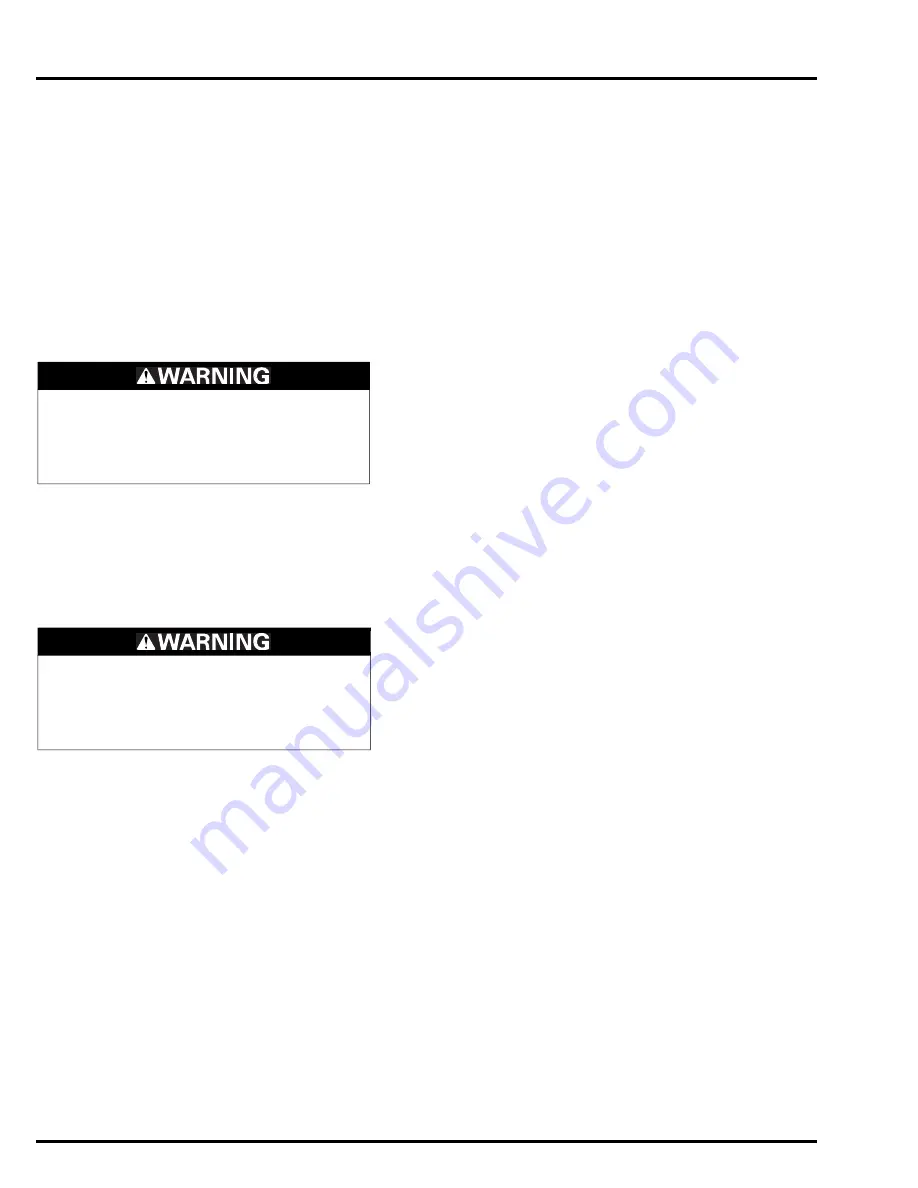
0
dummyhead
dummyhead
How to use this manual
How to use this manual
A Few Words About Safety
Service Information
The service and repair information contained in this manual is intended for use by qualified, professional technicians. Attempting
service or repairs without the proper training, tools, and equipment could cause injury to you and/or others. It could also damage
this Honda product or create an unsafe condition.
This manual describes the proper methods and procedures for performing service, maintenance, and repairs. Some procedures
require the use special tools. Any person who intends to use a replacement part, service procedure, or a tool that is not
recommended by Honda must determine the risks to their personal safety and the safe operation of this product.
If you need to replace a part, use Honda Genuine parts with the correct part number or an equivalent part. We strongly recommend
that you do not use replacement parts of inferior quality.
For Your Customer’s Safety
Proper service and maintenance are essential to the customer’s safety and the reliability of this product. Any error or oversight
while servicing this product can result in faulty operation, damage to the product, or injury to others.
For Your Safety
Because this manual is intended for the professional service technician, we do not provide warnings about many basic shop safety
practices (e.g., Hot parts-wear gloves). If you have not received shop safety training or do not feel confident about your knowledge
of safe servicing practices, we recommend that you do not attempt to perform the procedures described in this manual.
Some of the most important general service safety precautions are given below. However, we cannot warn you of every
conceivable hazard that can arise in performing service and repair procedures. Only you can decide whether or not you should
perform a given task.
Important Safety Precautions
Make sure you have a clear understanding of all basic shop safety practices and that you are wearing appropriate clothing and
using safety equipment. When performing any service task, be especially careful of the following:
• Read all of the instructions before you begin, and make sure you have the tools, the replacement or repair parts, and the skills
required to perform the tasks safely and completely.
• Protect your eyes by using proper safety glasses, goggles, or face shields anytime you hammer, drill, grind, or work around
pressurized air, pressurized liquids, springs or other stored-energy components. If there is any doubt, put on eye protection.
• Use other protective wear when necessary, for example gloves or safety shoes. Handling hot or sharp parts can cause severe
burns or cuts. Before you grab something that looks like it can hurt you, stop and put on gloves.
• Protect yourself and others whenever you have equipment hoisted in the air. Anytime you lift this product with a hoist, make sure
that the hoist hook is securely attached to the product.
Make sure the engine is off before you begin any servicing procedures, unless the instruction tells you to do otherwise. This will
help eliminate several potential hazards:
• Carbon monoxide poisoning from engine exhaust. Be sure there is adequate ventilation whenever you run the engine.
• Burns from hot parts. Let the engine and exhaust system cool before working in those areas.
• Injury from moving parts. If the instruction tells you to run the engine, be sure your hands, fingers, and clothing are out of the
way.
Gasoline vapors and hydrogen gasses from batteries are explosive. To reduce the possibility of a fire or explosion, be careful when
working around gasoline or batteries.
• Use only a nonflammable solvent, not gasoline, to clean parts.
• Never store gasoline in an open container.
• Keep all cigarettes, sparks, and flames away from the battery and all fuel-related parts.
Improper service or repairs can create an unsafe
condition that can cause your customer or others to
be seriously hurt or killed.
Follow the procedures and precautions in this
manual and other service materials carefully.
Failure to properly follow instructions and
precautions can cause you to be seriously hurt or
killed.
Follow the procedures and precautions in this
manual carefully.
gx120k1_gx160k1_gx200
Summary of Contents for GX120K1
Page 14: ...1 9 GX120K1 GX160K1 GX200 SPECIFICATIONS GX160K1 GX160U1 GX160UT1 gx120k1_gx160k1_gx200 ...
Page 15: ...1 10 SPECIFICATIONS GX120K1 GX160K1 GX200 GX200 GX200U GX200UT gx120k1_gx160k1_gx200 ...
Page 19: ...1 14 SPECIFICATIONS GX120K1 GX160K1 GX200 GX160K1 Unit mm in gx120k1_gx160k1_gx200 ...
Page 67: ...4 4 AIR CLEANER MUFFLER GX120K1 GX160K1 GX200 Rammer type P 3 6 P 3 6 gx120k1_gx160k1_gx200 ...
Page 69: ...4 6 AIR CLEANER MUFFLER GX120K1 GX160K1 GX200 Rammer type gx120k1_gx160k1_gx200 ...
Page 71: ...5 2 RECOIL STARTER FAN COVER GX120K1 GX160K1 GX200 GX200 gx120k1_gx160k1_gx200 ...
Page 80: ...6 1 6 CARBURETOR 1 CARBURETOR 6 2 gx120k1_gx160k1_gx200 ...
Page 81: ...6 2 CARBURETOR GX120K1 GX160K1 GX200 1 CARBURETOR REMOVAL INSTALLATION gx120k1_gx160k1_gx200 ...
Page 82: ...6 3 GX120K1 GX160K1 GX200 CARBURETOR Rammer type gx120k1_gx160k1_gx200 ...
Page 101: ...9 1 9 CYLINDER HEAD VALVES 1 CYLINDER HEAD VALVES 9 2 gx120k1_gx160k1_gx200 ...
Page 120: ...11 1 11 GOVERNOR OIL LEVEL SWITCH 1 GOVERNOR OIL LEVEL SWITCH 11 2 gx120k1_gx160k1_gx200 ...