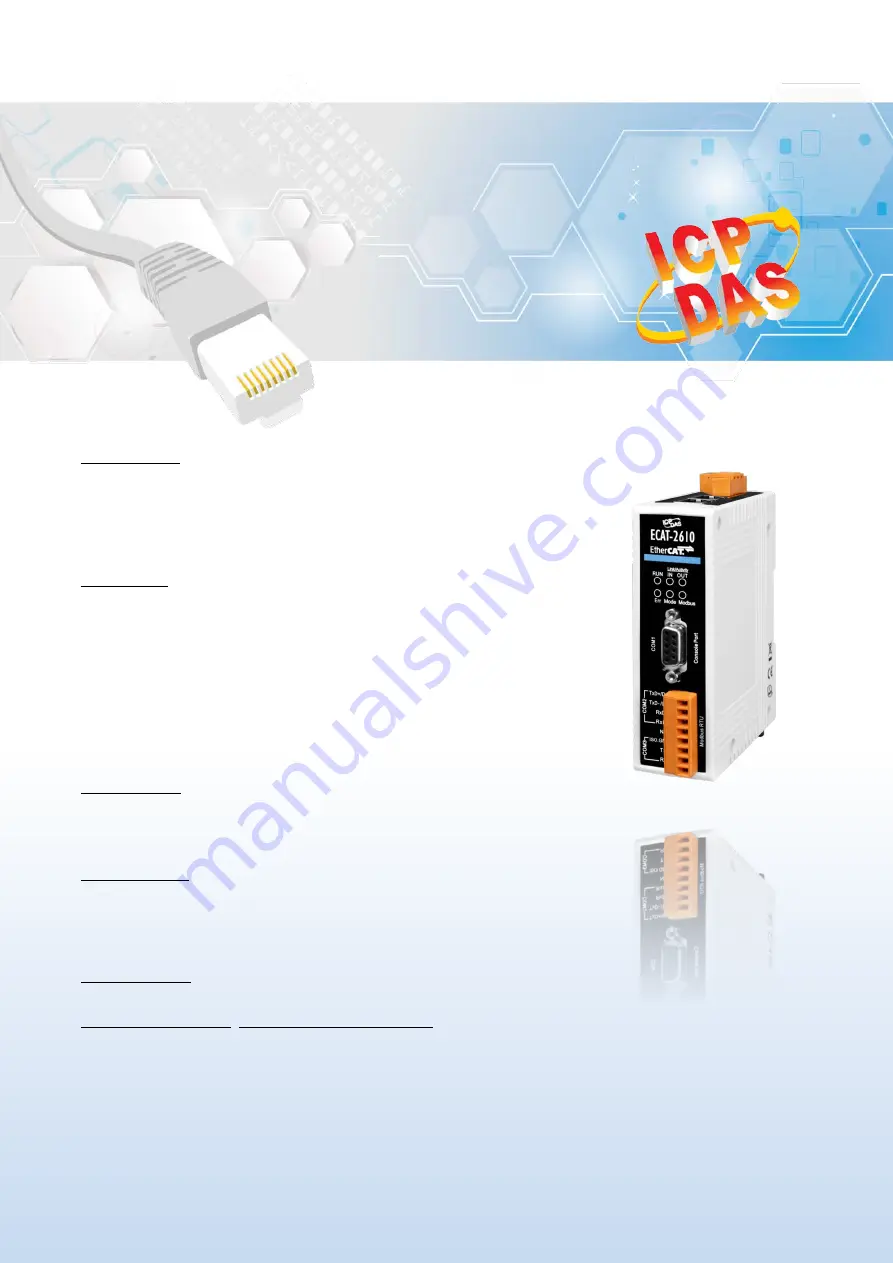
ECAT-2610 EtherCAT to Modbus
RTU Gateway
User Manual
English Ver. 1.0, Dec. 2017
WARRANTY
All products manufactured by ICP DAS are warranted against
defective materials for a period of one year from the date of
delivery to the original purchaser.
WARNING
ICP DAS assumes no liability for damages consequent to the use
of this product. ICP DAS reserves the right to change this manual
at any time without notice. The information furnished by ICP
DAS is believed to be accurate and reliable. However, no
responsibility is assumed by ICP DAS for its use, nor for any
infringements of patents or other rights of third parties resulting
from its use.
COPYRIGHT
Copyright © 2017 by ICP DAS. All rights are reserved.
TRADEMARK
Names are used for identification only and may be registered
trademarks of their respective companies.
CONTACT
US
If you have any questions, please feel free to contact us via email at:
[email protected], [email protected]