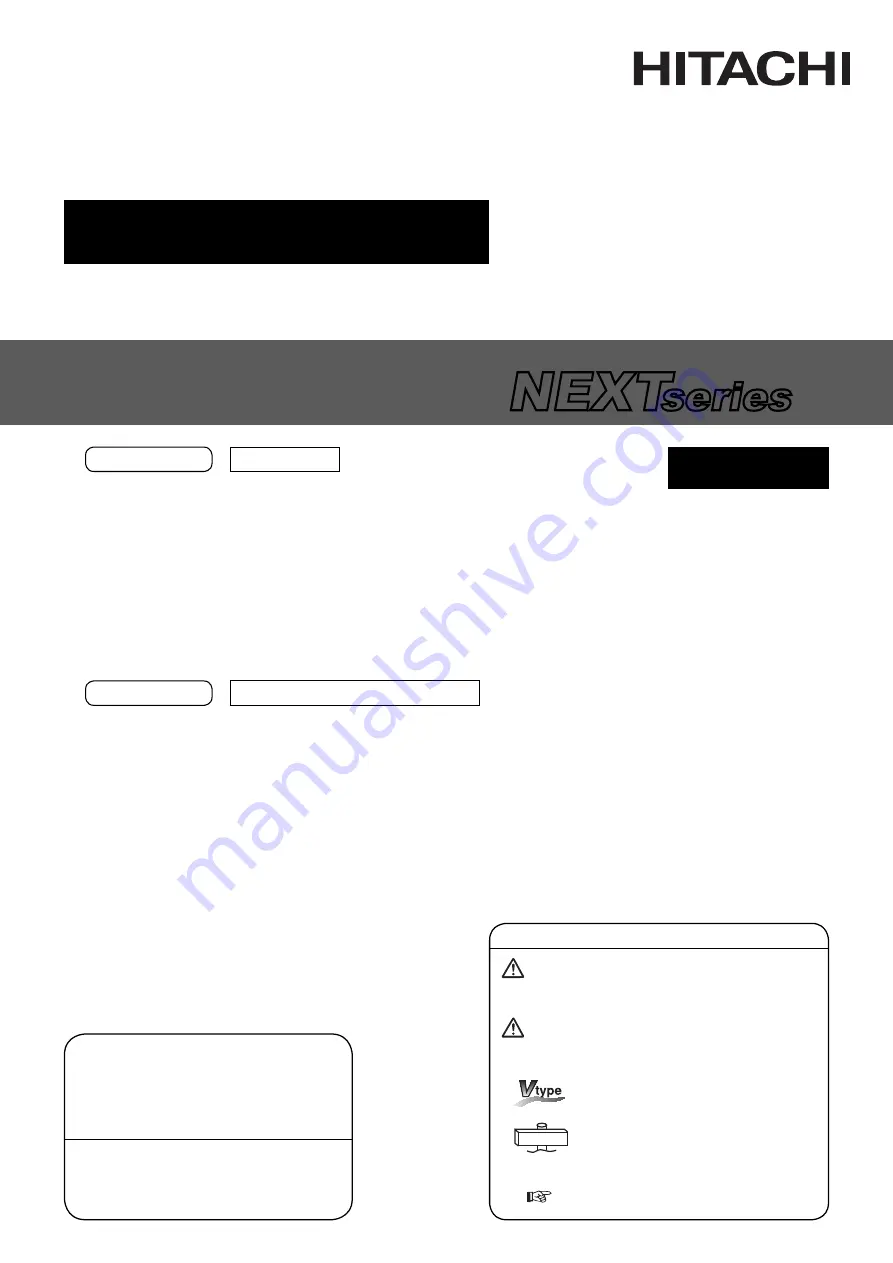
INSTRUCTION MANUAL
DSP-132W6N
DSP-145W6N
DSP-160W6N
DSP-200W6N
DSP-240W6N
●
This INSTRUCTION MANUAL explains in detail
the important items that require attention;
observed as the following:
●
Always observe notations of WARNING, CAUTION
and IMPORTANT, as they indicate considerable
risks to safety.
NEXT
series
Water-Cooled
GRAPHIC DESCRIPTIONS:
WARNING
CAUTION
IMPORTANT
TWO STAGE
Prior to operation of this air compressor,
ensure that all operators read and
understand this INSTRUCTION MANUAL
completely, thereby operating it safely
and properly.
Place the INSTRUCTION MANUAL near
the air compressor to make it available
at any time, and refer to it as the need
arises.
:
This is a warning. If handled improp-
erly, death or severe injury could
result.
:
This is a caution. If handled improp-
erly, injury and/or physical damage
could result.
:
This graphic is for items that need
attention, other than WARNING and
CAUTION.
:
This graphic is a page number reference.
:
This graphic is
Variable Speed-control
Drive (VSD) models.
HITACHI Oil-Free Rotary Screw Air Compressor
Fixed Speed
DSP-160V6WN
DSP-240V6WN
Variable Speed Drive Control
Water-Cooled