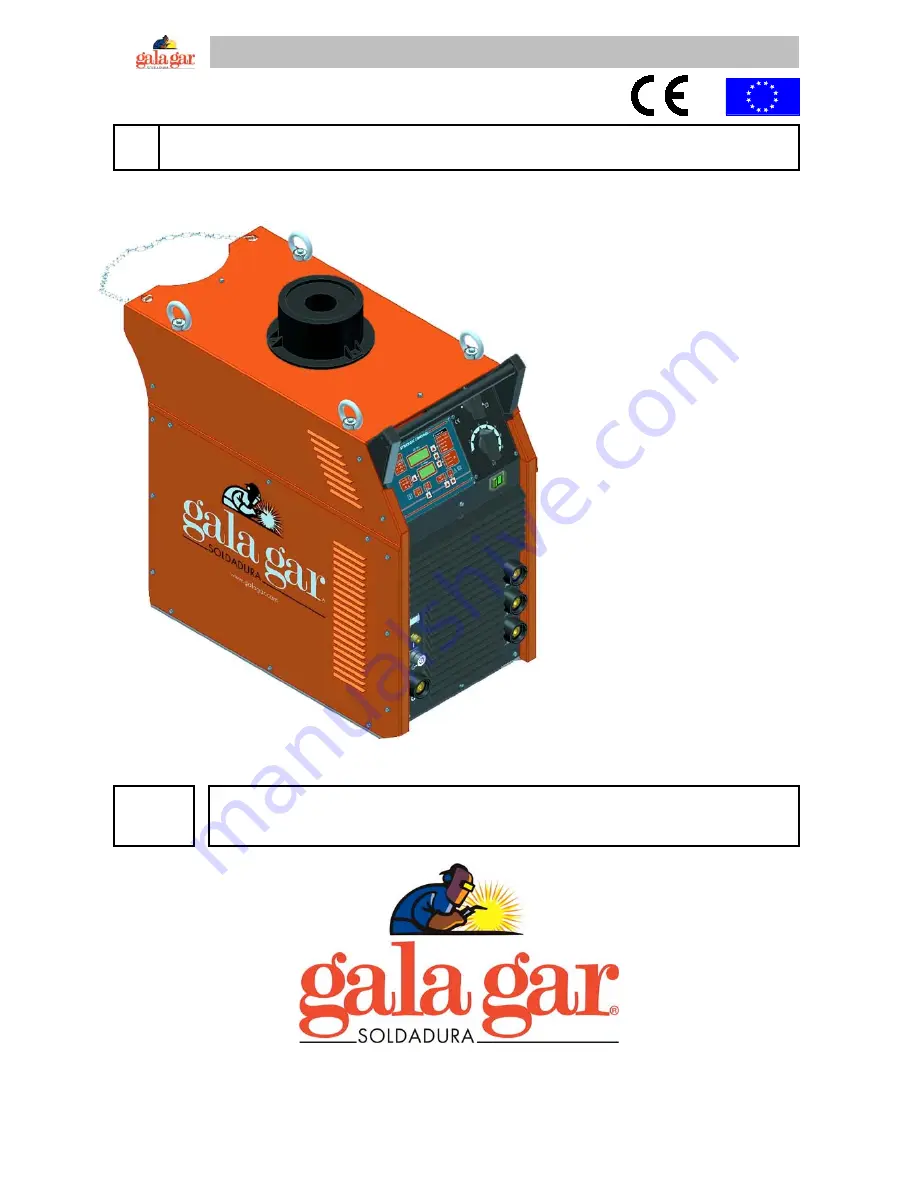
GALA SYNERGIC 5000
GB
TECHNICAL INSTRUCTIONS MANUAL. POWER SOURCES.
INDUSTRIAL MIG/MAG WELDING EQUIPMENT OF SYNERGIC CONTROL.
GALA Synergic
5000
(3Ph - 230/400V 50/60 Hz)
Ref. 432.00.000
GB
THIS EQUIPMENT MUST BE USED BY PROFESSIONALS.
TO HELP YOU IN YOUR WORK CAREFULLY READ THIS MANUAL.
Jaime Ferrán 19 50014 ZARAGOZA (Spain)
TLF.-34/976473410 FAX.-34/976472450
Ref. 43217545/Ed0