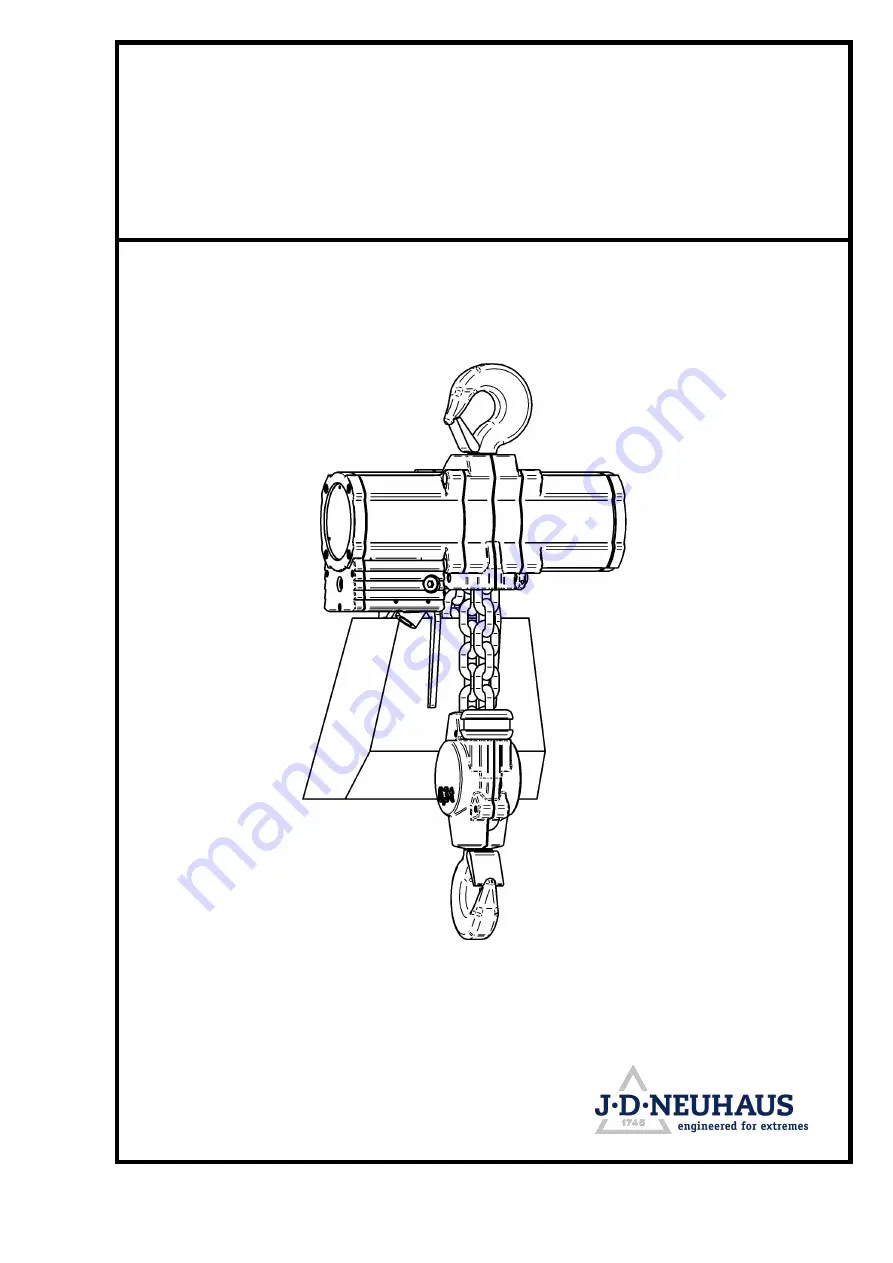
JDN OPERATING AND ASSEMBLY INSTRUCTIONS
Hoist
PROFI 6 TI
Serial No.: P706448
Doc.-No.: VA057988-10-OM-EN-0821-62-1
ORIGINAL OPERATING
AND ASSEMBLY INSTRUCTIONS
Representation may differ from actual product!
JDN OPERATING AND ASSEMBLY INSTRUCTIONS
Hoist
PROFI 6 TI
Serial No.: P706448
Doc.-No.: VA057988-10-OM-EN-0821-62-1
ORIGINAL OPERATING
AND ASSEMBLY INSTRUCTIONS
Representation may differ from actual product!