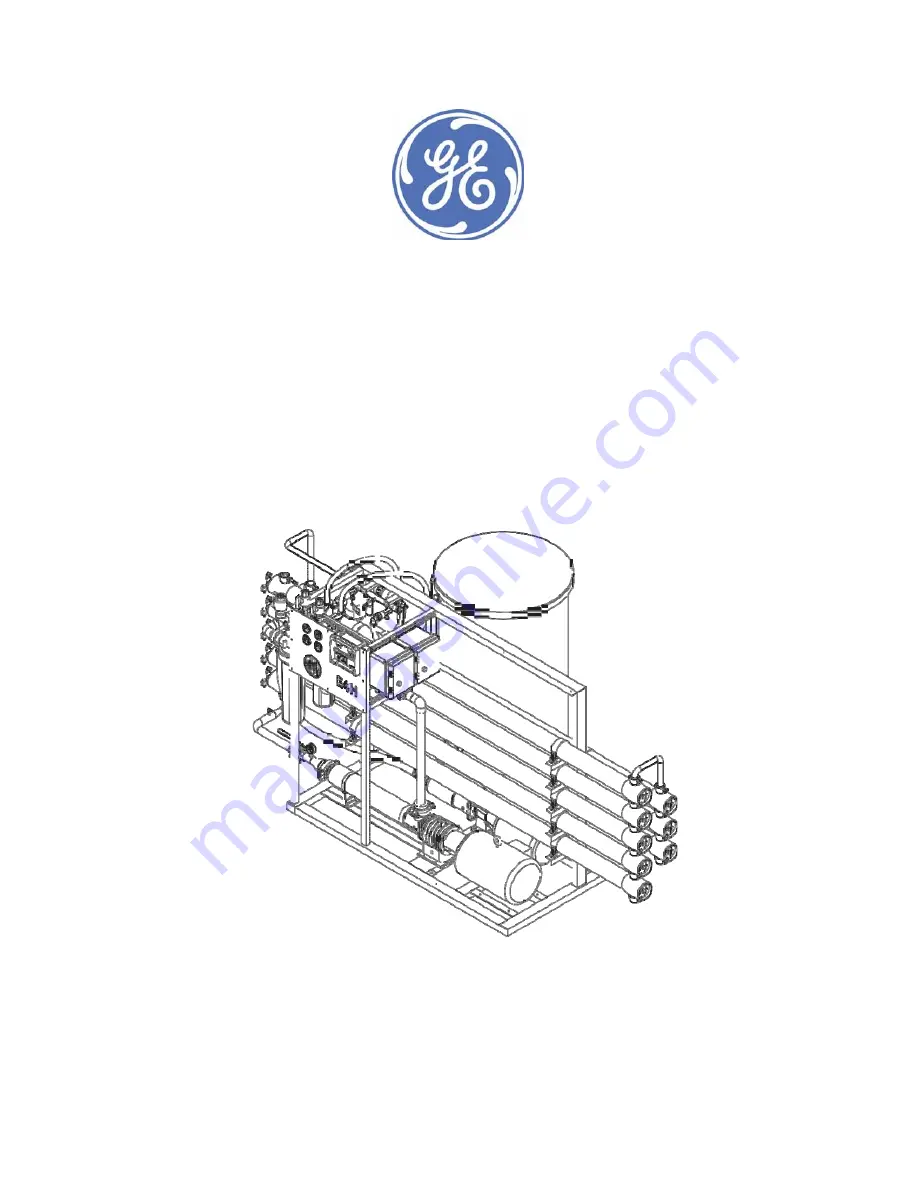
OPERATIONS AND MAINTENANCE MANUAL
E4H Series Water Purification Machines
16,000 GPD to 43,200 GPD
60.6 m
3
/day to 163.5 m
3
/day
NOTICE
The enclosed materials are considered proprietary property of GE Water & Process Technologies. No assignments, either implied or expressed, of
intellectual property rights, data, know-how, trade secrets or licenses of use thereof are given. All information is provided exclusively for the addressee for
the purposes of evaluation and is not to be reproduced or divulged to other parties, nor used for manufacture or other means, or to authorize any of the
above, without the express written consent of GE Water & Process Technologies. The acceptance of this document will be construed as an acceptance of
the foregoing conditions. * Trademark of General Electric Company; may be registered in one or more countries.