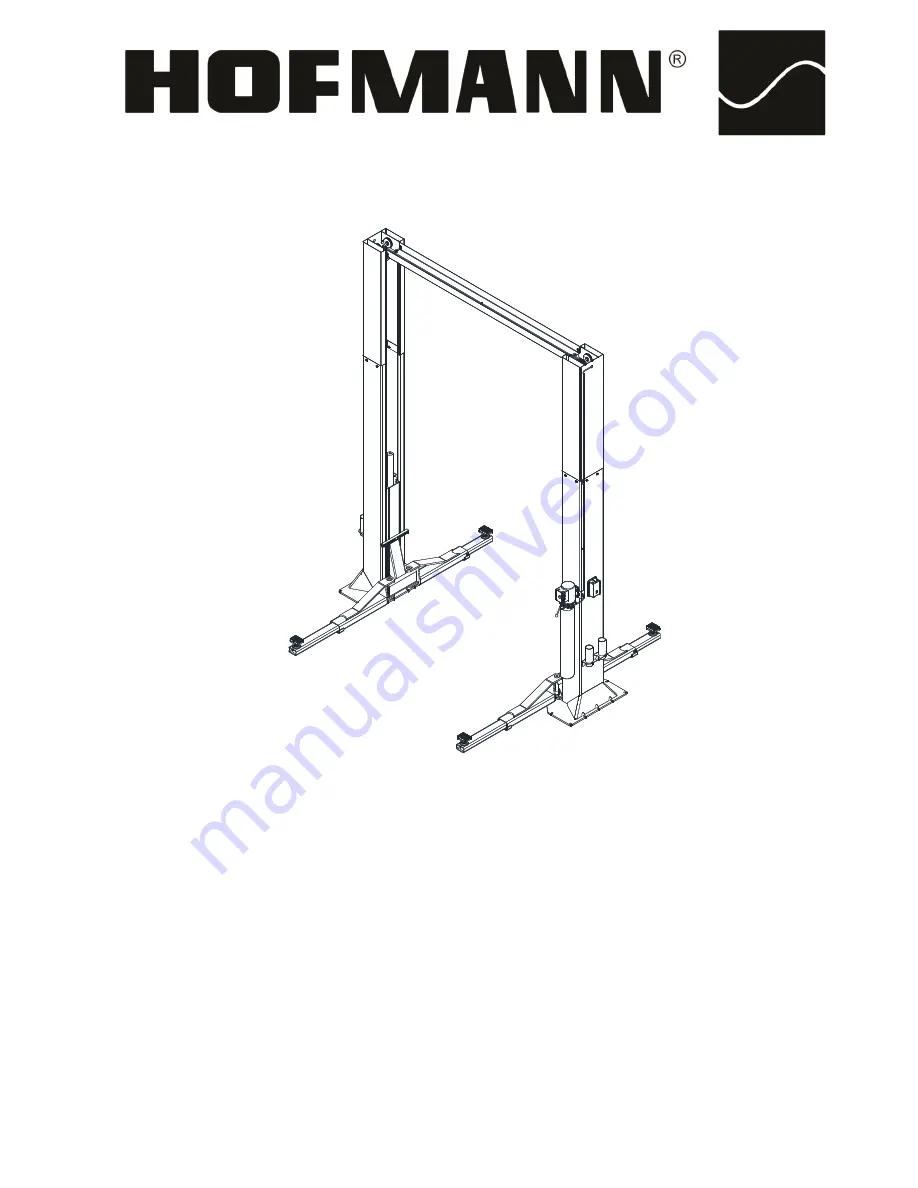
Rev. 12/03/2019
Installation, Operation & Maintenance Manual
Two Post Surface Mounted Lift
M
ODEL
EELR739A
&
EELR740A
15,000
LB
C
APACITY
-
3750
LB
P
ER
A
RM
M
ODEL
EELR741A
&
EELR742A
18,000
LB
C
APACITY
–
4500
LB PER ARM
Snap-On Equipment
309 Exchange Avenue, Conway, Arkansas, 72032
Tel: 501-450-1500
Fax: 501-450-1585
IMPORTANT:
READ THIS MANUAL COMPLETELY BEFORE
INSTALLING or OPERATING LIFT