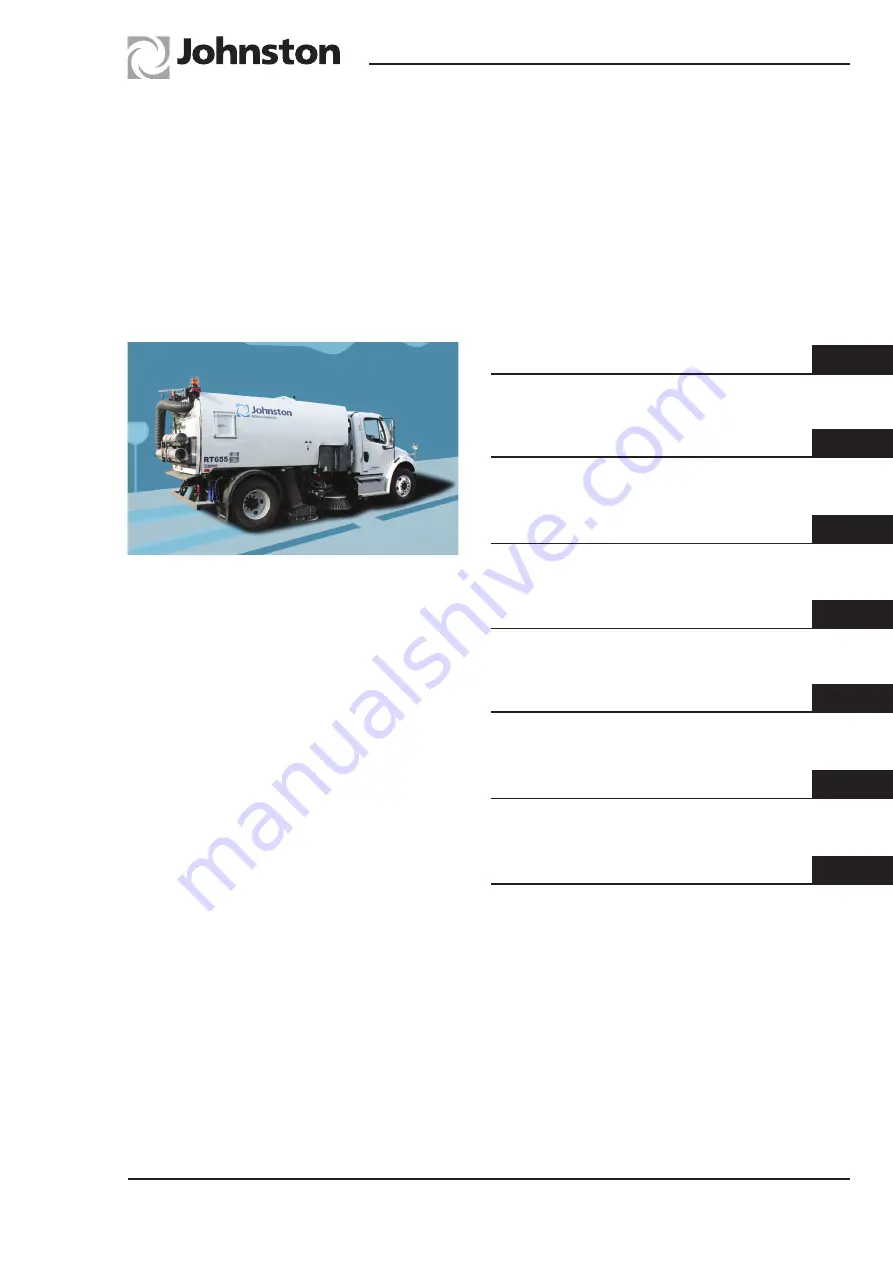
Johnston Sweepers Limited
General Arrangement
Controls
Operation
Optional Equipment
Chapter not used
Routine Maintenance
RT655 Mk III
Regenerative Air
Twin Engine
Suction Sweeper
From Manufacture Sequence No. 7458
Part No 01288-1(GB)
Revision Level A
E.C.N. 712675
Print date - 16/11/2015
1
2
3
4
5
6
Operator’s
Guide
Conformity Certificates
7