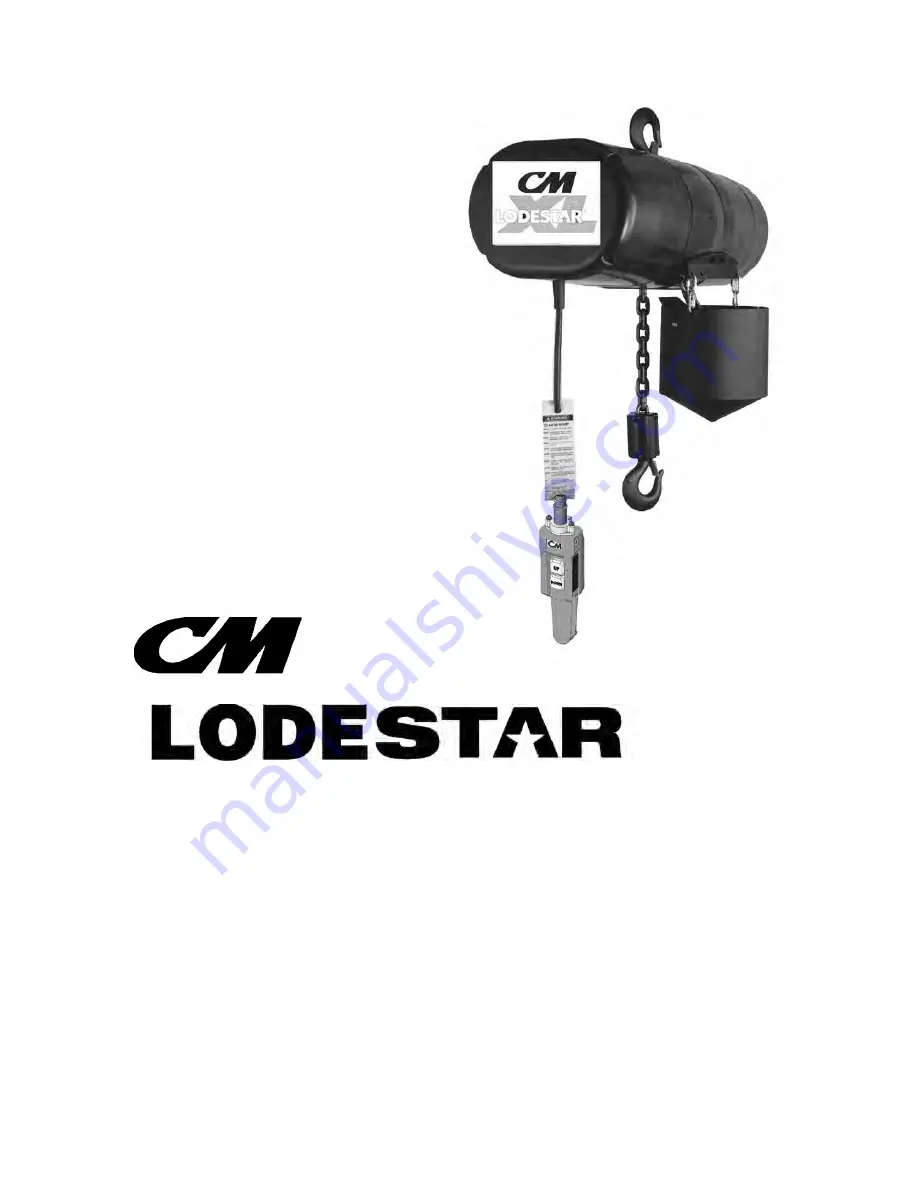
O P E R AT I N G ,
M A I N T E N A N C E
& PA R T S
M A N U A L
E L E C T R I C
C H A I N H O I S T
Manual No. 652-E
Before installing hoist, fill in
the information below. Refer
to the hoist identification
plate.
Model No. __________________
Serial No. __________________
Purchase Date ______________
Voltage ____________________
Rated Capacity______________
52756
XXLL
Rated capacities 2 through 7½ tons/
2000 through 7500 kg
Follow all instructions and warnings for
inspecting, maintaining and operating this hoist.
The use of any hoist presents some risk of personal
injury or property damage. That risk is greatly
increased if proper instructions and warnings are not
followed. Before using this hoist, each operator
should become thoroughly familiar with all warnings,
instructions and recommendations in this manual.
Retain this manual for future reference and use.
Forward this manual to operator.
Failure to operate equipment as directed
in manual may cause injury.
®