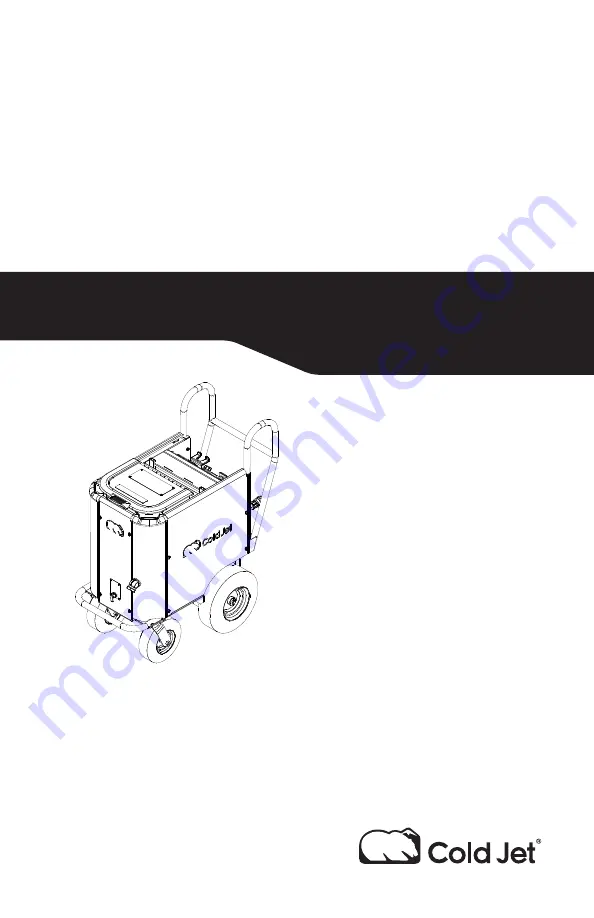
Aero
40
S
E
R
I
E
S
SAFETY
General Safety Precautions ������������� 6
Electrostatic Discharge�������������������� 7
Carbon Dioxide ������������������������������� 8
Machine Safety �������������������������������� 9
COMPONENT GUIDE
Front View �������������������������������������� 12
Rear View ���������������������������������������� 13
Control Panel ��������������������������������� 14
Blast Applicator ����������������������������� 15
OPERATION
Start Up ������������������������������������������� 18
Shut Down �������������������������������������� 19
MAINTENANCE
Troubleshooting ����������������������������� 22
Maintenance ���������������������������������� 23
Customer Service ��������������������������� 25
APPENDIX
Speciications ��������������������������������� 26
Symbol Glossary ���������������������������� 27
Blast Air Quality ����������������������������� 29
Warranty ����������������������������������������� 30
OPERATOR MANUAL
Aero 40 Series Dry Ice Blast Systems
Summary of Contents for Aero 40 HP
Page 2: ...Aero 40 S E R I E S ...
Page 4: ...Aero 40 S E R I E S ...
Page 5: ...SAFETY ...
Page 10: ...Aero 40 S E R I E S ...
Page 11: ...YOUR MACHINE ...
Page 12: ...12 12 Front View Fill Lid Air Supply Connection Bleed Valve ...
Page 13: ...13 13 Rear View Blast Hose Connection AC Power Cord Nozzle Hanger ...
Page 16: ...Aero 40 S E R I E S ...
Page 17: ...OPERATION ...
Page 20: ...Aero 40 S E R I E S ...
Page 21: ...MAINTENANCE ...
Page 24: ...Aero 40 S E R I E S ...