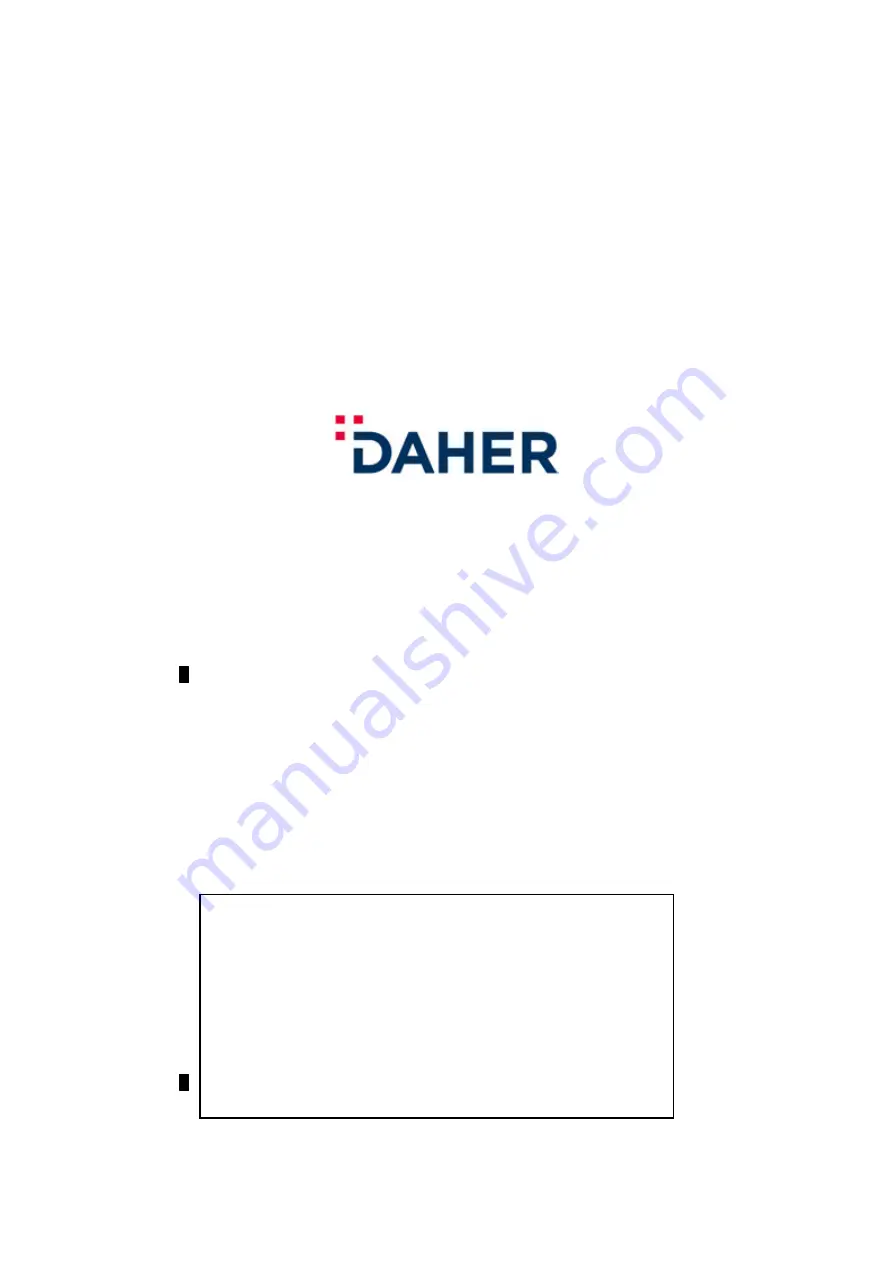
TBM 930
PILOT'S INFORMATION
MANUAL
P/N DMJPIPYEE0 - Edition 1 - Revision 5
▲
CAUTION
▲
This information manual is a non-official copy of the pilot's operating
handbook and may be used for general information purposes only.
It is not kept current and therefore cannot be used as a substitute for
airworthiness authorities approved manual which is the only one
intended for operation of the airplane.
The list of effective pages in this manual corresponds to that of the
basic Pilot's Operating Handbook.
▲
The content of this document is the property of DAHER AEROSPACE. It is
supplied in confidence and commercial security of its contents must be
maintained.
It must not be used for any purpose other than that for which it is
supplied, nor may information contained in it be disclosed to
unauthorized persons. It must not be reproduced nor transmitted in any
form in whole or in part without permission in writing from the owners of
the Copyright.
Information in this document is subject to change without notice.
© 2018, 2019, 2020, 2021 - DAHER AEROSPACE
All rights reserved
DAHER AEROSPACE
Customer care
65921 TARBES CEDEX 9
FRANCE
Printed in FRANCE
PIM - DO NOT USE FOR FLIGHT OPERATIONS