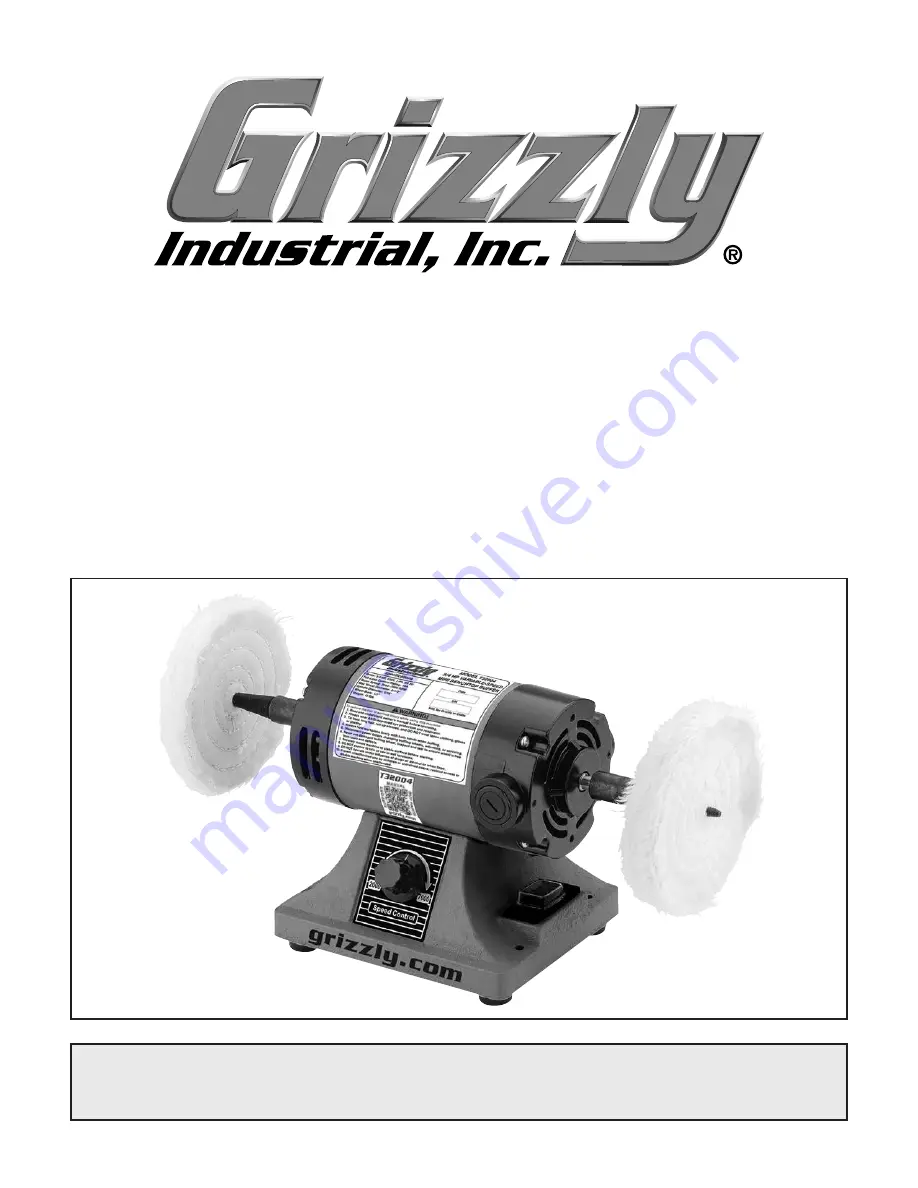
COPYRIGHT © MAY, 2020 BY GRIZZLY INDUSTRIAL, INC.
WARNING: NO PORTION OF THIS MANUAL MAY BE REPRODUCED IN ANY SHAPE
OR FORM WITHOUT THE WRITTEN APPROVAL OF GRIZZLY INDUSTRIAL, INC.
#CS20952 PRINTED IN CHINA
V1.05.20
MODEL T32004
3/4 HP VARIABLE-SPEED
MINI BENCHTOP BUFFER
OWNER'S MANUAL
(For models manufactured since 02/20)
Summary of Contents for T32004
Page 32: ......