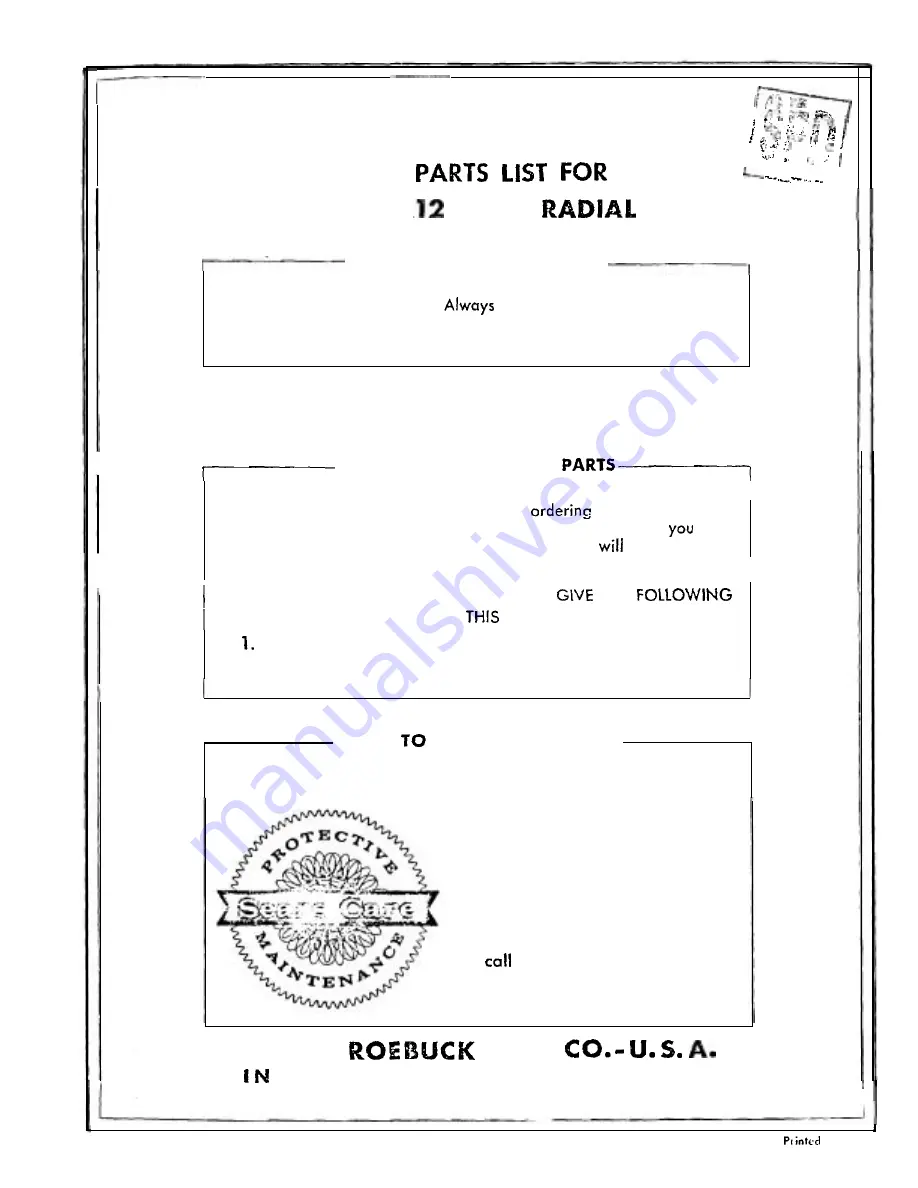
...
ASSEMBLY,
OPERATING
INSTRUCTIONS
,
...
.
.
...
AND
.
CRAFTSMAN
INCH
S A W
MODEL NUMBER 1 13.29501
The Model Number will b e found on a plate attached t o your saw,
a t the left side of the base.
mention the Model Number i n
a l l correspondence regarding the CRAFTSMAN RADIAL SAW or when
ordering repair parts.
C a r e f u l l y r e a d t h e instructions provided, observe t h e simple
s a f e t y precautions
and
you
w i l l h a v e m a n y hours
of
satisfactory
use from your
n e w Craftsman
tool.
H O W
TO ORDER REPAIR
All
parts listed herein may be ordered through SEARS, ROEBUCK A N D
I
CO.
or SIMPSONS-SEARS LIMITED. When
parts
by
mail from
the
catalog order house which serves the territory in which
live,
selling prices will be furnished on request or parts
be shipped a t
prevailing prices and you will be billed accordingly.
I
W H E N ORDERING
REPAIR PARTS, ALWAYS
THE
INFORMATION AS S H O W N
IN
LIST:
The PART NUMBER
3.
The
MODEL
NUMBER
1
13.29501
2.
The PART NAME
4.
The
NAME
of item
-
RADIAL SAW
COAST
COAST NATION-WIDE
SERVICE
FROM SEARS
F O R
YOUR CRAFTSMAN RADIAL S A W
SEARS, ROEBUCK
A N D
CO.
a n d
SIMPSONS-SEARS LIMITED i n Canada
back u p your investment with quick,
expert mechanical service and genu-
ine CRAFTSMAN replacement parts.
If
a n d when you need repairs or serv-
ice,
on us t o protect your invest-
ment
in this fine piece
of
equipment.
I
J
SEARS,
A N D
C A N A D A ,
S I M P S O N S - S E A R S
L I M I T E D
in
U .
S . A .
Part
No.
63161