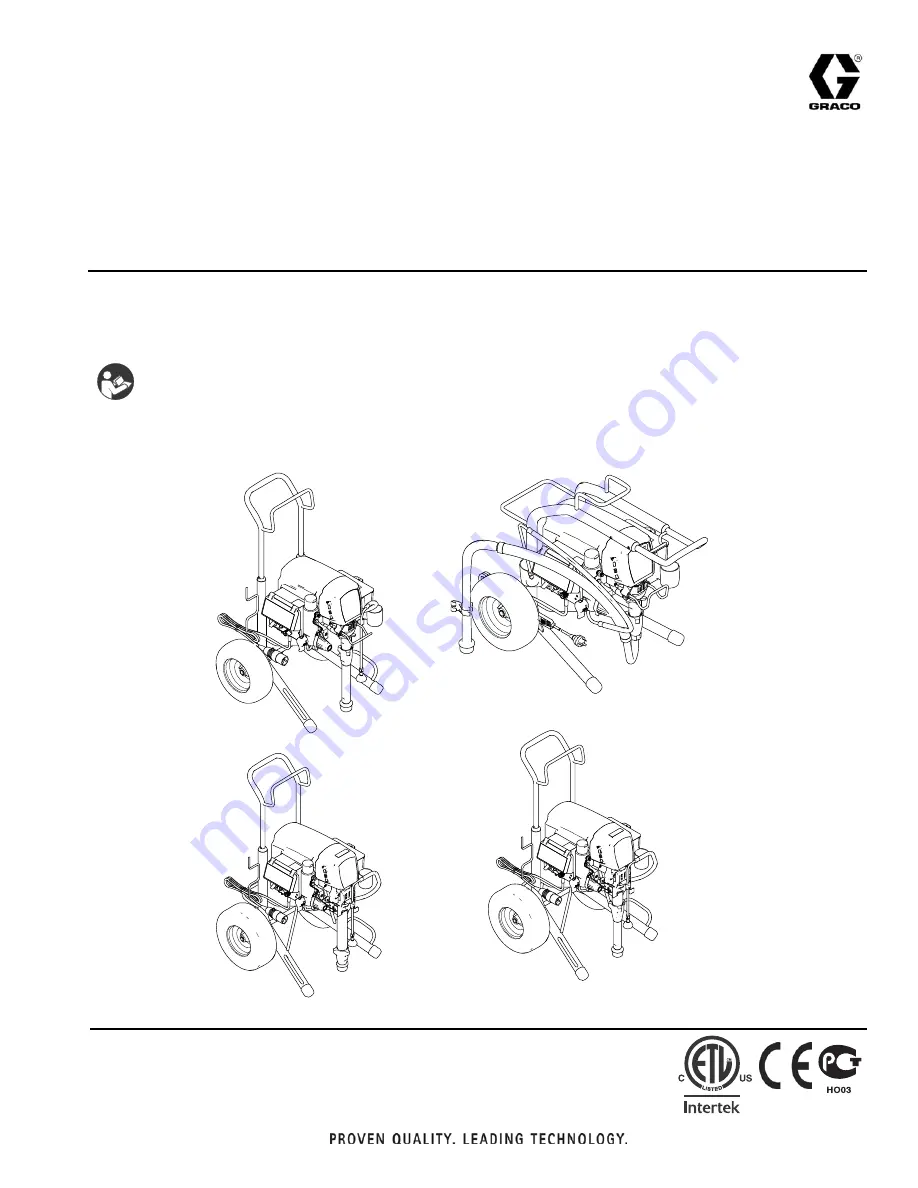
311365H
ENG
Ultra
®
Max II/Ultimate Mx II
- For Portable Airless Spraying of Architectural Coatings and Paints. For professional use only.
Not for use in explosive atmospheres.-
3300 psi (22.8 MPa, 227 bar) Maximum Working Pressure
See page 3 for model information, including maximum working pressure and approvals.
Korean patent 10-0579681
IMPORTANT SAFETY INSTRUCTIONS
Read all warnings and instructions in this
manual. Save these instructions.
MARK V
ti13461a
ti13460a
1095/1595 HI
ti13459a
695/795 LOW
695/795 HI
ti13450a
Repair
Summary of Contents for ultimate mx ii
Page 33: ...Notes 311365H 33 Notes ...
Page 47: ...Notes 311365H 47 Notes ...