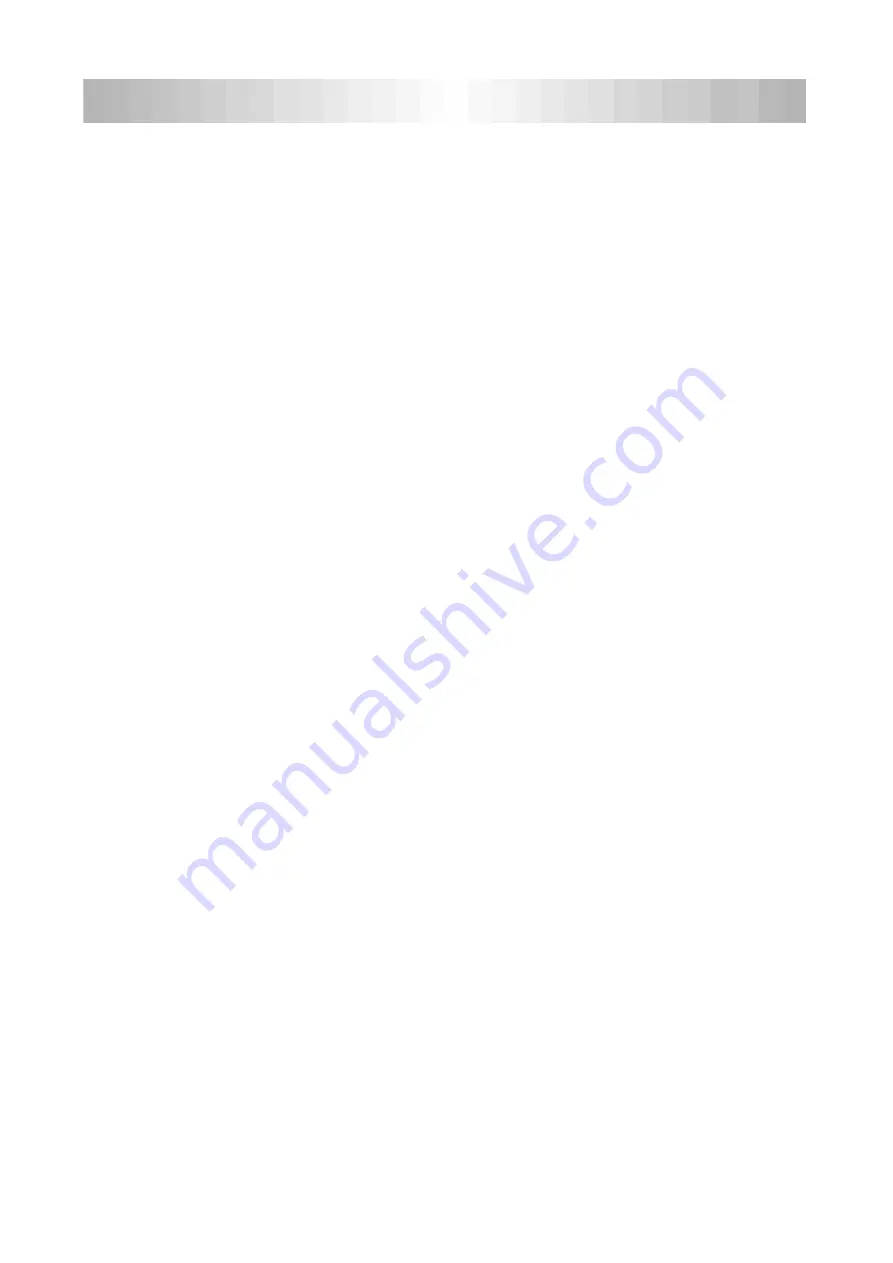
CHAPTER 1. GENERAL
1.1 APPEARANCE
1.2 SPECIFICATIONS
1.3 PERFORMANCE CURVE
1.4 DIMENSIONS
1.5 GENERAL WARNING
CHAPTER 2. STRUCTURE AND FUNCTION
2.1 BODY
A. CYLINDER HEAD
B. CYLINDER BLOCK
C. CRANKSHAFT
D. PISTON AND PISTON RINGS
E. CONNECTING ROD
F. CAMSHAFT
G. FUEL CAMSHAFT
H. ROCKER ARM ASSEMBLY
I. INLET AND EXHAUST VALVES
J. TIMING GEARS
K. FLYWHEEL
2.2 LUBRICATING SYSTEM
A. FLOW OF LUBRICATING OIL
B. OIL PUMP
C. OIL FILTER AND RELIEF VALVE
D. OIL PRESSURE SWITCH
2.3 COOLING SYSTEM
A. FLOW OF COOLING WATER
B. WATER PUMP
C. THERMOSTAT
D. RADIATOR
E. RADIATOR CAP
2.4 FUEL SYSTEM
A. FLOW OF FUEL
B. FUEL FILTER
C. FUEL FEED PUMP
D. FUEL INJECTION PUMP
E. FUEL INJECTION NOZZLE
F. GOVERNOR AND IDLE COMPENSATING
PART 2 ENGINE