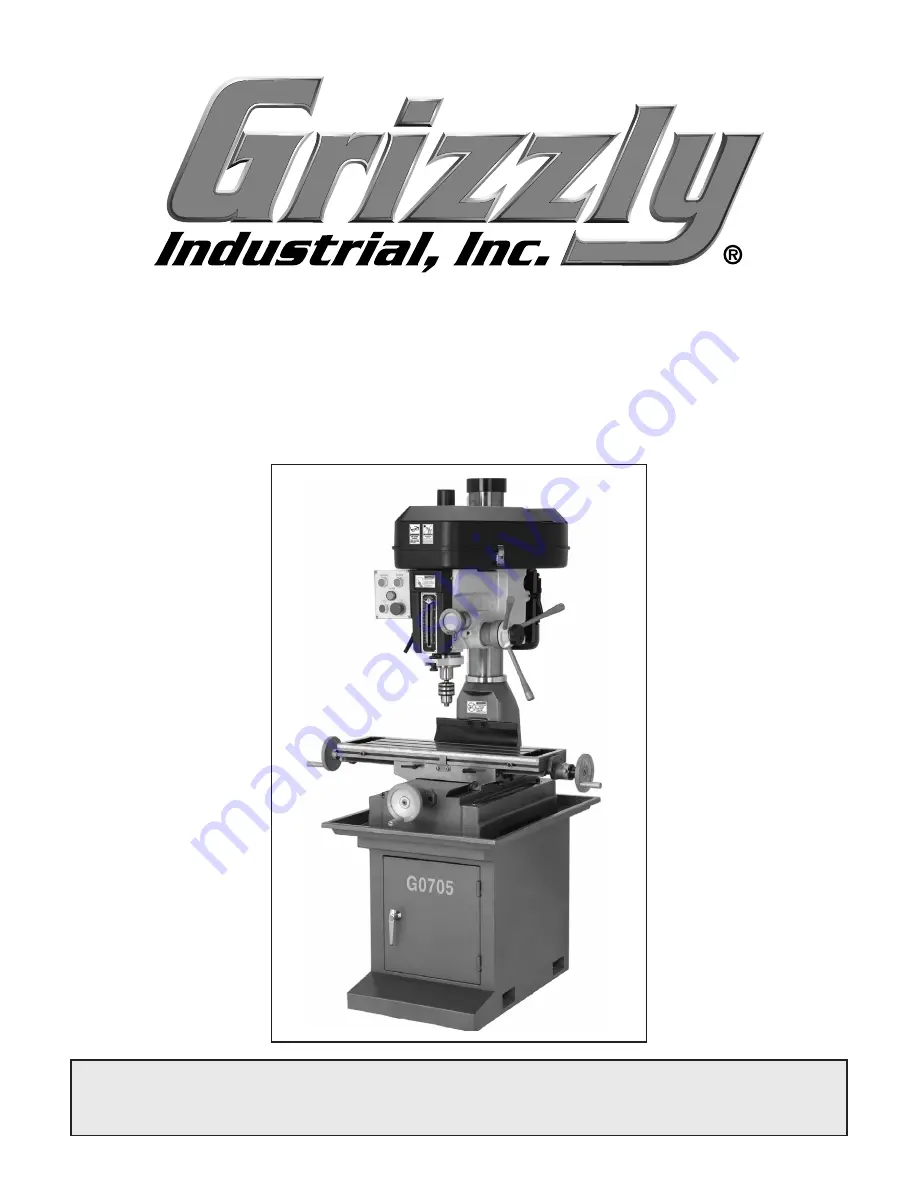
Copyright © MarCh, 2010 By grizzly industrial, inC. revised deCeMBer, 2010 (JB)
Warning: no portion of this manual may be reproduced in any shape
or form Without the Written approval of grizzly industrial, inc.
(For Models ManuFaCtured sinCe 09/09) #JB12469 printed in China
model g0705
mill/drill w/stand
oWner's manual