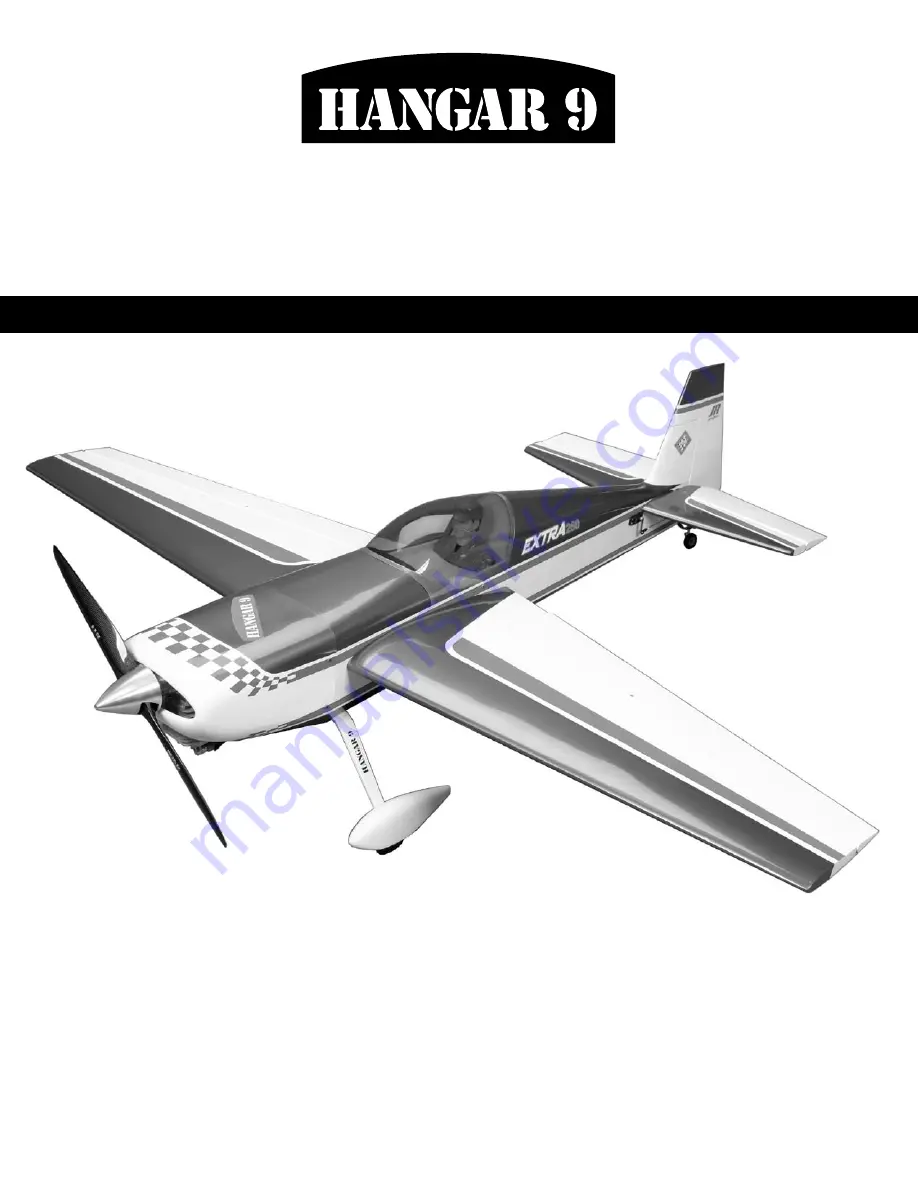
ASSEMBLY MANUAL
Specifications
Wingspan: ............. 78.25 in (198.8 cm)
Length: ................... 71.25 in (181 cm)
Wing Area: ............ 1134 sq in (73.1 sq dm)
Weight: .................. 12–15.5 lb (5.44–7.0 kg)
Radio: ..................... 4-channel w/6 servos
Recommended Engines:
2-Stroke ............1.20–2.10
4-Stroke ............1.50–2.20
Gas .....................35–50cc
Extra 260
��
�
• Awsome IMAC and 3D performer
• Lightweight construction
• Designed by aerobatic veteran Mike McConville
• 90% factory built ARF
• Plug-in wings and stabilizers for easy transport and field assembly