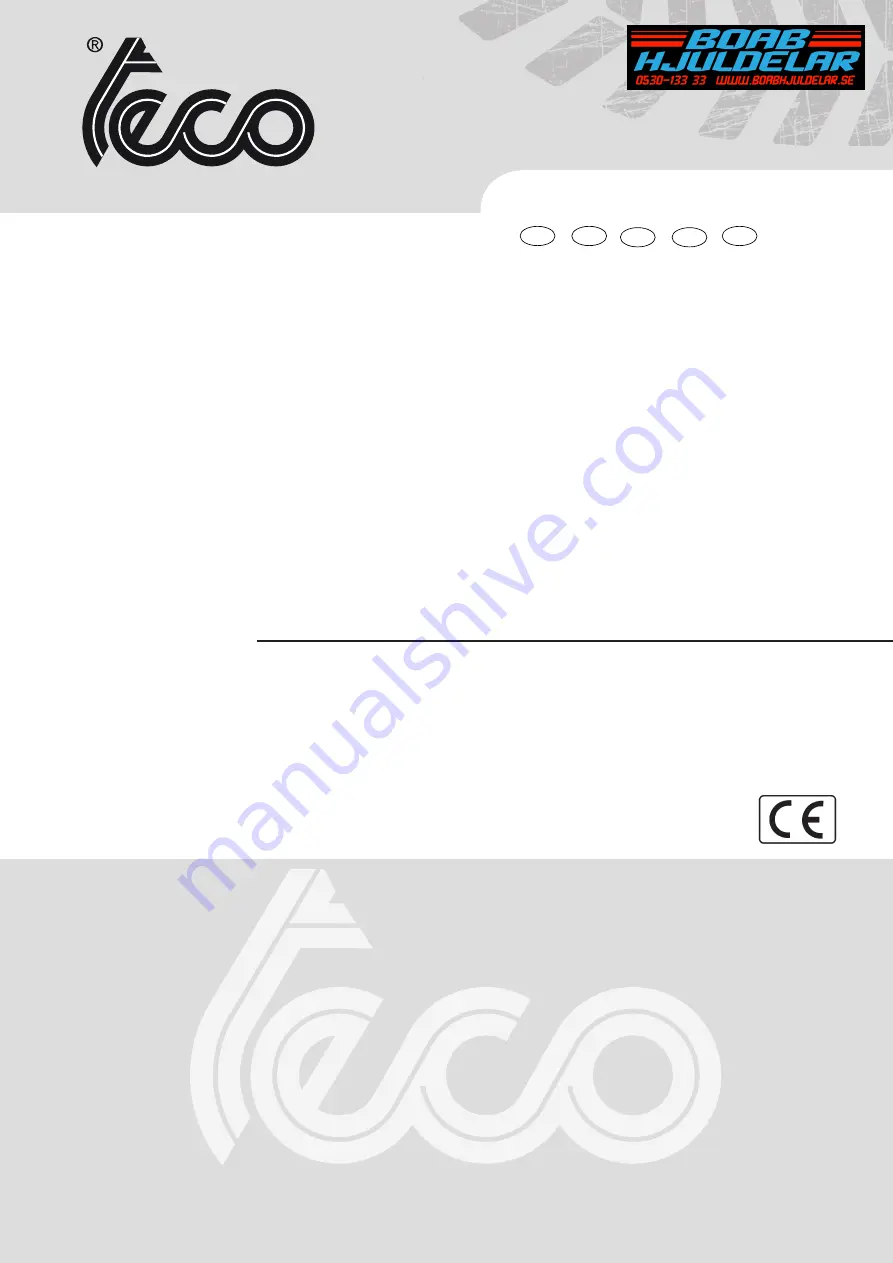
Automotive Equipment
Instruction Manual
VEHICLE
LIFT
TECO 300 SPECIAL
TECO 350 SPECIAL
4-1
24298
Version
0
.0 -
Settembre
201
8
IT
UK
FR
DE
ES
www.teco - www.tecoautomotive.com - www.youtube.com/user/TECOsrl
Telephone: +39 0522 631562 - E-mail: [email protected]
Summary of Contents for 300 SPECIAL
Page 14: ...Figura 4 LAYOUT PSS MONOFORBICE WITH ESTENSION 51 ...
Page 15: ...Figura 4a LAYOUT PSS MONOFORBICE WITH FLAP 52 ...
Page 16: ...Figura 4b LAYOUT PSS MONOFORBICE ESTENSION WITH FRAME 53 ...
Page 17: ...Figura 4c LAYOUT PSS MONOFORBICE FLAP WITH FRAME 54 ...
Page 21: ...Figure 7 ELECTRICAL DIAGRAM 58 ...
Page 29: ...Figure 16 HIDRAULIC HOSE CONECTION 66 A B F C ...