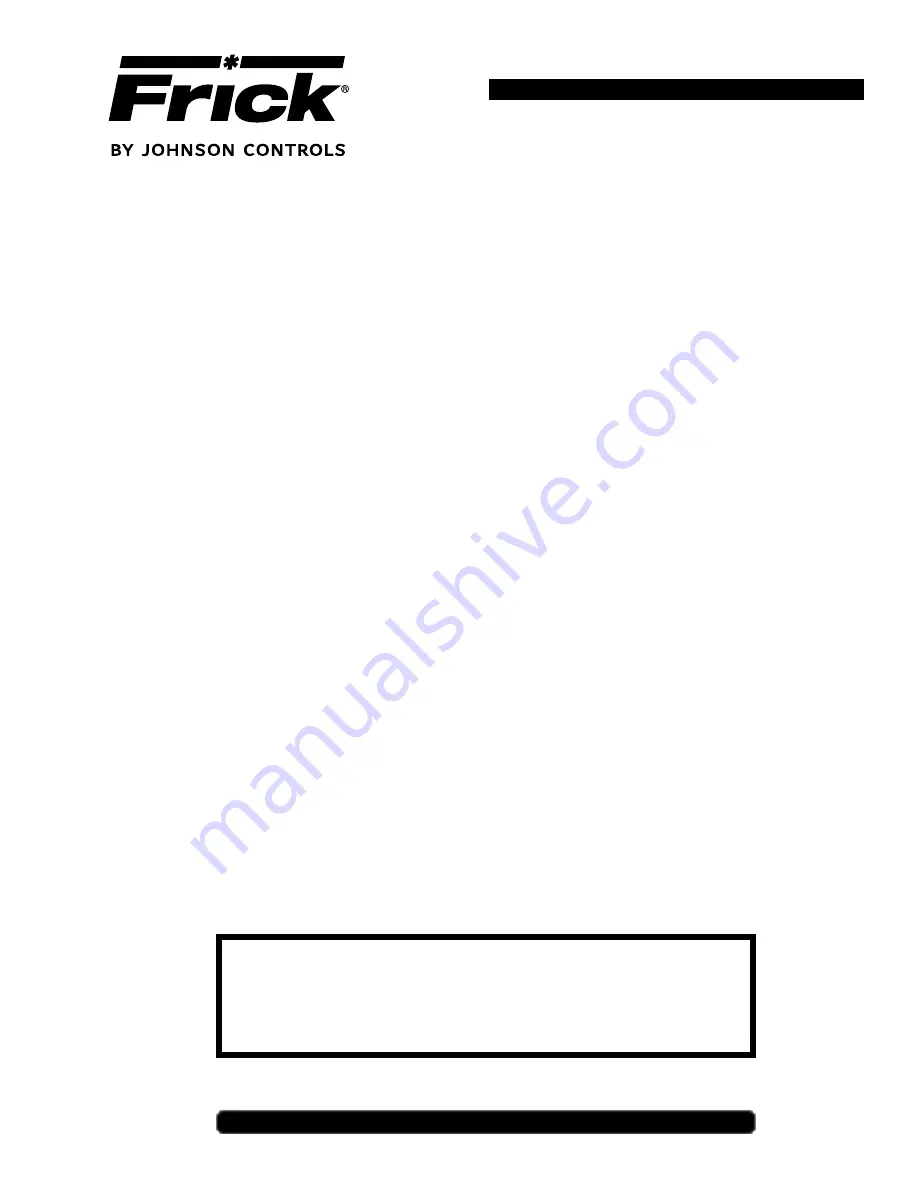
ROTARY SCREW COMPRESSOR UNITS
ALL REFRIGERANTS
MODELS
100 through 480
RWF
THIS MANUAL CONTAINS RIGGING, ASSEMBLY, START-UP, AND
MAINTENANCE INSTRUCTIONS. READ THOROUGHLY BEFORE
BEGINNING INSTALLATION. FAILURE TO FOLLOW THESE
INSTRUCTIONS COULD RESULT IN DAMAGE OR IMPROPER
OPERATION OF THE UNIT.
Form S70-600 IOM (OCT 2004)
INSTALLATION - OPERATION - MAINTENANCE
File:
EQUIPMENT MANUAL - Section 70
Replaces:
S70-600 IOM/MAY 2001
Dist:
3, 3a, 3b, 3c
Please check www.frickcold.com for the latest version of this publication.