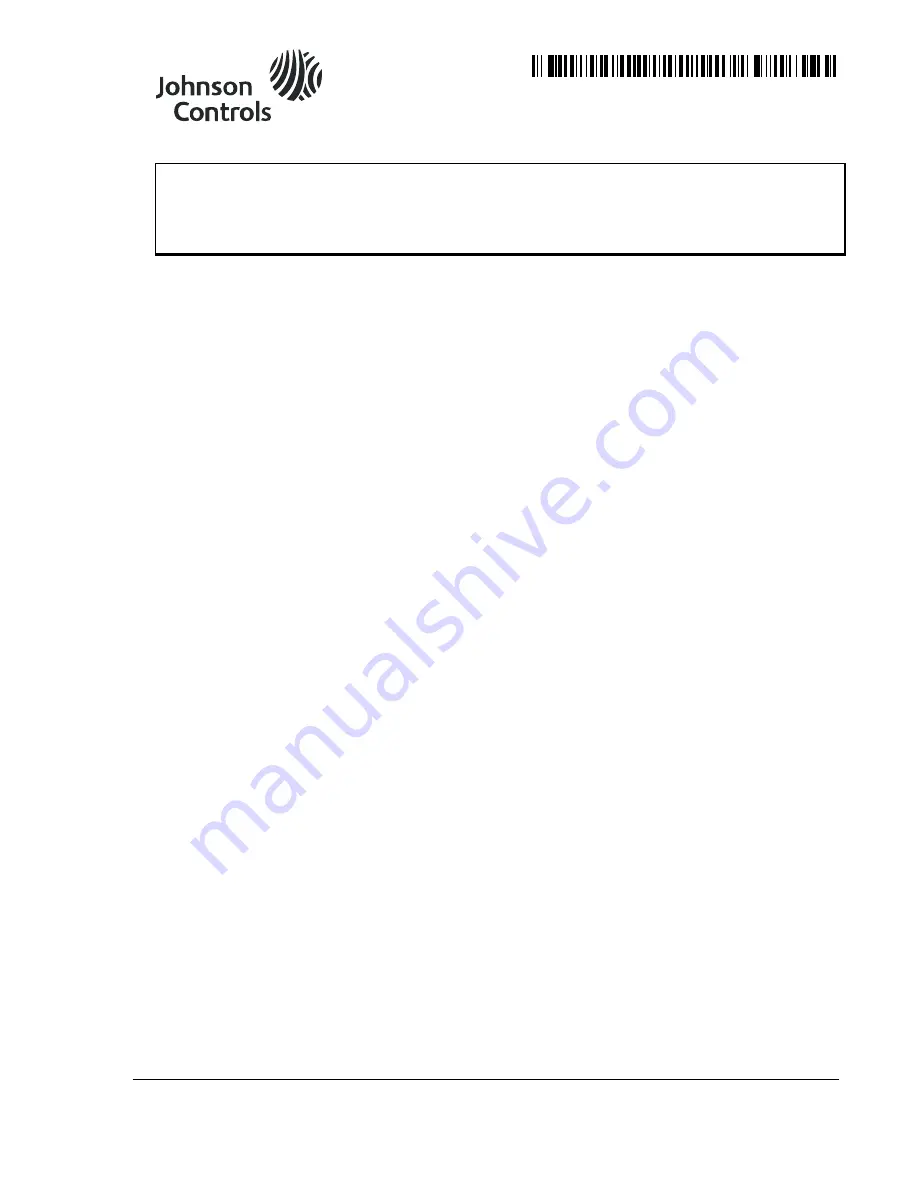
64- 378- 14, Rev. D
Technical Bulletin A-4400
Issue Date 0316
©
2016 Johnson Controls, Inc.
1
Part No. 64-378-14, Rev. D
Code No. LIT-718050T
Conventional Wall Mounting Arrangement
Activated Carbon Filter Installation
Permanent Wiring Using Conduit
Evaporator Pressure Adjustment
Low Ambient Temperature Compensation
A-4400 Series Refrigerated Air Dryers
Installation and Maintenance