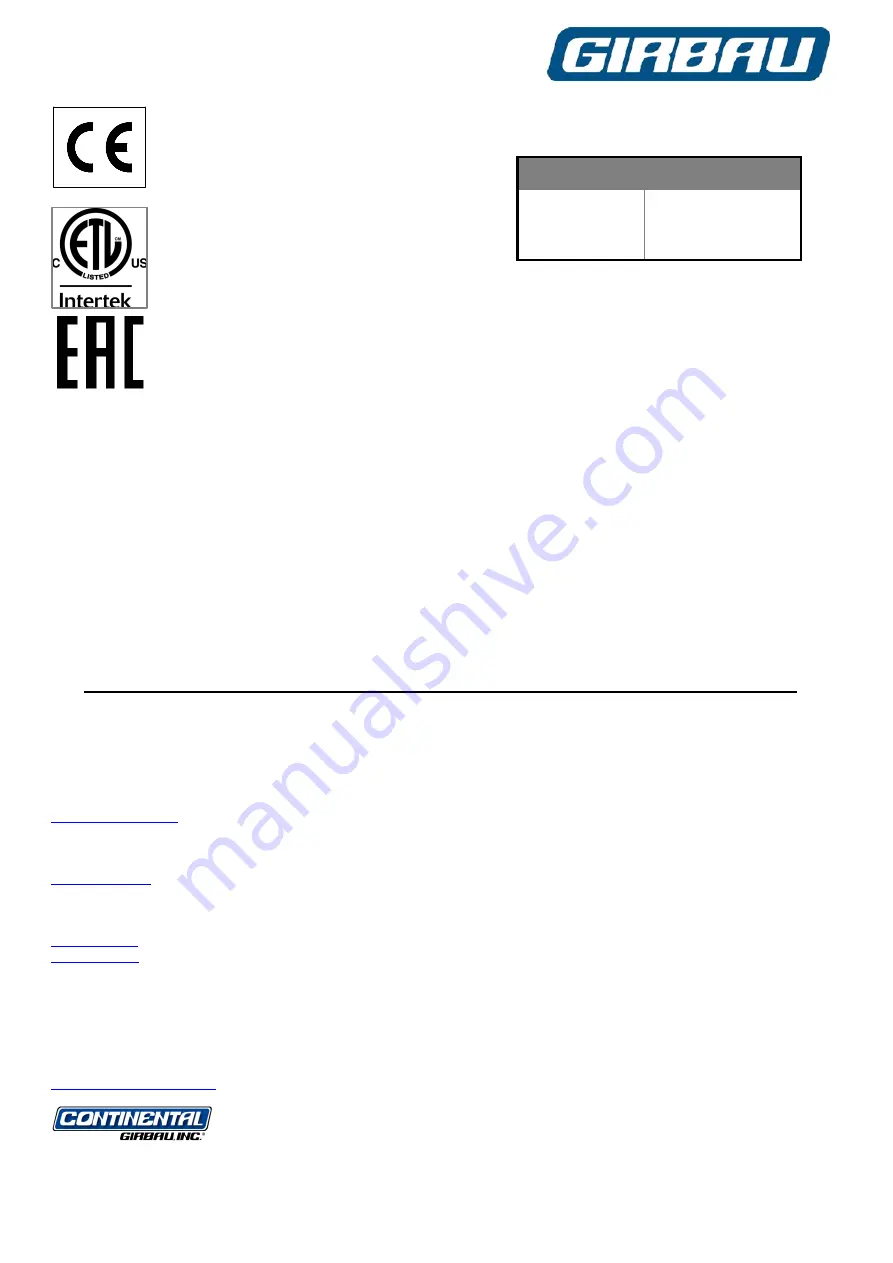
Code no. 550038
Rev. no. 16/1018
Model
From Machine No.
PB32
PB/PBP51
X13
X20
2,175,001
2,190,001
2,205,001
2,210,001
Installation, Operation
and
Maintenance
Instruction manual for
Flatwork Ironer
GIRBAU, SA
Crta de Manlleu, km. 1
08500 VIC (Barcelona)
SPAIN
National sales:
Tel. (+ 34) 902 300 359
International sales:
Tel. (+ 34) 938 862 219
Service:
Tel. (+ 34) 902 300 357
For
USA & CANADA:
CONTINENTAL GIRBAU Inc.
2500 State Road 44
WI 54904 Oshkosh
USA
Tel. 1(920) 231-8222
[email protected]
EN
PB32
PB/PBP51
X13***W
X20***W/F