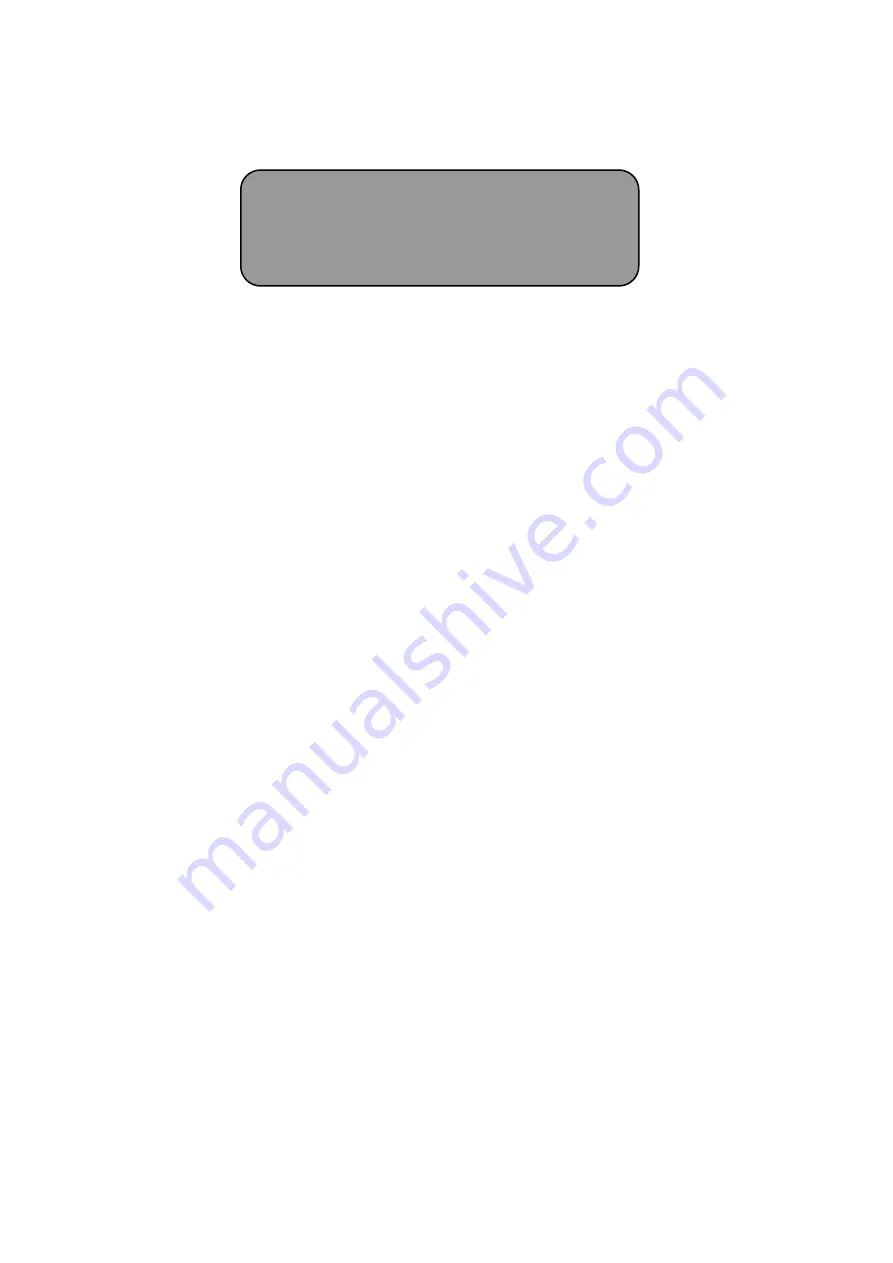
SH2000
HOT AIR CONTINUOUS HEAT SEALER
INSTRUCTION
AND
MAINTENANCE
MANUAL
FISCHBEIN-SAXON LTD
Incorporating The Thames Packaging Equipment Company and Fischbein Ltd
Alexandra Business Centre, 274 Alma Road, Enfield, Middlesex, EN3 7RS, England
Telephone: +44 (0) 844 3722 877 Fax: +44 (0) 844 3722 876
Manual No 82.150 Rev 100315
Summary of Contents for Saxon SH 2000
Page 6: ...SH2000 82 150 Rev 100315 6...
Page 8: ...SH2000 82 150 Rev 100315 8...
Page 10: ...SH2000 82 150 Rev 100315 10...
Page 41: ...SH2000 82 150 Rev 100315 41 NOTES ROUTINE MAINTENANCE...
Page 59: ...SH2000 82 150 Rev 100315 59 10 3 2000 Series Trolley Unit MACHINE LAYOUTS...
Page 60: ...SH2000 82 150 Rev 100315 60 ANNEX Section 7 1 2 Annex Section 7 Plug and Socket Assembly...
Page 61: ...SH2000 82 150 Rev 100315 61 ANNEX Section 7 3 4...
Page 62: ...SH2000 82 150 Rev 100315 62 ANNEX Section 7 5 6...
Page 63: ...SH2000 82 150 Rev 100315 63 ANNEX Section 7 7 8...
Page 64: ...SH2000 82 150 Rev 100315 64 ANNEX Section 7 9 10...
Page 65: ...SH2000 82 150 Rev 100315 65 ANNEX Section 7 11 12...
Page 66: ...SH2000 82 150 Rev 100315 66 ANNEX Section 7 13 14...
Page 67: ...SH2000 82 150 Rev 100315 67 ANNEX Section 7 15 16...