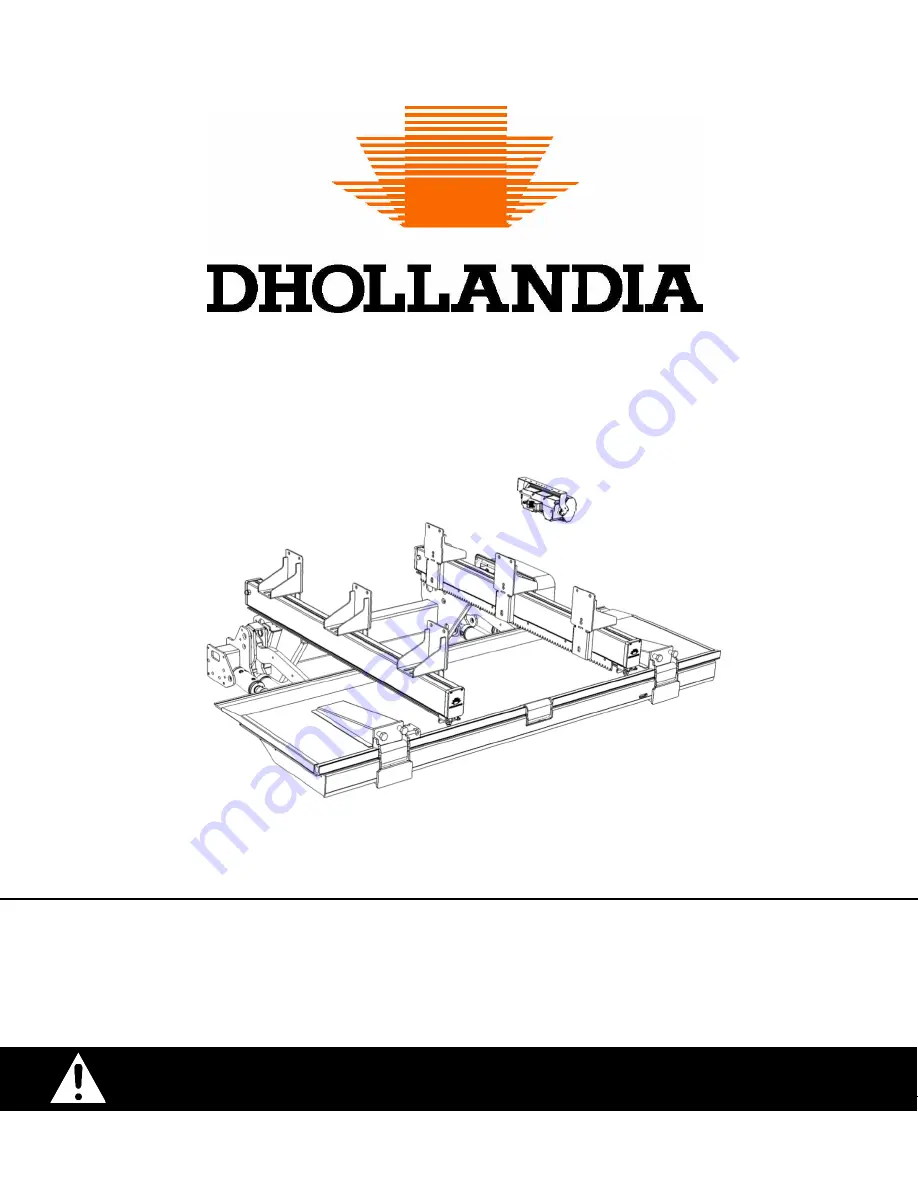
Doc:
FIT_S_US_EN_2019_rev4
Rev:
4
Date: OCTOBER 14, 2019
Manufacturer:
DHOLLANDIA US, L.L.C.
Tel : +1 704 629 5542 E-mail : [email protected]
132 W Virginia Ave
Bessemer City North Carolina, 28016
website : www.dhollandia.com
DH-S*
INSTALLATION MANUAL
Read the manual in its entirety before operating the liftgate
Keep this manual in the vehicle cab, as reference for the driver and liftgate operator
900
–
6,600lbs (400-3000kg)
** Pictured: SM.20 liftgate
Summary of Contents for DH-S Series
Page 11: ...10 DHOLLANDIA 1 2 3 4 5 6 7 8 9 10 11 12 14 15 16 17 13 Figure 6 1...
Page 13: ...12 DHOLLANDIA Figure 6 2...
Page 46: ...45 DHOLLANDIA Figure 11 6 Figure 11 8 Figure 11 7...
Page 49: ...48 DHOLLANDIA...
Page 50: ...49 DHOLLANDIA...
Page 66: ...65 DHOLLANDIA Figure 16 4...
Page 68: ...67 DHOLLANDIA For option OAE510 15 see Figure 16 6 below Figure 16 6...
Page 73: ...72 DHOLLANDIA...
Page 74: ...73 DHOLLANDIA...
Page 75: ...74 DHOLLANDIA...
Page 76: ...75 DHOLLANDIA...
Page 77: ...76 DHOLLANDIA...
Page 78: ...77 DHOLLANDIA...
Page 80: ...79 DHOLLANDIA 16 9 MOUNTING DIAGRAMS...
Page 81: ...80 DHOLLANDIA...