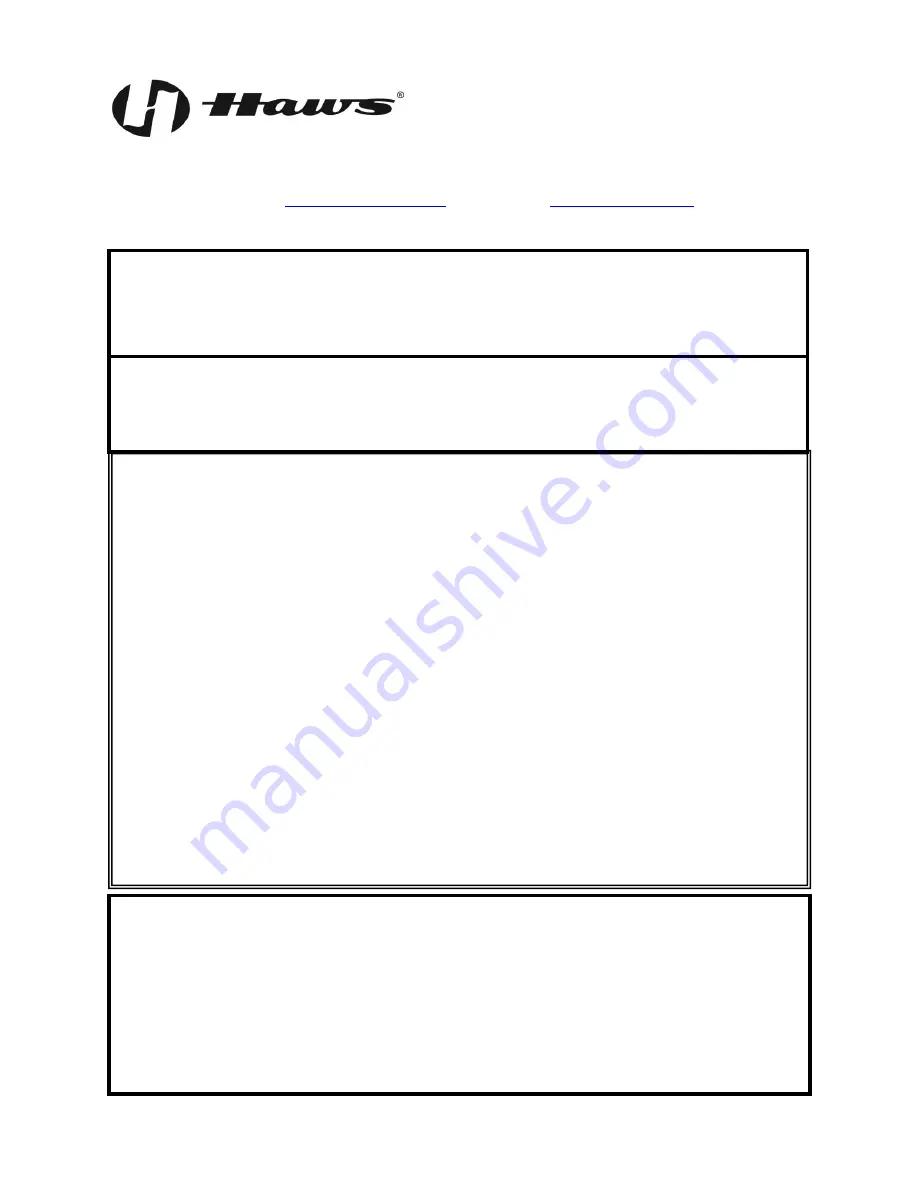
01/21 1210 Series Bottle Fillers
Page 1 of 17
1455 Kleppe Lane
Sparks, NV 89431-6467
(775) 359-4712
Fax (775) 359-7424
E-mail:
website:
No. 0510001059 (1)
Bottle Filling Stations
MODELS 1210S AND 1210SF
INSTALLATION, OPERATION
&
MAINTENANCE INSTRUCTIONS
SAFETY PRECAUTIONS
CAUTION: Disconnect electrical power to outlet before installing or servicing.
NOTICE:
A. The electrical receptacle must have code-approved ground-fault circuit
interrupter (GFCI) protection for personnel.
B. Care should be taken not to damage refrigeration system lines or
electrical wires during installation.
C. Installation must conform to all applicable codes and standards.
D. Maintain 8 inches (20cm) separation from filter circuit board (antenna) at
all times.
NOTE TO INSTALLER: Please leave this information with the Maintenance Department.
FULL-SCALE ROUGH-IN TEMPLATE (PN 0510001160) AVAILABLE UPON REQUEST.
SHOULD YOU EXPERIENCE DIFFICULTY WITH THE INSTALLATION OF THIS
MODEL PLEASE CALL:
TECHNICAL SUPPORT:
1-800-766-5612
FOR CUSTOMER SERVICE:
1-888-640-4297