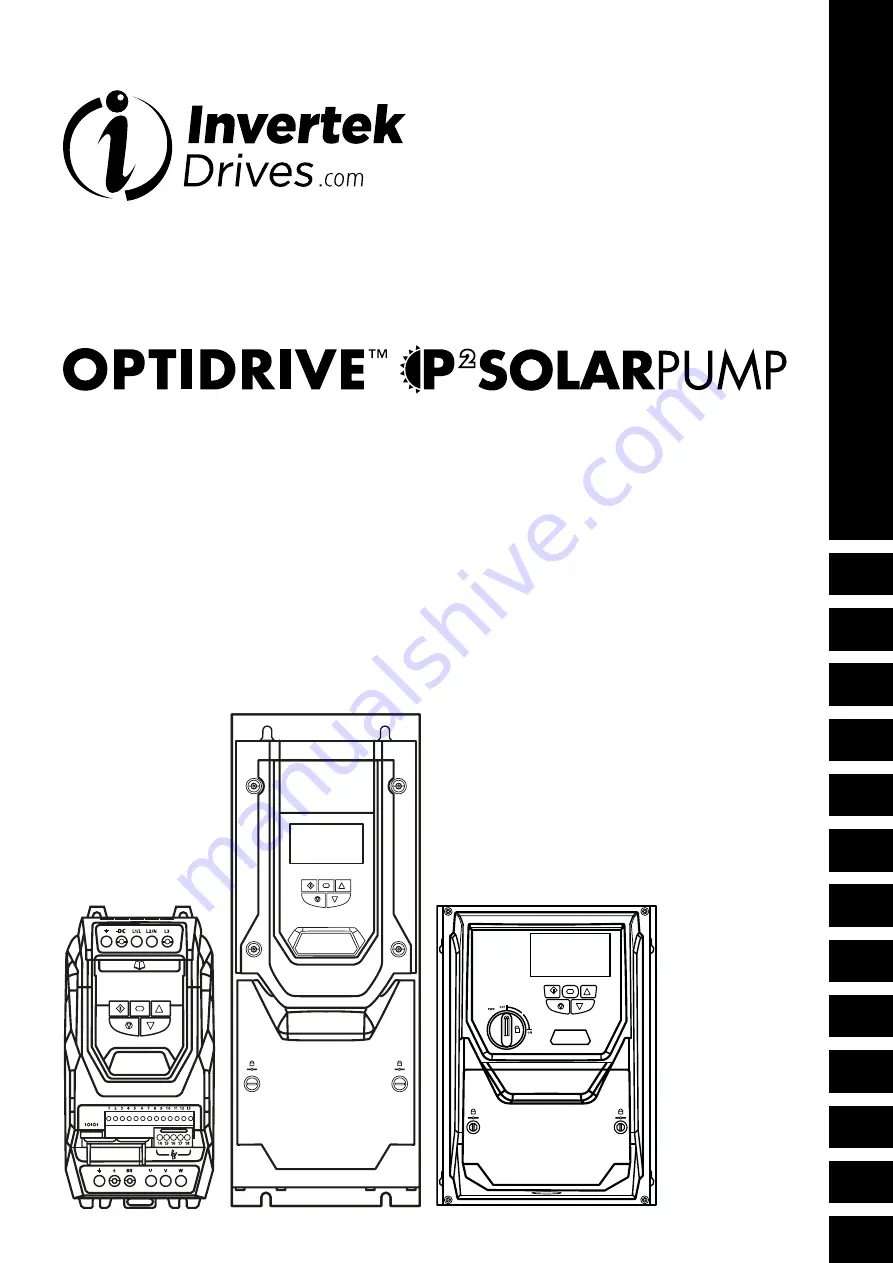
User Guide
AC Variable Speed Drive
for Solar Pumping Applications
0.75kW – 160kW / 1HP – 250HP
For 200 and 400 Volt 3 Phase Motors
2
General Information
and Ratings
1
Before You Start
3
Mechanical Installation
4
Electrical Installation
5
LED Keypad and
Display Operation
6
Quick Start Procedure
7
Full Parameter List
7
Control Terminal
Functions
8
Extended
Parameters
9
Serial
Communications
10
Technical Data
11
Troubleshooting