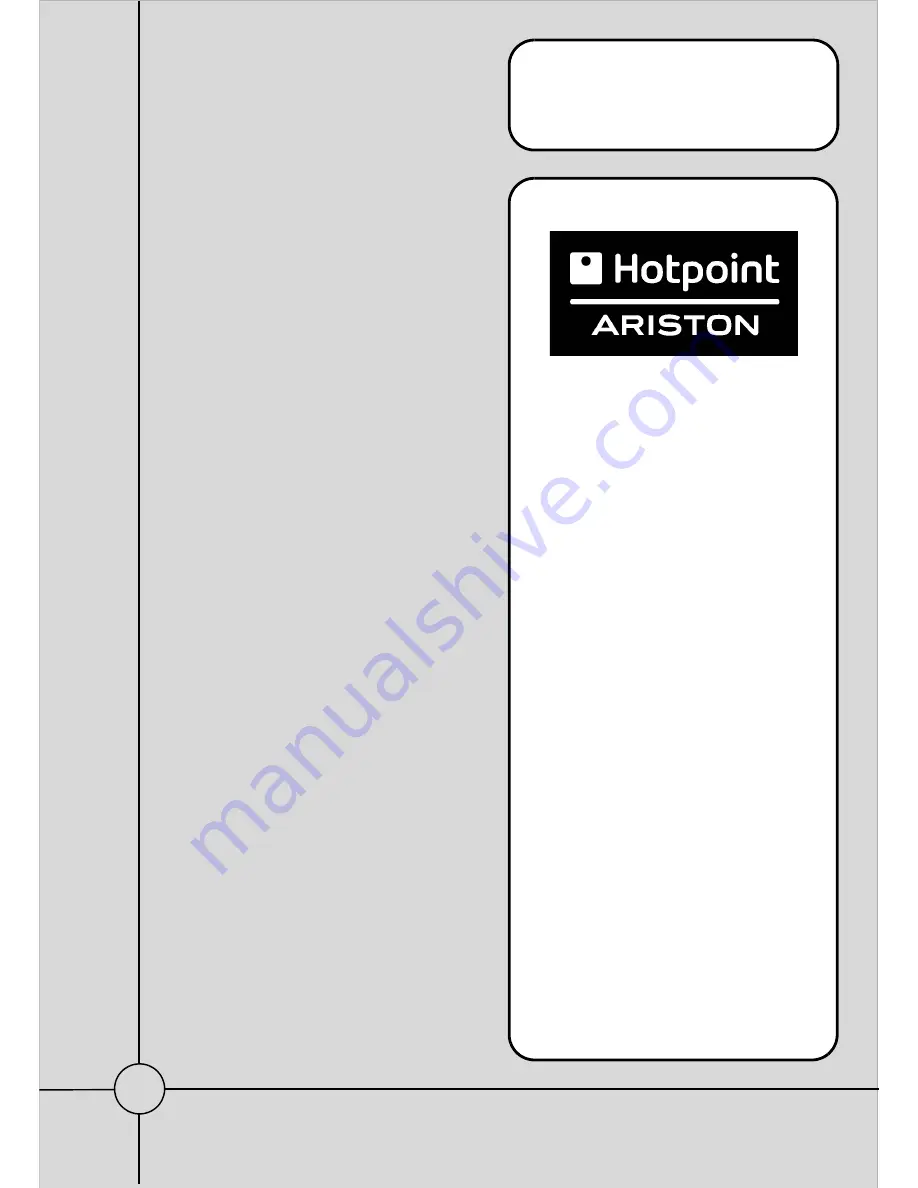
Indesit Company UK Ltd
© 2008 Reg. Office: Peterborough PE2 9JB Registered in London: 106725
Service
Information
Aqualtis
8 Kg
"B Energy"
CONDENSER
ELECTRONIC
TUMBLE DRYER
Models Covered
AQCF851BUEU
61513
AQCF851BUFR
61408
AQCF851BUIT
61375
AQCF852BIEU
61523
AQCF852BUEU
61526
AQCF852BUSK
61527
5407471 Issue 1 Nov. 2008