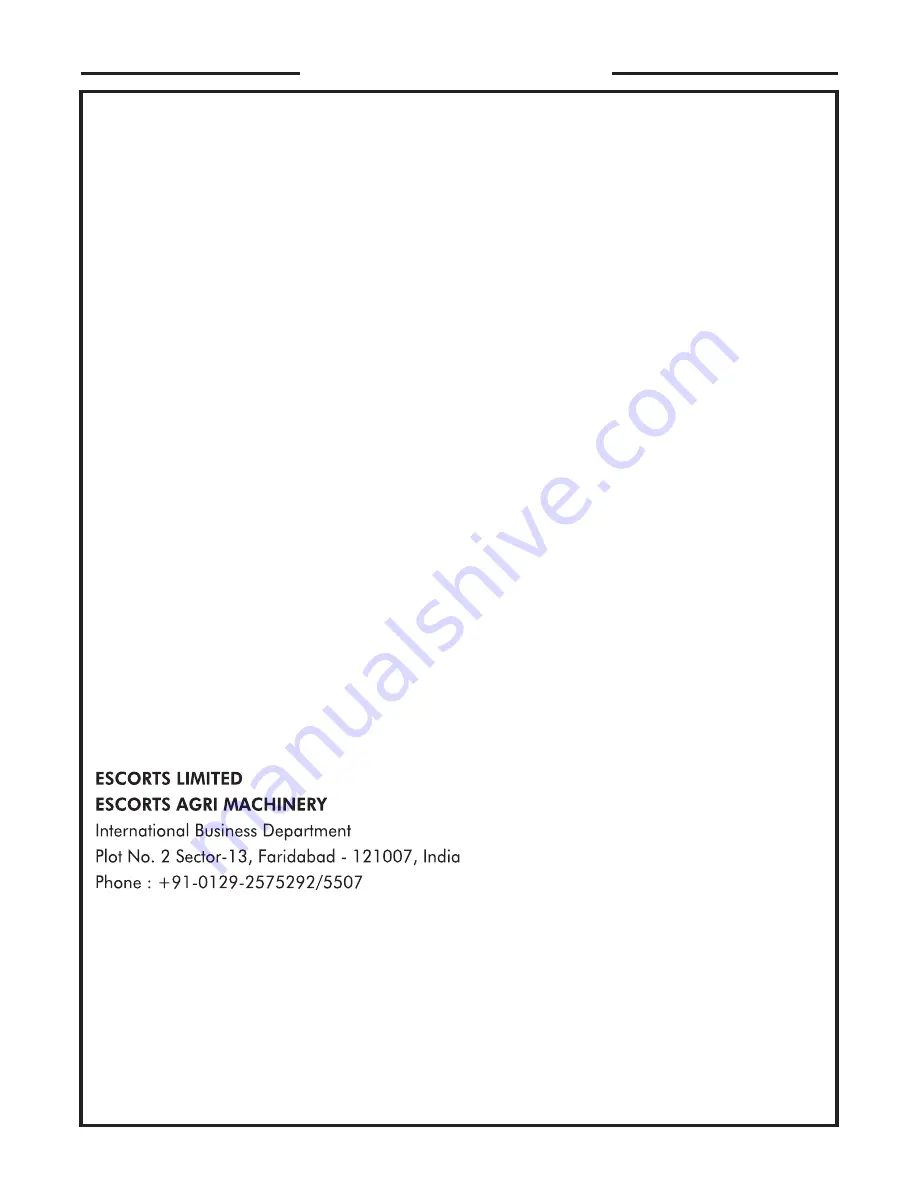
NOTE TO THE OWNER
Thank you for purchasing your new Farmtrac tractor. :
This Manual has been prepared to assist you in the correct procedure for running-in, driving and operating your
new tractor and to assist you in the correct method of maintenance to keep it in peak condition.
Your tractor has been designed and built to give maximum performance, economy and ease of operation under a
wide variety of operating conditions. Prior to delivery, the tractor was carefully inspected, both at the factory and
by your Authorized Dealer to ensure that it reaches you in optimum condition. To maintain this condition and
ensure trouble-free operation, it is important that the routine services, as specified in this manual, are carried out
at the recommended intervals.
The precautions to be observed to ensure your safety and the safety of others. Read the safety precautions and
follow the advice offered before operating the tractor.
The vehicle reference serial number are also recorded on the pre-delivery inspection sheet that was provided to
you by your Authorized Dealer and should be quoted to the Dealer should the tractor require service.
Read this Manual carefully and keep it at a convenient place for future reference. This manual must be considered
as an integral part of your tractor. If at any time you require service or advice concerning your tractor, do not
hesitate to contact your Authorized Dealer. He has trained personnel, genuine parts and the necessary
equipment to carry out all your service requirements.
Following these introductory pages, this manual is split into four sections. Section A describes the controls and
instruments and advises the correct method of operating your new tractor. Section B details lubrication and
maintenance procedures and includes a comprehensive service chart. Section C outlines the specifications of
your tractor.
Escorts Limited has a Company policy of continuous improvement and development. Designs, materials and
specifications are subject to change without notice and without any liability whatsoever.
All data given in this book is subject to production variations. Dimensions and weights are approximate only and
the illustrations do not necessarily show tractor in standard condition. Some of the equipment/accessories
described in the text may also not be fitted on your tractor. For exact information about any particular tractor,
please consult your Authorized Dealer.
E-mail - [email protected]
NOTE :
The Operator Manual is in accordance with standard ISO 3600 : 1996.
Summary of Contents for FT 6050 CROSS
Page 4: ... DEALERS S STAMP 2 ...
Page 6: ...4 ...
Page 8: ...6 ...
Page 10: ...8 ...
Page 11: ...9 ...
Page 25: ...SECTION A ...
Page 28: ...SECTION A 3 2 Control Levers ...
Page 52: ...27 NOTE CONTROL INSTRUMENTS AND OPERATION ...
Page 53: ...SECTION B ...
Page 62: ...9 SECTION B 18 17 Parking brake Hub 17 16 Parking brake Hub ...
Page 76: ...23 NOTES SECTION B ...
Page 77: ...24 ...
Page 78: ...25 ...
Page 79: ...26 ...
Page 80: ...FARMTRAC 27 ...
Page 81: ...28 ...
Page 82: ...29 ...
Page 83: ...SECTION C 30 ...
Page 88: ...NOTES SPECIFICATIONS 5 ...