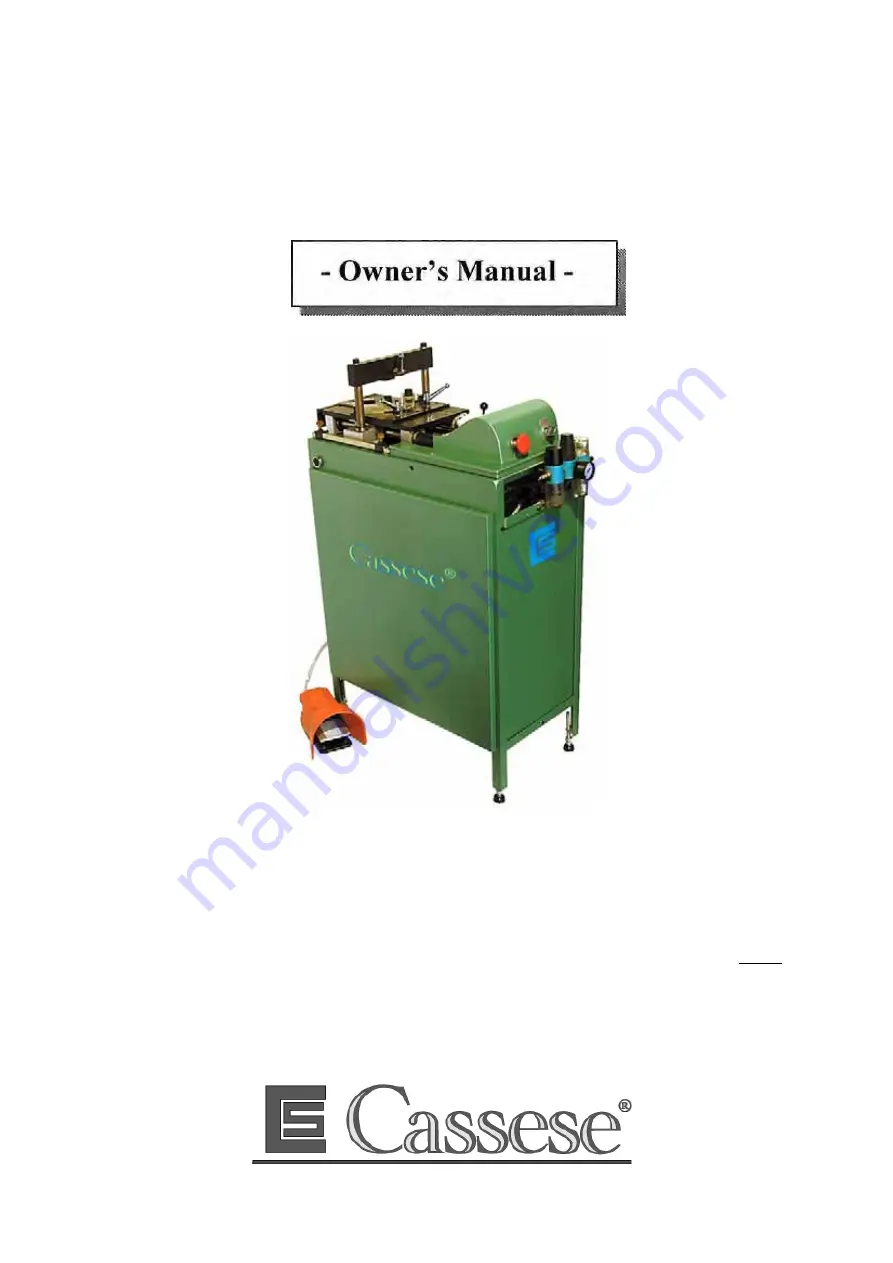
CS 276E Electronic Underpinner
SETTING UP OPERATIONS
.®
In most of cases, your Cassese supplier will set up the machine for you.
If this is not the case, first follow the separate "INSTRUCTIONS FOR SETTING UP
BEFORE OPERATION" (pages A & B)
As long as you are not instructed to do so, do not connect the machine to any air or power
source.
Factory & Head office : Zone industricllc - F - 77390 VERNEUIL L'ETANG - FRANCE
Web Site :
www.cassese.com
.