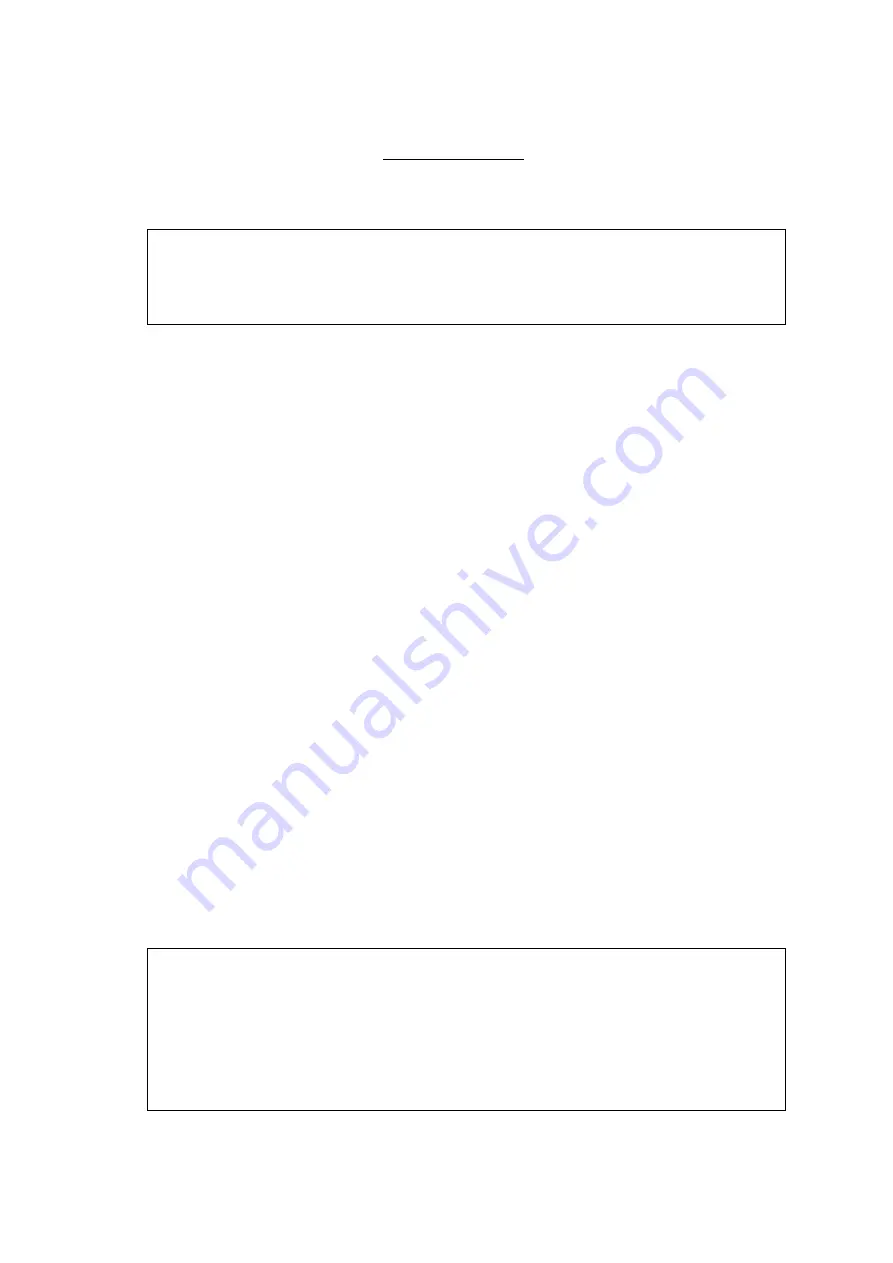
Notes for User
To use this analyzer with safety and effectiveness, please read this
manual before usage.
This manual applies to the product model NGA 6000.
1. This manual should be referred with regard to the product design and safety
assurance of the configuration.
2. For the purpose of safe confirmation, this manual should be provided to the
end user at the same time with the supply of the product.
3. Please use only in well-ventilated place.
4. This product should not be washed/polished by volatile or toxic
chemical materials like thinner.
5. Please don't use the printer until the printing paper is prepared.
6. If the equipment is wiped with a piece of moistened gauze, dry the equipment
thoroughly before use.
Using the monitor while it is wet may result in an electric shock.
7. Do not clean the terminals or the AC power inlet. Otherwise, deformation or
corrosion of contacts could occur,
which may result in contact failure and/or malfunction of the equipment.
- The contents of this manual may be changed without notice for the
purpose of functional improvement.
Copyright © NEXTECH CO., LTD.