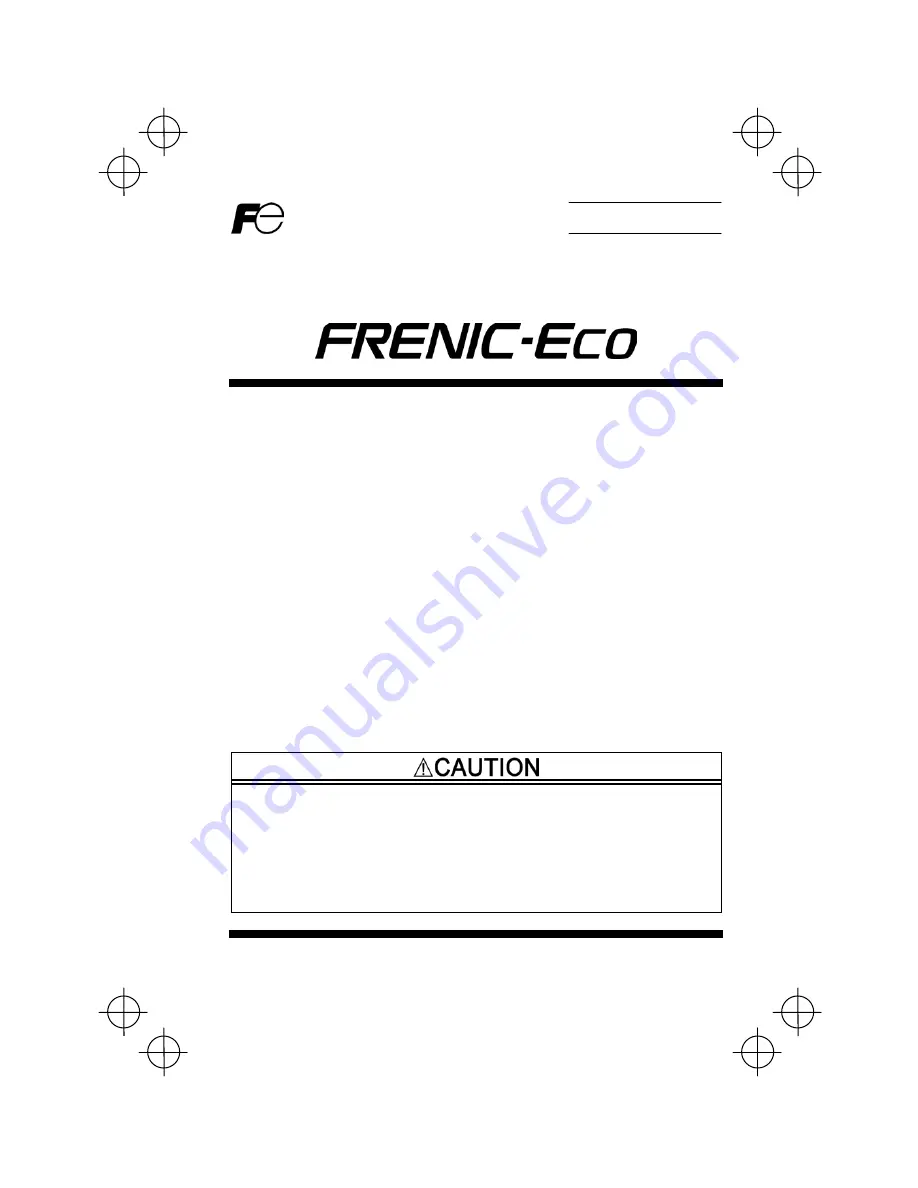
Instruction Manual
Designed for Fan and Pump Applications
Thank you for purchasing our FRENIC-Eco series of inverters.
• This product is designed to drive a three-phase induction motor. Read through this instruction manual and
be familiar with the handling procedure for correct use.
• Improper handling might result in incorrect operation, a short life, or even a failure of this product as well as
the motor.
• Deliver this manual to the end user of this product. Keep this manual in a safe place until this product is
discarded.
• For how to use an optional device, refer to the installation and instruction manuals for that optional device.
Fuji Electric FA Components & Systems Co., Ltd.
Fuji Electric Corp. of America
INR-SI47-1225-E
Summary of Contents for FRENIC-ECO
Page 111: ...5 3 F codes Fundamental Functions The shaded function codes are applicable to the quick setup...
Page 114: ...5 6 F code continued...
Page 115: ...5 7 E codes Extension Terminal Functions...
Page 116: ...5 8 E code continued...
Page 119: ...5 11 E code continued...
Page 121: ...5 13 P codes Motor Parameters The shaded function codes are applicable to the quick setup...
Page 122: ...5 14 H codes High Performance Functions...
Page 123: ...5 15 H code continued...
Page 126: ...5 18 J code continued...
Page 127: ...5 19 J code continued...
Page 128: ...5 20 y codes Link Functions...
Page 129: ...5 21 y code continued...
Page 141: ...5 33 Example of Operating Characteristics...
Page 217: ...8 6 8 3 Common Specifications...
Page 218: ...8 7...
Page 223: ...8 12 8 5 External Dimensions 8 5 1 Standard models Unit inch mm 10 2 260...
Page 227: ...8 16 8 5 3 Multi function Keypad Unit inch mm...
Page 246: ...Fuji Electric FA Components Systems Co Ltd Fuji Electric Corp of America 2007 11 K07 K07 10CM...