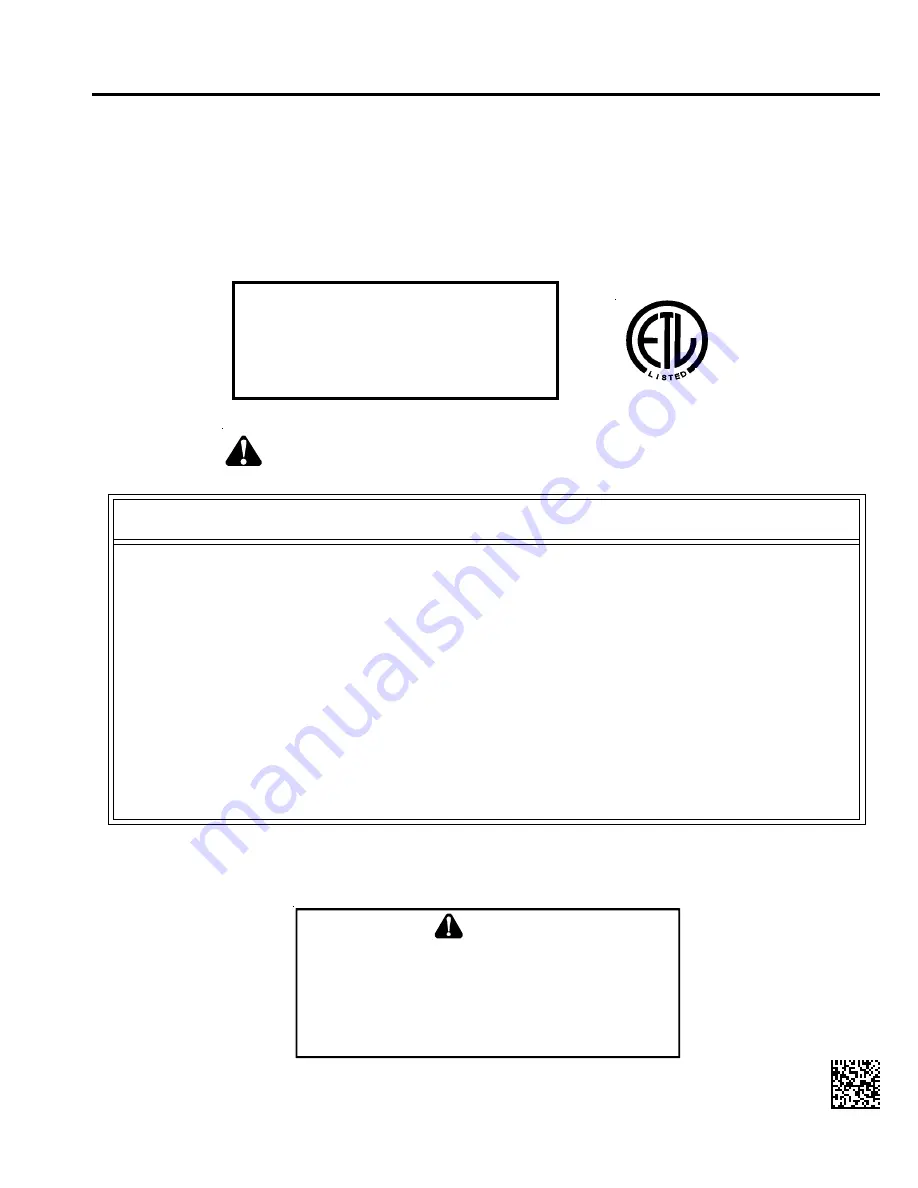
5151 San Felipe Suite 500 • Houston, TX 77056
www.goodmanmfg.com • www.amana-hac.com
C
US
®
ATTENTION INSTALLING PERSONNEL
RECOGNIZE THIS SYMBOL AS A SAFETY PRECAUTION.
Installer: Affix all manuals adjacent to the unit.
These furnaces comply with requirements
embodied in the American National Stan-
dard / National Standard of Canada ANSI
Z21.47·CSA-2.3 Gas Fired Central Furnaces.
As a professional installer, you have an obligation to know the product better than the customer.
This includes all safety precautions and related items.
Prior to actual installation, thoroughly familiarize yourself with this Instruction Manual.
Pay special attention to all safety warnings. Often during installation or repair, it is possible to place yourself
in a position which is more hazardous than when the unit is in operation.
Remember, it is
your
responsibility to install the product safely and to know it well enough
to be able to instruct a customer in its safe use.
Safety is a matter of common sense...a matter of thinking before acting.
Most dealers have a list of specific, good safety practices...follow them.
The precautions listed in this Installation Manual are intended as supplemental to existing practices.
However, if there is a direct conflict between existing practices and the content of this manual,
the precautions listed here take precedence.
NOTE
: Please contact your distributor or our website for the applicable Specification Sheet
referred to in this manual.
G
OODMAN
WILL
NOT
BE
RESPONSIBLE
FOR
ANY
INJURY
OR
PROPERTY
DAMAGE
ARISING
FROM
IMPROPER
SERVICE
OR
SERVICE
PROCEDURES
.
I
F
YOU
INSTALL
OR
PERFORM
SERVICE
ON
THIS
UNIT
,
YOU
ASSUME
RESPONSIBILITY
FOR
ANY
PERSONAL
INJURY
OR
PROPERTY
DAMAGE
WHICH
MAY
RESULT
.
M
ANY
JURISDICTIONS
REQUIRE
A
LICENSE
TO
INSTALL
OR
SERVICE
HEATING
AND
AIR
CONDITIONING
EQUIPMENT
.
WARNING
©
2009 Goodman Manufacturing Company, L.P.
IO-359C
9/09
IIIII
NST
NST
NST
NST
NSTALLA
ALLA
ALLA
ALLA
ALLATION
TION
TION
TION
TION
I
I
I
I
I
NSTRUC
NSTRUC
NSTRUC
NSTRUC
NSTRUCTIONS
TIONS
TIONS
TIONS
TIONS
FOR
FOR
FOR
FOR
FOR
*M(H,S)8 / *D(H,S)8 / *HS8 / GME8 G
*M(H,S)8 / *D(H,S)8 / *HS8 / GME8 G
*M(H,S)8 / *D(H,S)8 / *HS8 / GME8 G
*M(H,S)8 / *D(H,S)8 / *HS8 / GME8 G
*M(H,S)8 / *D(H,S)8 / *HS8 / GME8 G
AS
AS
AS
AS
AS
F
F
F
F
F
URNA
URNA
URNA
URNA
URNACE
CE
CE
CE
CE
(CATEGORY I )