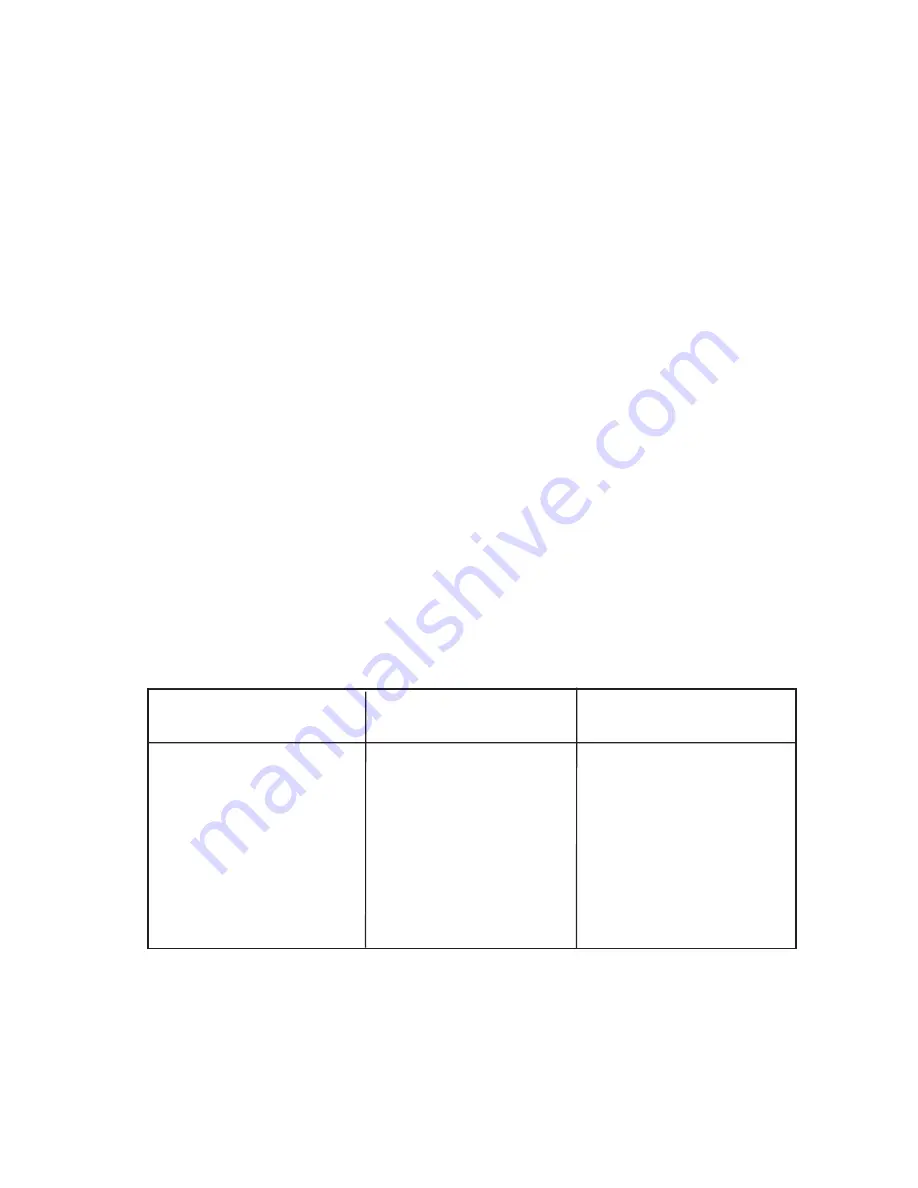
OM-2028
010187
Revised 042393
Revised 071596
OPERATION AND MAINTENANCE
MANUAL
with
ILLUSTRATED PARTS LIST
for
ENGINE-DRIVEN GENERATOR SET
Series Numbers 6910, 6910A, 6910B, 6910C
MODEL 90 GT 20
90-KVA, 400-HZ, 115/200-V AC, 3-PHASE
Specification Number
Mounting
Voltage Regulator Used
6910-1, 6910A-1, 6910B-1
Trailer or Truck
430391C
6910C-1
6910A-2, 6910B-2, 6910C-2
Trailer or Truck
489812A
6910A-3, 6910B-3, 6910C-3
Fixed Unit W/Fuel
Tank & Batteries
489812A
6910B-4, 6910C-4
4-Wheel trailer, 5th Wheel
Trailer, or Truck
489812A
6910B-5, 6910C-5
Tractor
489812A
Hobart Brothers Company
Airport Systems Group
Ground Power Equipment
Troy, Ohio 45373
U.S.A.
Summary of Contents for 6910
Page 2: ...This page intentionally left blank ...
Page 14: ...This page intentionally left blank OM 2028 Introduction June 20 89 Revised Page 2 ...
Page 40: ...This page intentionally left blank OM 2028 1 1 May 1 91 Revised Page 26 ...
Page 66: ...Engine Control Panel in Tilt out Position Figure 6 OM 2028 2 1 August 31 90 Revised Page 12 ...
Page 72: ...This page intentionally left blank OM 2028 2 2 June 20 89 Revised Page 6 ...
Page 128: ...Generator Set Figure 1 OM 2028 4 3 May 1 91 Revised Page 2 ...
Page 130: ...Canopy Assembly Figure 2 OM 2028 4 3 May 1 91 Revised Page 4 ...
Page 132: ...This page intentionally left blank OM 2028 4 3 May 1 91 Revised Page 6 ...
Page 134: ...Generator Set Without Canopy Figure 3 OM 2028 4 3 May 1 91 Revised Page 8 ...
Page 136: ...This page intentionally left blank OM 2028 4 3 May 1 91 Revised Page 10 ...
Page 138: ...Radiator and Cooling System Group Figure 4 OM 2028 4 3 May 1 91 Revised Page 12 ...
Page 142: ...Electric Governor Kit Figure 6 OM 2028 4 3 May 1 91 Revised Page 16 ...
Page 144: ...Fuel Lines Assembly Figure 7 OM 2028 4 3 May 1 91 Revised Page 18 ...
Page 146: ...Oil Line Assembly Figure 8 OM 2028 4 3 May 1 91 Revised Page 20 ...
Page 148: ...Stator Terminal Panel Assembly Figure 9 OM 2028 4 3 May 1 91 Revised Page 22 ...
Page 150: ...Power Module Panel Assembly Figure 10 OM 2028 4 3 May 1 91 Revised Page 24 ...
Page 152: ...Control Box Assembly Figure 11 OM 2028 4 3 May 1 91 Revised Page 26 ...
Page 154: ...Generator Controls Tray Assembly Figure 12 OM 2028 4 3 May 1 91 Revised Page 28 ...
Page 156: ...Protective Relays Tray Assembly Figure 13 OM 2028 4 3 May 1 91 Revised Page 30 ...
Page 158: ...Control Box and Internal Components Group Figure 14 OM 2028 4 3 May 1 91 Revised Page 32 ...
Page 160: ...Engine Control Panel Assembly Figure 15 OM 2028 4 3 May 1 91 Revised Page 34 ...
Page 162: ...This page intentionally left blank OM 2028 4 3 May 1 91 Revised Page 36 ...
Page 164: ...Output Terminal Board Assembly Figure 16 OM 2028 4 3 May 1 91 Revised Page 38 ...
Page 166: ...Generator Assembly Figure 17 OM 2028 4 3 May 1 91 Revised Page 40 ...
Page 168: ...Mounting Frame Assembly and Lifting Yoke Figure 18 OM 2028 4 3 May 1 91 Revised Page 42 ...
Page 170: ...Water Heater Figure 19 OM 2028 4 3 May 1 91 Revised Page 44 ...
Page 172: ...This page intentionally left blank OM 2028 4 3 May 1 91 Revised Page 46 ...
Page 174: ...This page intentionally left blank OM 2028 5 0 May 1 91 Revised Page 2 ...
Page 176: ...This page intentionally left blank OM 2028 6 0 June 20 89 Revised Page 2 ...
Page 177: ... I I I I I l zE I I 01 39NVN jlOVlQ t __ ...
Page 178: ......
Page 179: ......
Page 180: ......
Page 181: ......
Page 182: ......
Page 183: ......
Page 184: ......
Page 186: ......
Page 187: ......
Page 188: ......
Page 189: ......
Page 190: ......
Page 191: ......
Page 192: ......
Page 193: ......
Page 194: ......
Page 195: ......
Page 196: ......
Page 198: ......
Page 199: ......
Page 200: ......
Page 201: ......
Page 202: ......
Page 203: ......
Page 204: ......
Page 205: ......
Page 206: ......