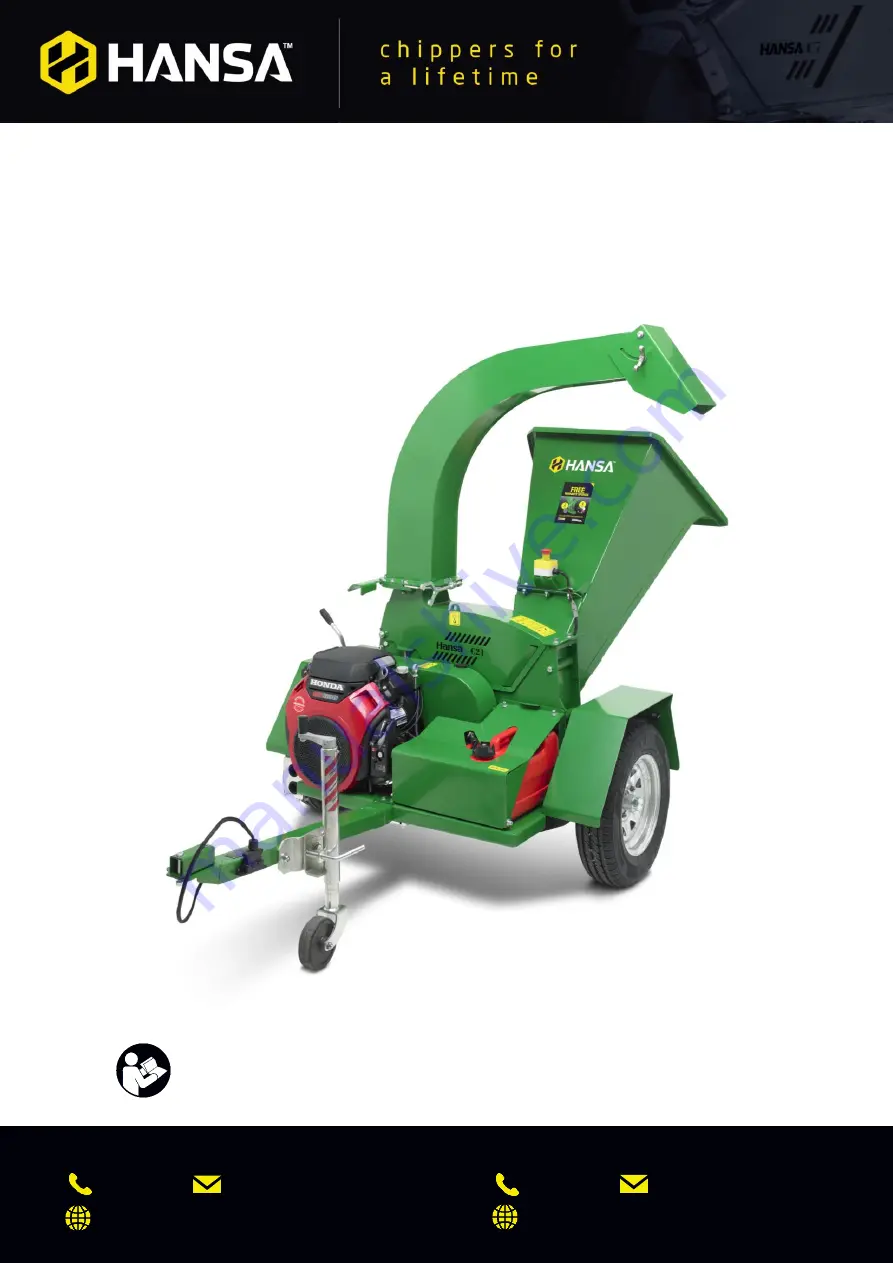
HANSA NEW ZEALAND
+64 7 849 4749 [email protected]
www.hansachippers.com
HANSA AUSTRALIA
1800 248 199 [email protected]
www.hansachippers.com.au
HANSA NEW ZEALAND
+64 7 849 4749 [email protected]
www.hansaproducts.co.nz
HANSA AUSTRALIA
1800 426 722 [email protected]
www.hansaproducts.com.au
Hansa C21
Operation, maintenance and safety manual
All operators must fully read and underst
and this operator’s manual
before using the chipper.